-
- News
- Books
Featured Books
- design007 Magazine
Latest Issues
Current IssueAll About That Route
Most designers favor manual routing, but today's interactive autorouters may be changing designers' minds by allowing users more direct control. In this issue, our expert contributors discuss a variety of manual and autorouting strategies.
Creating the Ideal Data Package
Why is it so difficult to create the ideal data package? Many of these simple errors can be alleviated by paying attention to detail—and knowing what issues to look out for. So, this month, our experts weigh in on the best practices for creating the ideal design data package for your design.
Designing Through the Noise
Our experts discuss the constantly evolving world of RF design, including the many tradeoffs, material considerations, and design tips and techniques that designers and design engineers need to know to succeed in this high-frequency realm.
- Articles
- Columns
- Links
- Media kit
||| MENU - design007 Magazine
How to Benefit From Robotic Soldering Processes
October 28, 2020 | Pete Starkey, I-Connect007Estimated reading time: 6 minutes
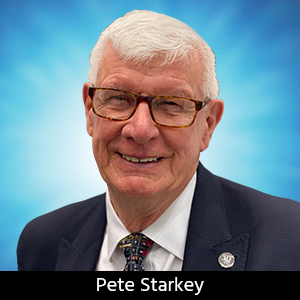
Webinars are in vogue! Current circumstances limit physical tutorials, and a webinar should offer an opportunity for online dissemination of information and transfer of knowledge. In recent months, I have attended dozens—some stimulating and informative, and many intrinsically dull and ineffective. But in my experience, the master of the technical webinar with many years’ experience of delivering first-rate events is Bob Willis—electronics assembly specialist, soldering expert, and provider of training and consultancy in electronics manufacture.
Bob’s presentation was titled “How to benefit from robotic soldering processes?” An international audience of over 200 delegates from 32 countries was keen to find out, as he presented his real-time interactive preview of the upcoming robotic soldering experience.
Bob explained that robotic soldering offered an alternative form of selectively soldering through-hole components, connectors, for example, to printed circuit boards, simulating and automating the otherwise labour-intensive process of hand soldering. With the appropriate choice of equipment and material, robotic soldering could provide increased throughput, accuracy and quality, and better consistency and repeatability than even the most skilful manual operator. And the optimum soldering profile for each individual joint could be programmed in.
He had experience with robotic soldering from as early as 2003 and commented that the technology had more recently attracted considerable interest. A wide range of equipment was currently available, and solder suppliers had developed specific materials to support the demanding requirements of medical, industrial, and automotive applications. Solder was typically supplied in the form of flux-cored wire, melted with either a precision hot iron or a laser. Bob described practical aspects of the technique, illustrating common problems and how they could be overcome with good practice, as well as discussing reliability test results with standard lead-free and higher-temperature alloys.
Why consider robotic soldering? Bob saw it as a means of reducing costs compared with wave and selective soldering and presenting an opportunity to create soldering work-cells with one operator controlling two or three separate cells. It also gave production staff the option of evaluating a new technique and extending their skill-set. Although the principles of robotic soldering had been established for several years, it was still new to many people. He admitted that he was still learning.
Focusing on practical aspects, Bob referred to work at the National Physical Laboratory (NPL) on high-temperature soldering in which he had cooperated and for which two free reports were available. An industry survey on the usage of high-temperature alloys had indicated 31% lead-tin, 31% tin-silver, 9% tin-antimony, and 8% tin-copper. As for the high-temperature robotic soldering process, 10% had used robotic iron, 4% robotic laser, 4% both, and 82% had used neither.
In the NPL high-temperature project, four-layer multilayer polyimide PCBs were assembled by robotic laser and robotic iron selective soldering using lead-tin, tin-antimony, tin-copper, and tin-silver alloys, followed by 1,000 hours static ageing at 200°C. The assemblies were subjected to microsectioning, optical and X-ray inspection, thermal shock, and peel strength measurements.
In his discussion of design rules for through-hole soldering, Bob commented that an important parameter was lead-to-hole ratio. In the case of the 96-way connectors used in the trial, the rule was pin size plus 0.010”. If the pins were square or rectangular, the diagonal dimension was used. The design rule for pad size was pin size plus 0.010”. The solder mask opening was pad size plus 0.006”.
It was preferred to reduce the number and size of thermal relief connections to inner-layer pads where possible. If necessary, certain of the pins could be clenched to ensure that the connector component was retained in position during soldering. Bob showed illustrations of hand-soldered joints using high-melting-point lead-tin-silver solder with a temperature range of 296–301°C and compared joint shapes and surface textures.
NPL had conducted trials with five different proprietary robotic soldering systems, selective laser, and robotic iron, concluding that they were not only extremely flexible and potentially faster processes than selective soldering but had the ability to define specific parameters for each joint. Bob demonstrated the use of an infra-red thermal imaging camera for monitoring and optimising conditions. Different tip configurations were available for point and drag iron-soldering, and laser systems had process monitoring capabilities. In all cases, the source of solder was a flux-cored wire with automatic feed and the option of nitrogen shielding. It was stressed that positionally accurate PCB tooling was vital.
