-
- News
- Books
Featured Books
- design007 Magazine
Latest Issues
Current IssueProper Floor Planning
Floor planning decisions can make or break performance, manufacturability, and timelines. This month’s contributors weigh in with their best practices for proper floor planning and specific strategies to get it right.
Showing Some Constraint
A strong design constraint strategy carefully balances a wide range of electrical and manufacturing trade-offs. This month, we explore the key requirements, common challenges, and best practices behind building an effective constraint strategy.
All About That Route
Most designers favor manual routing, but today's interactive autorouters may be changing designers' minds by allowing users more direct control. In this issue, our expert contributors discuss a variety of manual and autorouting strategies.
- Articles
- Columns
- Links
- Media kit
||| MENU - design007 Magazine
Estimated reading time: 8 minutes
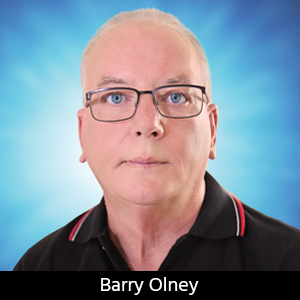
Beyond Design: Fringing Fields
Electromagnetic energy is all around us from TV to radio and communication waves and the Earth’s magnetic field and plasma shield that protect us from the sun’s solar flares (Figure 1). This activity is driven by the sun’s magnetic field. Like all physical phenomena, they tend to follow the same rules.
Figure 1: The sun’s corona discharge (solar flare) and Earth’s magnetic field.
A parallel plate capacitor (or a planar pair) has two conductors separated by a dielectric layer. Most of the energy in the structure is concentrated directly between the plates. However, some of the energy spills over into the area outside the plates. The electric field lines associated with this effect are called fringing fields. In this month’s column, I will look at how electromagnetic radiation can be emitted from the edges of planes in multilayer PCBs by the fringing fields, possibly causing electromagnetic compatibility (EMC) issues.
Fringing is the bending of the electric flux lines near the edge of the parallel plate capacitors. Fringing is also known as the edge effect. Normally, the flux lines inside the capacitor are uniform and parallel. But at the edges, the flux lines are not straight and bend slightly outward due to the geometry. Also, in a plane pair, signals passing through the cavity may intensify fringing fields (Figure 2).
Figure 2: Signals passing through a plane cavity intensify fringing fields.
When the return current flows through the impedance of a cavity between two planes, it generates voltage. Although quite small (typically in the order of 5 mV), the accumulated noise from simultaneous switching devices can become significant. Unfortunately, as core voltages drop, noise margins become tighter. This voltage, emanating from the vicinity of the signal via, injects a propagating wave into the cavity, which can excite the cavity resonances or any other parallel structure (for instance, between copper pours over planes). Other signal vias, also passing through this cavity, can pick up this transient voltage as crosstalk. And when the wave meets the PCB edge, the two reference planes form a slot antenna and will radiate noise with the potential to generate electromagnetic interference (EMI) to nearby equipment.
The more switching signals that pass through the cavity, the more noise is induced into other signals; it affects vias all over the cavity, not just the ones in close proximity to the aggressor signal vias. This cavity noise propagates as standing waves, spreading across the entire plane pair. This is the primary mechanism by which high-frequency noise is injected into cavities by signals transitioning through cavities, using each plane successively as the signal return path.
Cavity resonance also affects the power/signal return layers at the edges of the PCB. Edge effects can be particularly problematic since it is the board edges that are in such close proximity to the chassis; hence, the radiation fields can induce currents into the chassis frame.
When the cavity has open end boundary conditions, resonances arise when a multiple of half wavelengths can fit between the ends of the cavity. Figure 3 shows the cavity resonance of a plane pair with a resonant frequency of 1 GHz. If the signal clock frequency (or harmonics) are multiples of 1 GHz, then noise can be injected into the plane cavity. When the clock or data harmonics overlap with the cavity resonant frequencies, there is the potential for long-range coupling between any signals that run through the cavity. This is one reason why all return planes should be GND layers so that stitching vias between GND planes can be placed adjacent to each signal via transition to minimize the possibility of exciting the cavity resonance.
Figure 3: Amplitude at the far end of planes as input frequency is swept. (Source: Eric Bogatin)
Cavity resonances are (at first) a signal integrity issue, but the amplification of cavity resonance excited by fast rise time signals at high frequencies can also contribute to electromagnetic emissions. The frequency components of the voltage noise are related to the peak impedance of the cavity and the frequency components of the return currents. In any complex system, with typical interconnect density, avoiding signal layer transitions is not practicable and is an issue that designers must live with. However, one can learn to avoid injecting excessive noise into the cavity or at least minimize the impact.
Figure 4 gives an example of a signal trace on the top microstrip layer routed outside the reference plane area. I see this all the time when I analyze PCBs. The signal path is very close to the edge of the PCB, and the reference planes are not located directly under the trace to provide full field coverage. The electric fields (blue) tend to couple to the plane edges, whereas the magnetic fields (red) radiate outward omnidirectionally. The fringing effect creates a very “hot” area and will radiate and possibly create coupling issues to nearby circuits, cables, and slots in enclosures.
