-
- News
- Books
Featured Books
- design007 Magazine
Latest Issues
Current IssueAll About That Route
Most designers favor manual routing, but today's interactive autorouters may be changing designers' minds by allowing users more direct control. In this issue, our expert contributors discuss a variety of manual and autorouting strategies.
Creating the Ideal Data Package
Why is it so difficult to create the ideal data package? Many of these simple errors can be alleviated by paying attention to detail—and knowing what issues to look out for. So, this month, our experts weigh in on the best practices for creating the ideal design data package for your design.
Designing Through the Noise
Our experts discuss the constantly evolving world of RF design, including the many tradeoffs, material considerations, and design tips and techniques that designers and design engineers need to know to succeed in this high-frequency realm.
- Articles
- Columns
- Links
- Media kit
||| MENU - design007 Magazine
Real Time with…SMTAI 2020: ASC Makes Lemonade Out of Lemons
September 25, 2020 | Real Time with...SMTAIEstimated reading time: 11 minutes
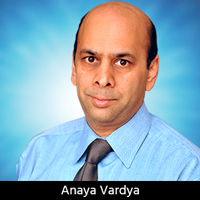
Steve Williams and Anaya Vardya, president and CEO of American Standard Circuits (ASC), discuss the upcoming virtual SMTAI show and how the company is “making lemonade out of lemons.” As they point out, there may be no face-to-face interaction, but virtual shows are open to attendees from around the world with no travel or hotel costs. Anaya explains how the COVID-19 lockdown has caused ASC to become more creative in its marketing efforts, including holding webinars and publishing two eBooks with I-Connect007. They also discuss ASC’s holistic approach to the marketplace, with a diversified product mix across various segments.
View more videos and show-related content at Real Time with… SMTAI 2020 virtual.
More from ASC:
- The Printed Circuit Designer’s Guide to… Thermal Management: A Fabricator's Perspective
- The Printed Circuit Designer’s Guide to… Flex and Rigid-Flex Fundamentals
- The Printed Circuit Designer’s Guide to… Fundamentals of RF/Microwave PCBs
I-Connect007 continues to deliver original reporting and coverage of the electronics design, electronics manufacturing, and contract manufacturing industries, including up-to-date information from the companies, associations, and supply chains globally. Find the latest news and information at I-Connect007.com.
Audio Transcript:
Steve Williams: Hi, Steve Williams here with Real Time… SMTA International, and this morning, I have Anaya Vardya, president and CEO of American Standard Circuits, with me. Good morning, Anaya.
Anaya Vardya: Good morning. How are you, Steve?
Williams: I’m doing okay. We’re going to talk a little bit about this upcoming trade show. Is this the first one you have done this year?
Vardya: Believe it or not, this is going to be the first trade show we’ve done. Unfortunately, most of the trade shows have been canceled so far this year due to COVID-19. This is the first one we’re going to be doing this year.
Williams: Is this the first one you’ve done in this virtual format?
Vardya: Correct. For a while, we had other opportunities to do virtual trade shows, and we kind of let those pass by us. This time, we decided we don’t really know when the world is going to change, and it’s about time that we jump in and figure out what a virtual trade show is all about. This one seemed really logical. Plus, the one thing that I do like about the virtual trade shows is that basically anybody in the world can attend. And given the fact that we do have a global customer base, hopefully, it will be interesting to see how it turns out for us.
The other advantage is we can also have a variety of different people participate from our perspective. Normally, in a trade show, you’re limited to two or three people. We typically don’t take any more than three people to our trade shows, and that would be what we’re limited to. In this case, we’re going to try with a greater number of participants for this trade show.
Williams: That’s a good point. On the flip side, do you think that maybe you’re going to get a better response than a face-to-face trade show because people don’t have to pay for travel?
Vardya: It goes both ways. It is likely that we see more people because people don’t have to travel as long as the show is advertised. But on the other hand, you do miss the camaraderie of a trade show, and you also miss the fact that there’s a lot of socializing that goes on after hours. And it’s a great opportunity for us to spend some real quality face-to-face time with our customers. There are pros and cons, and we’re all in a different world right now, so we have to make lemonade out of the lemons we have. That’s my approach to this. Let’s do the best we can.
Williams: It will be interesting to see how this turns out after it’s done, and maybe we’ll do a post-interview and see what the turnout was and the responses.
Vardya: Sure, we’d love to do that.
Williams: Talking about COVID-19, how has that impacted ASC, or has it?
