-
- News
- Books
Featured Books
- design007 Magazine
Latest Issues
Current IssueAll About That Route
Most designers favor manual routing, but today's interactive autorouters may be changing designers' minds by allowing users more direct control. In this issue, our expert contributors discuss a variety of manual and autorouting strategies.
Creating the Ideal Data Package
Why is it so difficult to create the ideal data package? Many of these simple errors can be alleviated by paying attention to detail—and knowing what issues to look out for. So, this month, our experts weigh in on the best practices for creating the ideal design data package for your design.
Designing Through the Noise
Our experts discuss the constantly evolving world of RF design, including the many tradeoffs, material considerations, and design tips and techniques that designers and design engineers need to know to succeed in this high-frequency realm.
- Articles
- Columns
- Links
- Media kit
||| MENU - design007 Magazine
EIPC Technical Snapshot: Automotive Technology
October 19, 2020 | Pete Starkey, I-Connect007Estimated reading time: 7 minutes
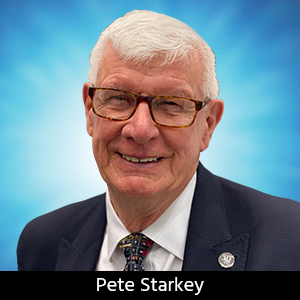
Although current circumstances have forced the postponement of its live conferences, seminars, and workshops, EIPC continues to provide a platform for the exchange and dissemination of the latest knowledge and technical information to the European interconnection and packaging industry. Its current series of technical snapshots, delivered in a webinar format, address technology challenges facing the automotive, telecom, and high-speed sectors of the industry.
The most recent session focused on automotive technology and some of the key factors driving the global automotive PCB industry. The webinar was moderated by EIPC vice-president Emma Hudson, and included presentations from three industry experts.
The first presentation, entitled “An Exploration of Advanced Semiconductor Packaging’s Effect on Automotive Electronic Hardware Design and Assembly,” came from Lenora Clark, director of autonomous driving and safety technology for ESI Automotive. Her stated objectives were to understand how megatrends were changing semiconductor package needs and design features in the automotive space and to relate these to the rest of the electronic build.
For carmakers, the choice of electronics package was driven by the megatrend, and for those involved in designing and building the electronics, it began with the semiconductor package. Although advanced semiconductor packaging had obvious applications in smartphones and data centres, it had not previously been considered a growth area for automotive. But now its growth was exponential.
The megatrends were requiring exceptional quantities of electronics in the areas of connectivity, autonomy, ride-sharing, and electrification. Advanced driver assistance systems required numerous cameras, short- and long-range radars, high-resolution lidar, and multiple ultrasonic sensors, together with the processing power to support all the electronics and the interconnection between them. Electric vehicles required semiconductor packages to support inverters, chargers, and power conversion.
Although electronics had been used in automobiles for many years, most of the packaging was legacy. Advances in technology demanded advanced packaging, and this was very new to the automotive industry. Additionally, a different architecture was evolving, where information was no longer processed locally at individual sensors but needed microcontrollers for multiple nodes.
It was necessary for multiple sensors to communicate with each other, and more advanced processing was required, with a central computer making the ultimate decision. Automotive semiconductors had higher functionality and integration at the package level and were required to work at different frequencies, voltages, and temperatures than their smartphone equivalents.
One of the biggest differences was the operational lifetime. A smartphone was only expected to work for up to three years, and a field failure rate of less than 10% was tolerable, but automotive electronics were expected to remain defect-free for up to 15 years. The applications were life-critical, so reliability was a crucial factor, and this requirement would influence package design and choice of materials.
High-density PCB designs would be essential, with more layers, finer lines and spaces, and features like stacked microvias probably unavoidable. A move to any-layer-via construction was a possibility. High-frequency applications for radar and 5G would require low-loss substrates and possibly mixed-material stack-ups with consequent fabrication difficulties. For assembly, solder alloys with enhanced reliability would be required, especially under long-term mechanical stress and thermal cycling, together with fluxes formulated to minimise electrochemical corrosion.
In her summary, Clark remarked that the automotive supply chain was unique. Existing members understood the requirements but would now need to learn new skills. New suppliers would have to learn the needs and expectations of the automotive industry.