Figure 5 illustrates the cross-section on a microstrip trace, and its associated plane return current distribution (red). Where the electric fields (blue) are more tightly coupled to the plane directly below the trace, the return current also exhibits tighter coupling. But where the field spreads out from the trace, the larger loop area between the signal and the return current path increases the inductance.
Figure 5: Microstrip plane return current distribution.
Return current tends to couple to the signal conductor, falling off in intensity, with the square of increased distance. A stripline (inner layer) return current distribution is narrower with the fields more intense above and below the trace. The electric field spreads out to approximately three times the width of the trace (on both sides), so it is important to ensure there is enough plane coverage to prevent radiation.
To reduce emissions and increase immunity, when routing a PCB, try to avoid positioning critical signals close to the edge of the board. This creates a more robust system for electromagnetic compatibility.
There are various approaches pertaining to reducing radiation edge effects from the PCB. In many cases, energy can be reflected, possibly creating additional internal cavity resonance effects and coupling to internal vias, also resulting in increased radiation. When plane pairs resonate, their emissions come from the fringing fields at the board edges. With ground/power plane pairs, edge-fired emissions can be reduced by reducing the plane separation and lowering the AC impedance. Alternatively, make the power planes slightly smaller (~200 mils) than the GND plane. This modifies the pattern of the fringing fields, pulling them back from the edge, and may help reduce emissions to some extent.
Edge plating, as the name suggests, is the process of plating the edges around the PCB. I first saw this technique used at NEC back in 1994. This is an elegant (but expensive) solution to prevent emissions from extremely high-speed SERDES signals on terabit routers, etc. but is an overkill for a typical high-speed design.
Another way to mitigate this problem is to create a via fence stitched to ground around the perimeter of the PCB. If the spacing between the stitching vias is less than or equal to one-eighth of a wavelength, the via fencing will appear as a short circuit, causing the propagating wave to be reflected back to the source rather than being launched from the PCB edge.
A post-production solution is to employ cavity resonance absorber material applied along the edge of the PCB, which dissipates the edge radiation from the PCB without using additional board real estate. It also reduces the possibility of board resonance problems by dissipating the energy and not reflecting the energy back into the interior of the board. However, it is always best to fix the problem at the source rather than applying as a quick fix after production.
Key Points
- Fringing is the bending of the electric flux lines near the edge of the parallel plate capacitors. A signal passing through a plane cavity may intensify fringing fields.
- As core voltages drop, noise margins become tighter.
- Signals passing through a plane cavity inject propagating waves, which can excite the cavity resonances.
- When the wave meets the PCB edge, the two reference planes form a slot antenna and will radiate noise.
- The cavity noise propagates as standing waves spreading across the entire plane pair.
- When the cavity has open end boundary conditions, resonances arise when a multiple of half wavelengths can fit between the ends of the cavity.
- Return current tends to couple to the signal conductor, falling off in intensity with the square of increased distance.
- Avoid positioning critical signals close to the edge of the board.
- Edge plating is an elegant (but expensive) solution to prevent emissions from extremely high-speed SERDES signals.
- GND stitching vias are placed at one-eighth of a wavelength as a short circuit, causing the propagating wave to be reflected back to the source.
- Edge radiation should be eliminated at the source.
Further Reading
- Barry Olney, “Beyond Design: Plane Cavity Resonance,” The PCB Design Magazine, September 2017.
- Barry Olney, “Beyond Design: Mythbusting—There Are No One-Way Trips!” The PCB Design Magazine, April 2014.
- Barry Olney, “Beyond Design: The 10 Fundamental Rules of High-Speed PCB Design, Part 3,” Design007 Magazine, November 2018.
- Basu (VU2NSB), “Solar Activity and Ionosphere,” VU2NSB, November 19, 2019.
- Mast Technologies, “Reducing PCB Edge Fringing.”
- Larry D. Smith and Eric Bogatin, Principles of Power Integrity for PDN Design—Simplified, Pearson, March 2017.
- Eric Bogatin, “What is the resonant frequency of a cavity? Rule of Thumb #30,” EDN, July 19, 2016.
- Arturo Mediano, “Avoid Critical Signals in Edges of the PCB,” In Compliance, December 27, 2018.
- Bert Simonovich, "Controlling Electromagnetic Emissions From PCB Edges in Backplanes,” Signal Integrity Journal, January 18, 2017.
This column originally appeared in the October 2020 issue of Design007 Magazine.
More Columns from Beyond Design
Beyond Design: Effective Floor Planning StrategiesBeyond Design: Refining Design Constraints
Beyond Design: The Metamorphosis of the PCB Router
Beyond Design: Radiation and Interference Coupling
Beyond Design: Key SI Considerations for High-speed PCB Design
Beyond Design: Electro-optical Circuit Boards
Beyond Design: AI-driven Inverse Stackup Optimization
Beyond Design: High-speed Rules of Thumb