-
- News
- Books
Featured Books
- design007 Magazine
Latest Issues
Current IssueAll About That Route
Most designers favor manual routing, but today's interactive autorouters may be changing designers' minds by allowing users more direct control. In this issue, our expert contributors discuss a variety of manual and autorouting strategies.
Creating the Ideal Data Package
Why is it so difficult to create the ideal data package? Many of these simple errors can be alleviated by paying attention to detail—and knowing what issues to look out for. So, this month, our experts weigh in on the best practices for creating the ideal design data package for your design.
Designing Through the Noise
Our experts discuss the constantly evolving world of RF design, including the many tradeoffs, material considerations, and design tips and techniques that designers and design engineers need to know to succeed in this high-frequency realm.
- Articles
- Columns
- Links
- Media kit
||| MENU - design007 Magazine
Real Time with… AltiumLive Europe: If You Don’t Know How It’s Made, How Can You Possibly Design It?
October 26, 2020 | Pete Starkey, I-Connect007Estimated reading time: 4 minutes
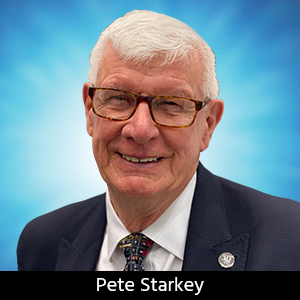
Designers attending the AltiumLive Europe 2020 Virtual Summit had the opportunity to see at first-hand how circuit boards were made to help them make informed design-for-manufacturing decisions.
Listed by Michael Gasch as the largest PCB manufacturer in Europe—and certainly one of the most modern, specialising in flex-rigid circuits, embedding technology, and other high-tech solutions—Würth Electronik welcomed AltiumLive to its Niedernhall factory to take a virtual tour. And a team of experts was on hand to provide real-time answers to questions raised by participants—of which there were more than 400.
The session was moderated by Altium multimedia marketing manager Benjamin Kitzinger. Würth PCB specialist Andreas Schilpp led the tour, and his colleagues—Alexander Staudt, Bernt Schroder, and Klaus Schill-Mulack—made up the panel.
The virtual tour was conducted in 10-minute periods, separated by Q&A sessions, and participants were also encouraged to respond to an occasional on-line multiple-choice quiz. The question asked before the start was how many steps there were in producing a 10-layer multilayer in basic technology—click on a number and submit. The answer was 65, to the surprise of a few who clearly had no hands-on experience of PCB fabrication.
Andreas Schilpp set off on his tour, accompanied by a cameraperson. After showing examples of a variety of product types, he began the manufacturing sequence with the issue of inner layer materials, following them into the yellow safelight area for photoresist lamination and laser direct imaging, then developing, acid etching and resist stripping, bonding treatment, and automated optical inspection before lay-up and hot-press bonding.
There was a Q&A break, with questions about the number of employees (approximately 180, covering 24 hours over six days), whether single-image or panelised data was preferred (single-image so that material usage could be optimised by panelisation in-house), and registration systems (post-etch punch and pin lamination for small batch, or optical alignment, spot weld, and mass-lamination for series production).
And a second quiz: What was the smallest drill diameter used in production? The answer was 0.1 mm.
Back on the virtual tour, Schilpp visited the drill shop: X-ray tooling hole optimisation, robotic flash trimming, and edge dressing, and then drilling. For mechanical drilling, there was a choice of single-spindle modules or multi-spindle machines, with 300,000 rpm spindle speed capability—all with auto-loading facilities. Laser drilling was used for microvia HDI and flex-rigid work. The next process was through-hole metallisation before photoresist lamination for outer layer laser direct imaging, followed by copper and tin pattern plating, resist stripping, alkaline etching and tin stripping, spray coating solder mask, and laser direct imaging. He commented that solder mask application and imaging for certain jobs was by 3D printing.
Another Q&A break brought a question about the cost impact of smaller drilled vias, 0.2 mm versus 0.3 mm. The answer was about 10%. There was also a question about improvement in capability since the factory was rebuilt, re-equipped, and re-commissioned in 2016. They said, “The name’s the same, but everything else is new!”
