-
- News
- Books
Featured Books
- design007 Magazine
Latest Issues
Current IssueAll About That Route
Most designers favor manual routing, but today's interactive autorouters may be changing designers' minds by allowing users more direct control. In this issue, our expert contributors discuss a variety of manual and autorouting strategies.
Creating the Ideal Data Package
Why is it so difficult to create the ideal data package? Many of these simple errors can be alleviated by paying attention to detail—and knowing what issues to look out for. So, this month, our experts weigh in on the best practices for creating the ideal design data package for your design.
Designing Through the Noise
Our experts discuss the constantly evolving world of RF design, including the many tradeoffs, material considerations, and design tips and techniques that designers and design engineers need to know to succeed in this high-frequency realm.
- Articles
- Columns
- Links
- Media kit
||| MENU - design007 Magazine
Real Time with… SMTAI 2020: Technical Conference Review
October 6, 2020 | Real Time with...SMTAIEstimated reading time: 16 minutes
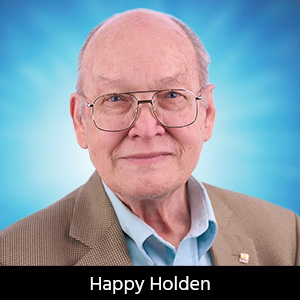
SMTAI 2020, which was converted to a virtual event, took place from September 28–30. I attend every year, but since there was no keynote in the virtual format, I went straight to the technical conference. This event covered a broad range of topics related to everything in assembly. Over 90 technical presentations are available, but this report covers just some of the sessions I attended.
Hiroshi Komatsu, Connectec Japan Corporation
#150: 10-Micron Pitch Wiring and Bump on Substrate Formed by Imprinting Technology to Apply Low-Temperature Flip-Chip Bonding for Low-Temperature Bonding, and Fine-Pitch, Imprinting, CTE
The theme of this presentation was a new process for the minimum bump pitch in flip-chip bonding. It is limited by the difference in expansion or shrinkage caused by the CTE mismatch between the chip and the substrate. It has been exceedingly difficult to achieve a bonding pitch of 35 microns or less in the conventional technology using solder.
Due to this technical limitation, the integration of hetero-chips with a large number of pin count on a substrate was intensively studied using 2.5D LSIs that typically use an interposer, which stacks chips three-dimensionally using a through-silicon via (TSV). However, the manufacturing technology, such as a silicon interposer and TSV used for these 2.5D LSIs, is an expensive process.
In this study, Komatsu reported a narrow-pitch bonding technology based on low-temperature flip-chip bonding using silver conductive paste as bumps. In this technology, a conductive paste was used to simultaneously form wiring and bump with the pitch of 10 microns on the substrate by using an imprinting method and non-conductive paste dispensing, followed by flip-chip bonding and curing at 140°C to enhance the bonding strength and reduce the resistance of the conductive paste. This allows the use of organic substrates like polyimide and PET film.
To form wiring and bump with the pitch of 10 microns simultaneously on the substrate, the final wiring and bump shape is formed in advance as a master mold, and this is transferred to a replica mold to form an inverted shape. Further, a conductive paste is filled in the concavity of the replica mold and then transferred to the substrate. Three examples were shown using an organic substrate and the low-temperature bonding technique that otherwise could not be applied to packages.
Figure 1: Low-temperature FCB IoT application.
Figure 2: Low-temperature FCB process flow.
Charles Woychik, i3 Microsystems Inc.
#151: 3D Integration Using Heterogeneous System-in-Package (HSiP) Technology FOWLP, Reconstituted Wafers, Multi-Chip Module, Embedded Die
An interposer with embedded semiconductor dies and passive devices has been fabricated using a heterogeneous system-in-package (HSiP) technology to create a highly dense integrated multi-chip module (MCM) package solution. This technology is based on fan-out wafer-level packaging (FOWLP) technology, which consists of a molded core wafer having embedded devices, through mold vias (TMVs), and passive devices, along with buildup circuitry layers on both sides of the molded core wafer.
This HSIP technology can integrate multiple die and passives to achieve maximum device packing, which is molded using an epoxy-based silica filled molding compound to create a reconstituted wafer. To maintain a flat module, it is necessary to balance the amount of Cu in both the front and back layers to achieve the neutrality of the module bow during thermal excursions. To create the buildup layers, a first dielectric material is deposited over the reconstituted wafer, vias are created, and then the Cu circuitry is formed. This new process was provided in detail.
This sequential process is repeated until the required number of layers is formed. This same process is repeated on the backside of the wafer. After the buildup layers are produced on the molded wafer, the individual modules are diced out of the wafer. On both sides of the outer layers are ball-grid array (BGA) pads, which allow these modules to be stacked using conventional solder attach methods. Reliability testing was conducted on the new HSIP of 1,000 thermal cycles, including 0–100°C and -40–125°C.
Figure 3: The future is stacked FOWLP.
Figure 4: Test vehicle design, single slice.Page 1 of 7
Suggested Items
Driving Innovation: Direct Imaging vs. Conventional Exposure
07/01/2025 | Simon Khesin -- Column: Driving InnovationMy first camera used Kodak film. I even experimented with developing photos in the bathroom, though I usually dropped the film off at a Kodak center and received the prints two weeks later, only to discover that some images were out of focus or poorly framed. Today, every smartphone contains a high-quality camera capable of producing stunning images instantly.
Hands-On Demos Now Available for Apollo Seiko’s EF and AF Selective Soldering Lines
06/30/2025 | Apollo SeikoApollo Seiko, a leading innovator in soldering technology, is excited to spotlight its expanded lineup of EF and AF Series Selective Soldering Systems, now available for live demonstrations in its newly dedicated demo room.
Indium Corporation Expert to Present on Automotive and Industrial Solder Bonding Solutions at Global Electronics Association Workshop
06/26/2025 | IndiumIndium Corporation Principal Engineer, Advanced Materials, Andy Mackie, Ph.D., MSc, will deliver a technical presentation on innovative solder bonding solutions for automotive and industrial applications at the Global Electronics A
Fresh PCB Concepts: Assembly Challenges with Micro Components and Standard Solder Mask Practices
06/26/2025 | Team NCAB -- Column: Fresh PCB ConceptsMicro components have redefined what is possible in PCB design. With package sizes like 01005 and 0201 becoming more common in high-density layouts, designers are now expected to pack more performance into smaller spaces than ever before. While these advancements support miniaturization and functionality, they introduce new assembly challenges, particularly with traditional solder mask and legend application processes.
Knocking Down the Bone Pile: Tin Whisker Mitigation in Aerospace Applications, Part 3
06/25/2025 | Nash Bell -- Column: Knocking Down the Bone PileTin whiskers are slender, hair-like metallic growths that can develop on the surface of tin-plated electronic components. Typically measuring a few micrometers in diameter and growing several millimeters in length, they form through an electrochemical process influenced by environmental factors such as temperature variations, mechanical or compressive stress, and the aging of solder alloys.