Vardya: The biggest impact from a COVID-19 standpoint of view to ASC has been our inability to travel. That has caused us to start to do a lot more creative things. For example, one of the things we would love to do with customers is to visit them and do lunch-and-learns. Instead, we’ve now resorted to doing webinars. What’s really nice about the webinars are people can either attend live, if they’re available at that particular time, or they can listen to a recorded version because the recorded version is actually in the cloud and is available for people to register for even in the future.
The one nice thing about this is that we’re learning new and different techniques from a marketing standpoint of view. We’re also trying to make ourselves very useful to our customers and potential customers by adding the available resources. That has been one. And then the other thing is we have released a couple of e-books this year, too. Part of what we’re trying to do is, again, make the most of the current situation and try to figure out creative ways to approach our customers and create value for our customers and potential customers.
Williams: Have you had to put in place any internal practices to deal with the COVID-19 as far as employees and visitors?
Vardya: Absolutely. While we are letting visitors in the facility, we do have some fairly strict protocols. For example, every day, when an employee comes in, they have to go through a temperature check, and they also have to tell us that their health is in good condition. We also have similar checklists for our visitors to make sure that they’re as healthy as they know they are.
And then, obviously, we have masks that everybody is varying throughout the facility. We’ve instituted a lot of extra cleaning in the shops. We’re having much more cleaning done than we ever have. We have some cleaning units, or HEPA filtering units, that we’ve put in place. We’re also doing some kind of defogging on a monthly basis. We’re really trying to do everything we can to protect our employees.
Williams: Excellent. Let’s go back real quick to the webinar thing. I’ve attended a couple of them, and they’ve been done quite well. How has that been received by your audience?
Vardya: We’ve had an extremely good reception. We have somebody who actually did a little reference for us on the quality of our webinars that we can use for our marketing materials. The other thing is we are definitely getting a global audience, so we’ve seen people from almost 20–25 different countries. We’re getting some really good participation, not only in terms of registration but also in terms of people attending live.
Williams: It’s not a one-time thing if they can go back and listen to it or watch it a week later and tell other people to go watch it, right?
Vardya: Correct.
Williams: Excellent. Do you have one coming up? What’s the next one?
Vardya: We recently had one on thermal management. Basically, our next four webinars are focused on thermal management. The first three are really focused on insulated metal PCBs, where the circuit board is thermally connected to the metal, but electrically isolated. And then the last one is in the RF/microwave sector, where the metal is typically thermally and electrically connected to the circuit board.
Again, our entire next four webinars, which are every Wednesday at 11:00 a.m. CT—and you can get on our website under our resources section and register for them—are focused on various aspects of thermal management. Our whole idea is these are companion webinars to our most recent book, which is on thermal management and was released a couple of weeks ago.
Williams: Let’s talk about that. You have a new book. Why did you write it?
Vardya: We wrote the book because one of the things that isn’t talked about a lot in the industry is thermal management, and one of the things that ASC has as its core competence is its thermal management capabilities. We thought it would make sense to help educate the design community and our customers about the various pros and cons of different ways of achieving thermal management, some of the design implications, and also a little bit on how does the manufacturing process work and how is it different than building a normal printed circuit board. We wanted to get some holistic views on this topic for our customers and potential customers.
Williams: Your audience for that book is probably OEMs and designers?
Vardya: Yes, I would say primarily, but it’s really for anybody that wants to learn more about that field. A lot of people that wonder, “How does the manufacturing process work in this case? What are the differences?” It highlights some of those aspects also, but again, it’s primarily meant for the design community that can use the book to really see where they can apply those kinds of concepts and how those kinds of concepts can help them. And if they are already designing boards with thermal management techniques, maybe it gives them ideas on some things that they didn’t realize they could do, or it at least brings up questions in their minds so that they can come in and talk to us.
Williams: Good. How has the book been received?
Vardya: We’re getting a lot of downloads so far. Again, it’s relatively new. In the first week, there were around 400 downloads, which is really good for a brand-new book, especially on a very specialized topic.
Williams: Excellent. As we’re coming to a close, I saw a recent video with John Bushie, and he talked about some new equipment you have recently. What else is going on at American Standard as far as anything new or exciting with technology, equipment, or people? What’s the update?
Vardya: Currently, our focus is really on improving our flex/rigid-flex capability, and also our HDI capability. Those are the primary two things that we continue to have a high level of focus on. The reality is that we continue to work on our metal back also, but the two areas that are of high focus right now are flex/rigid-flex and our HDI capability.