Next, there was a query about the difference between acid and alkaline etching—acid for photoresist, and alkaline for tin resist. Was copper reclaimed? Yes, copper was recovered from etchant and sent for recycling. What data format was preferred? Würth received about 250 data sets per day and was equipped to accept any format—typically extended Gerber or ODB++; IPC 2581 was seen occasionally but was not expected to replace Gerber. What were the benefits of 3D printing of solder mask? All of the benefits associated with additive processing, and the technology was becoming more widely used.
The third quiz question was about the volume of rinse water used per day, with a choice of answers from 200–20,000 cubic metres. Opinions were widespread, but the actual volume was 2,000 cubic metres.
In the final part of the virtual tour, Schilpp visited the finishing department, where electroless nickel immersion gold was the normal choice for flex-rigid work. Controlled-depth routing was used to remove excess rigid material from the flexible areas of flex-rigid circuits, and through-routing was used to profile individual circuits, so they could be removed from the panel. A pico-laser was available for profiling flexible material. Finished circuits were washed and optically inspected, then electrically tested with flying-probe equipment. Samples were release-tested in the laboratory before final inspection and shipping.
A concluding Q&A session responded to queries about providing customers with manufacturing design rules, including whether electrical testing was carried out 100% as standard (yes), what alternative profiling methods were available (V-scoring, sawing), what extra steps were involved when controlled impedance was required (several, beginning with calculating the stackup), and whether laser drilling would replace mechanical drilling. In all, 120 questions were answered live before time ran out, and several more would subsequently be responded to by email.
The closing quiz question was to guess the approximate cost of a PCB manufacturing plant with a capacity of 400 square metres per day. Most participants underestimated the actual cost of US$175 million!
It was a most informative hour and a quarter! Thank you, Würth Electronik and AltiumLive Europe.
Suggested Items
Driving Innovation: Direct Imaging vs. Conventional Exposure
07/01/2025 | Simon Khesin -- Column: Driving InnovationMy first camera used Kodak film. I even experimented with developing photos in the bathroom, though I usually dropped the film off at a Kodak center and received the prints two weeks later, only to discover that some images were out of focus or poorly framed. Today, every smartphone contains a high-quality camera capable of producing stunning images instantly.
Hands-On Demos Now Available for Apollo Seiko’s EF and AF Selective Soldering Lines
06/30/2025 | Apollo SeikoApollo Seiko, a leading innovator in soldering technology, is excited to spotlight its expanded lineup of EF and AF Series Selective Soldering Systems, now available for live demonstrations in its newly dedicated demo room.
Indium Corporation Expert to Present on Automotive and Industrial Solder Bonding Solutions at Global Electronics Association Workshop
06/26/2025 | IndiumIndium Corporation Principal Engineer, Advanced Materials, Andy Mackie, Ph.D., MSc, will deliver a technical presentation on innovative solder bonding solutions for automotive and industrial applications at the Global Electronics A
Fresh PCB Concepts: Assembly Challenges with Micro Components and Standard Solder Mask Practices
06/26/2025 | Team NCAB -- Column: Fresh PCB ConceptsMicro components have redefined what is possible in PCB design. With package sizes like 01005 and 0201 becoming more common in high-density layouts, designers are now expected to pack more performance into smaller spaces than ever before. While these advancements support miniaturization and functionality, they introduce new assembly challenges, particularly with traditional solder mask and legend application processes.
Knocking Down the Bone Pile: Tin Whisker Mitigation in Aerospace Applications, Part 3
06/25/2025 | Nash Bell -- Column: Knocking Down the Bone PileTin whiskers are slender, hair-like metallic growths that can develop on the surface of tin-plated electronic components. Typically measuring a few micrometers in diameter and growing several millimeters in length, they form through an electrochemical process influenced by environmental factors such as temperature variations, mechanical or compressive stress, and the aging of solder alloys.