-
- News
- Books
Featured Books
- design007 Magazine
Latest Issues
Current IssueProper Floor Planning
Floor planning decisions can make or break performance, manufacturability, and timelines. This month’s contributors weigh in with their best practices for proper floor planning and specific strategies to get it right.
Showing Some Constraint
A strong design constraint strategy carefully balances a wide range of electrical and manufacturing trade-offs. This month, we explore the key requirements, common challenges, and best practices behind building an effective constraint strategy.
All About That Route
Most designers favor manual routing, but today's interactive autorouters may be changing designers' minds by allowing users more direct control. In this issue, our expert contributors discuss a variety of manual and autorouting strategies.
- Articles
- Columns
- Links
- Media kit
||| MENU - design007 Magazine
Estimated reading time: 4 minutes
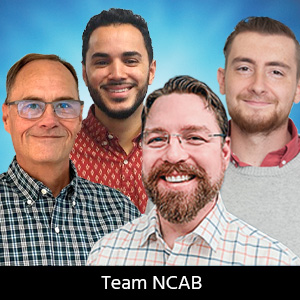
Fresh PCB Concepts: 4 Characteristics to Consider When Selecting PCB Base Materials
Selecting the correct material is critical if you want your circuit board to survive the assembly process or come out of the assembly process in good condition. In this column, I will explain the four main characteristics from the IPC-4101 material specification that are critical in finding the performance of your base material.
I have placed these in order of importance and draw attention to why I list Td ahead of Tg. There is an industry-wide misunderstanding that Tg is the most critical attribute to consider when selecting material, but I urge you to consider the Td as the more important material attribute, as this value determines the material’s survivability or capability to withstand the high temperatures seen during reflow.
Td: Decomposition Temperature
Td is a measure of the degradation of the material. The method used is thermogravimetric analysis (TGA), which measures when 5% of the material is lost by weight—the point at which reliability is compromised, and delamination may start to occur. It is important to understand that the value given is not a fixed value; it is tested according to IPC-TM-650 2.4.24.6 (5% weight loss) in N² gas:
- 5.3.1: Place the sample in the TGA and measure its mass
- 5.3.2: Heat the sample at a rate of 10°C/min from ambient to 550°C
- 5.3.3: Record the temperature, Td (2%), at which the mass of the sample is 2.0% less than its mass measured at 50°C
- 5.3.4: Record the temperature, Td (5%), at which the mass of the sample is 5.0% less than its mass measured at 50°C
Higher-reliability PCBs or PCBs that operate in demanding conditions will require a Td greater than or equal to 340°C (644°F).
Tg: Glass Transmission Temperature
Tg is a value of the temperature at which the material changes from a reasonably stiff, glass-like material to a more elastic and bendable plastic-like material. Above Tg, the material’s properties will change, such as the expansion of the material, meaning above Tg materials tend to expand more.
It’s important to know that materials can have the same Tg yet different CTEs, and the material changes heavily above this point (post-Tg). Of course, lower CTE is better. Equally, some materials can have higher Tg values yet also have a higher or worse coefficient of thermal expansion post-Tg.
This point is often measured by thermomechanical analysis (TMA) or differential scanning calorimetry (DSC). A common value on standard materials is 130–140°C (266–284°F). When testing using TMA methods (IPC-TM-650 2,4,25), it is very important that the difference between any Tg results (delta between Tg2 and Tg1) is very short as this means that the lamination of the multilayer took place well with regards to the transmission of pressure and temperature across the manufacturing panel and through the stack.
CTE: Coefficient of Thermal Expansion (Z-Axis)
This is a measure of how much the base material will expand when heated. When considering lead-free applications, the most referenced factor can be that of Z-axis expansion. This can be measured as PPM/°C before and after Tg, and also as a percentage over a temperature range. Typically, above Tg, we see that the expansion is greater. If the CTE is insufficient or too high in the material, then failures can occur, such as a fracture or delamination during assembly as the material expands rapidly above Tg. CTE is also a potential cause for PTH failure as excessive expansion puts undue stress on the through-holes during the thermal excursion (Figure 1).
Figure 1: This image shows the difference between Tg ratings and also the impact of higher CTE values. Materials B and C have the same Tg (Tg1) but different CTE (material C is higher) values. Material A has a lower Tg (Tg1) but a low CTE, so while it passes Tg sooner than the other two, the lower CTE means it does not expand (Z-axis) as much as material C.
Time to Delamination (T260, T280, T300)
This is a method in which the board is tested, using a TMA, to determine the time it takes for an event to occur such that the thickness is irreversibly changed at a pre-defined temperature. The term irreversibly changed is seen as the point at which the specimen delaminates.
Common temperatures referenced within IPC-4101 are:
- T260: 260°C (500°F)
- T288: 288°C (550°F)
- T300: 300°C (572°F)
Ownership of the material selection lies with the customer, the stakeholder who truly knows the processes and the demands of the project and what the boards will be exposed to (reflow time + temperature + number of reflow cycles) and what is needed to survive.
Your supplier should be able to recommend materials that meet the demands of IPC-4101 specification sheets, and these are based on some product and process parameters. To select the most suitable material for your projects, it’s important to know how you want your material to perform and use the characteristics as defined in the IPC-4101 specification, and specifically if you can define the specification sheet or slash sheet. This will help immensely.
Jeffery Beauchamp is a field application engineer at NCAB Group.
More Columns from Fresh PCB Concepts
Fresh PCB Concepts: Designing for Success at the Rigid-flex Transition AreaFresh PCB Concepts: More Than Compliance—A Human-centered Sustainability Approach
Fresh PCB Concepts: Assembly Challenges with Micro Components and Standard Solder Mask Practices
Fresh PCB Concepts: The Power of a Lunch & Learn for PCB Professionals
Fresh PCB Concepts: Key Considerations for Reliability, Performance, and Compliance in PCBs
Fresh PCB Concepts: Traceability in PCB Design
Fresh PCB Concepts: Tariffs and the Importance of a Diverse Supply Chain
Fresh PCB Concepts: PCB Stackup Strategies—Minimizing Crosstalk and EMI for Signal Integrity