We’re also working on implementing the Averatek A-SAP™ process that will really result in our ability to build finer lines and spaces and build circuits that have no copper on it. The advantage or the reason for that is because there are many implantable devices that require circuit boards that you cannot have copper in them, so you end up having gold and platinum as the conductors. That’s something else that we’re looking at right now.
In terms of equipment, we recently added two new Hioki testers, so we are upgrading our test capability. We also have put out a purchase order to buy a new six-spindle router, and this is no ordinary router. This router is actually focused on our IMPCB business and will do a great job for all the metalwork that we’re running in our factories. We expect that unit to be coming in at the beginning of November. It will really help us both from capacity and continue to work on improving our overall capability. It doesn’t bring any new real capability, but it does significantly enhance the capability that we have on our most advanced Lenz routers right now.
Those are a few of the things that are going on from an equipment and a technology standpoint of view. Again, as you know, ASC is very focused on a number of different things. We’re absolutely focused on flex/rigid-flex and RF/microwave, but we also have a very heavy focus on the metal back sector. We’re really combining all of those together.
The other thing is that we’re also working on improving our quality certifications. We’re almost done with doing all the prep work for our medical certifications, so we should be going for that pretty soon. That has, unfortunately, been impacted by COVID-19. We need to be able to get auditors in and things like that. And then the other thing that we’re also working on is the IPC-1791, which is the trusted supplier certification. Those are the two things that we have going on from a quality standpoint of view.
We’re really looking at this holistically. We’re not only looking at equipment, but we’re also looking at what we can do from a process standpoint of view and what we can do from our quality certification standpoint of view. It’s just continuing to improve our capabilities.
Williams: There are not many more merit badges you can get. You pretty much have them all.
Vardya: It has been interesting; that’s for sure.
Williams: Excellent. Any final words?
Vardya: Again, we’re really focused on a holistic approach to the marketplace. We’re looking for a diversified product mix and a diversified set of markets. Our focus is really to try to do a good job for our customers and create resources for them in this tough time.
Williams: I go to a lot of shops, and I see a lot of people, including some of your customers. And I can’t think of anybody else in the industry who is as well-respected as American Standard. You are just doing a fantastic job.
Vardya: Thank you, Steve. I appreciate your feedback.
Williams: Absolutely. Alrighty, Anaya. Thanks for your time.
Vardya: Thank you.
Williams: Once again, this is Steve Williams with Real Time with… SMTA International. Thanks for watching.
Suggested Items
The Evolution of Picosecond Laser Drilling
06/19/2025 | Marcy LaRont, PCB007 MagazineIs it hard to imagine a single laser pulse reduced not only from nanoseconds to picoseconds in its pulse duration, but even to femtoseconds? Well, buckle up because it seems we are there. In this interview, Dr. Stefan Rung, technical director of laser machines at Schmoll Maschinen GmbH, traces the technology trajectory of the laser drill from the CO2 laser to cutting-edge picosecond and hybrid laser drilling systems, highlighting the benefits and limitations of each method, and demonstrating how laser innovations are shaping the future of PCB fabrication.
Day 2: More Cutting-edge Insights at the EIPC Summer Conference
06/18/2025 | Pete Starkey, I-Connect007The European Institute for the PCB Community (EIPC) summer conference took place this year in Edinburgh, Scotland, June 3-4. This is the third of three articles on the conference. The other two cover Day 1’s sessions and the opening keynote speech. Below is a recap of the second day’s sessions.
Day 1: Cutting Edge Insights at the EIPC Summer Conference
06/17/2025 | Pete Starkey, I-Connect007The European Institute for the PCB Community (EIPC) Summer Conference took place this year in Edinburgh, Scotland, June 3-4. This is the second of three articles on the conference. The other two cover the keynote speeches and Day 2 of the technical conference. Below is a recap of the first day’s sessions.
Preventing Surface Prep Defects and Ensuring Reliability
06/10/2025 | Marcy LaRont, PCB007 MagazineIn printed circuit board (PCB) fabrication, surface preparation is a critical process that ensures strong adhesion, reliable plating, and long-term product performance. Without proper surface treatment, manufacturers may encounter defects such as delamination, poor solder mask adhesion, and plating failures. This article examines key surface preparation techniques, common defects resulting from improper processes, and real-world case studies that illustrate best practices.
RF PCB Design Tips and Tricks
05/08/2025 | Cherie Litson, EPTAC MIT CID/CID+There are many great books, videos, and information online about designing PCBs for RF circuits. A few of my favorite RF sources are Hans Rosenberg, Stephen Chavez, and Rick Hartley, but there are many more. These PCB design engineers have a very good perspective on what it takes to take an RF design from schematic concept to PCB layout.