Bob listed comprehensive operating settings for typical tip-soldering and laser-soldering robots and showed step-by-step videos of the soldering operation for each. As part of the programming procedure, besides importing the positional information from the design files, the different pad, hole and pin sizes were measured so that the volume of solder required for each joint could be calculated. Then, based on the gauge of solder wire, its feed rate could be defined.
The topic of solder wire for robotic soldering is clearly a technology area of its own. Not just the alloy metallurgy, but the geometry of the metallic component, the number and the size of the cores, and the chemistry of the flux contained therein. Bob showed several examples, cut in cross-section, and his video clips illustrated their behaviour as the temperature was increased to the melting point. Solder balling was a well-known issue in robotic soldering, caused by the sudden expansion of the flux and vaporisation of volatile material.
Applying the solder wire directly to the iron caused spitting, as did trying to work too fast, and spitting resulted in solder balls. The problem could be mitigated by scoring or piercing the wire in the feed mechanism immediately before it reached the point of fusion, to allow the flux to flow out in a controlled manner rather than explosively, and most machines now had a mechanical provision for this operation. Some assemblers also used masking plates to screen the board except for the connectors being soldered.
Bob showed examples of test patterns that could be used to compare the extent of spattering—as ever he preferred uncomplicated methods—and discussed the benefits of working with a stream of nitrogen flooding the soldering tip, using a thermal imaging camera to study the temperature effects.
A large selection of soldering tips was available, key features being temperature response, and working life. Useful working life clearly depended on conditions of use but was improved by regular cleaning, for which there was a choice of sponge, brush or air-jet devices, and by keeping the tip protected with nitrogen.
Having completed the soldering operation, what were the characteristics of the joints? Bob displayed microsections of pin-in-plated-through-hole joints produced by robotic laser soldering and robotic iron soldering, before and after heat-ageing, demonstrating the increase in intermetallic thickness. All met the criteria of IPC-610F Level 3. Pull-testing could indicate three different failure modes: tensile stress breakage of the pin, pull-out of the pin from the solder, or pull-out of the complete soldered hole from the PCB, and he showed examples of each with static photographs and high-speed video.
Bob concluded the presentation with a comprehensive catalogue of illustrations of soldering and assembly defects: board burning, mask damage, flux residues, poor thermal balance, flux spitting, solder fillet tearing, solder fillet lifting, pad lifting, copper hole-wall pull-away, inconsistent solder volume, flux bubbles, and solder balls. This set the scene for a spirited half-hour Q&A session, exemplifying the benefit of interactivity in the real-time live webinar format.
Indeed, at intervals during the presentation, Bob conducted instant audience polls, including questions like:
- Do you use robotic soldering?
- What do you see as the main benefits of robotic soldering?
- What cored wire would you most like to use?
- What IPC inspection class do you require?
Within an hour of the close of the session, the results had been analysed, presented as pie-charts, and emailed to participants.
Many thanks indeed Bob Willis for showing us the benefits of robotic soldering processes and for demonstrating how an effective technical webinar can be produced and presented.
Suggested Items
Driving Innovation: Direct Imaging vs. Conventional Exposure
07/01/2025 | Simon Khesin -- Column: Driving InnovationMy first camera used Kodak film. I even experimented with developing photos in the bathroom, though I usually dropped the film off at a Kodak center and received the prints two weeks later, only to discover that some images were out of focus or poorly framed. Today, every smartphone contains a high-quality camera capable of producing stunning images instantly.
Hands-On Demos Now Available for Apollo Seiko’s EF and AF Selective Soldering Lines
06/30/2025 | Apollo SeikoApollo Seiko, a leading innovator in soldering technology, is excited to spotlight its expanded lineup of EF and AF Series Selective Soldering Systems, now available for live demonstrations in its newly dedicated demo room.
Indium Corporation Expert to Present on Automotive and Industrial Solder Bonding Solutions at Global Electronics Association Workshop
06/26/2025 | IndiumIndium Corporation Principal Engineer, Advanced Materials, Andy Mackie, Ph.D., MSc, will deliver a technical presentation on innovative solder bonding solutions for automotive and industrial applications at the Global Electronics A
Fresh PCB Concepts: Assembly Challenges with Micro Components and Standard Solder Mask Practices
06/26/2025 | Team NCAB -- Column: Fresh PCB ConceptsMicro components have redefined what is possible in PCB design. With package sizes like 01005 and 0201 becoming more common in high-density layouts, designers are now expected to pack more performance into smaller spaces than ever before. While these advancements support miniaturization and functionality, they introduce new assembly challenges, particularly with traditional solder mask and legend application processes.
Knocking Down the Bone Pile: Tin Whisker Mitigation in Aerospace Applications, Part 3
06/25/2025 | Nash Bell -- Column: Knocking Down the Bone PileTin whiskers are slender, hair-like metallic growths that can develop on the surface of tin-plated electronic components. Typically measuring a few micrometers in diameter and growing several millimeters in length, they form through an electrochemical process influenced by environmental factors such as temperature variations, mechanical or compressive stress, and the aging of solder alloys.