Technology ambassador for Ventec International Group and president of EIPC, Alun Morgan gave the second presentation titled “Developing Universal Solutions to Automotive Materials Challenges.” He commented that electronics currently represented about 40% of the value of the vehicle, compared with 18% 20 years ago.
His see-through motor car illustration highlighted a series of hot-spots in automotive electric and electronic systems that required thermal management. He chose lighting as a subject for detailed discussion, commenting that automotive lighting had undergone a transition in recent years, with LEDs now predominant as they had become progressively brighter, more efficient, and less expensive. In headlights, compared with xenon or halogen-lamp, LEDs had the advantages of lower power consumption and dissipation, longer lifetime than the vehicle, colour close to daylight, and low lifetime-ownership cost. They could now be designed-in as permanent components of the vehicle.
A refresher course in thermodynamics reminded the physicists in the audience that, according to the first law, in a closed system, energy could neither be created nor destroyed but could only be converted into different forms. The second law was that heat would always flow from a region of high temperature to one of lower temperature, which was the key to thermal management.
But although LEDs had become more efficient in converting electrical energy to light, the fact remained that at least 60% of that energy was actually converted to heat. And in car headlights, that was a lot of heat to manage. Traditionally, the heat had been conducted away by attaching a heavy and bulky heat sink.
The modern way was to mount the LED on a printed circuit fabricated on an insulated metal substrate (IMS)—a laminated combination of a copper foil, a heat-conducting dielectric material, and a relatively thick metal-base plate—generally aluminium, and occasionally copper—that could then be coated with a finish known as ER1 that substantially improved the emissivity of the metal surface. Morgan demonstrated its effect with some impressively complicated mathematics.
Insulated metal substrates had become widely and successfully adopted for the thermal management of LED devices, but some challenges still had to be addressed. Morgan described a real-world case study where an automotive OEM had conducted a severe long-term thermal cycling test on an LED headlamp assembly and observed some electrical failures which had been traced to cracks in solder joints. These were shown to have been caused by shear stresses generated by differential expansion-contraction during thermal cycling in operation.Page 1 of 2
Suggested Items
Driving Innovation: Direct Imaging vs. Conventional Exposure
07/01/2025 | Simon Khesin -- Column: Driving InnovationMy first camera used Kodak film. I even experimented with developing photos in the bathroom, though I usually dropped the film off at a Kodak center and received the prints two weeks later, only to discover that some images were out of focus or poorly framed. Today, every smartphone contains a high-quality camera capable of producing stunning images instantly.
Hands-On Demos Now Available for Apollo Seiko’s EF and AF Selective Soldering Lines
06/30/2025 | Apollo SeikoApollo Seiko, a leading innovator in soldering technology, is excited to spotlight its expanded lineup of EF and AF Series Selective Soldering Systems, now available for live demonstrations in its newly dedicated demo room.
Indium Corporation Expert to Present on Automotive and Industrial Solder Bonding Solutions at Global Electronics Association Workshop
06/26/2025 | IndiumIndium Corporation Principal Engineer, Advanced Materials, Andy Mackie, Ph.D., MSc, will deliver a technical presentation on innovative solder bonding solutions for automotive and industrial applications at the Global Electronics A
Fresh PCB Concepts: Assembly Challenges with Micro Components and Standard Solder Mask Practices
06/26/2025 | Team NCAB -- Column: Fresh PCB ConceptsMicro components have redefined what is possible in PCB design. With package sizes like 01005 and 0201 becoming more common in high-density layouts, designers are now expected to pack more performance into smaller spaces than ever before. While these advancements support miniaturization and functionality, they introduce new assembly challenges, particularly with traditional solder mask and legend application processes.
Knocking Down the Bone Pile: Tin Whisker Mitigation in Aerospace Applications, Part 3
06/25/2025 | Nash Bell -- Column: Knocking Down the Bone PileTin whiskers are slender, hair-like metallic growths that can develop on the surface of tin-plated electronic components. Typically measuring a few micrometers in diameter and growing several millimeters in length, they form through an electrochemical process influenced by environmental factors such as temperature variations, mechanical or compressive stress, and the aging of solder alloys.