-
- News
- Books
Featured Books
- design007 Magazine
Latest Issues
Current IssueProper Floor Planning
Floor planning decisions can make or break performance, manufacturability, and timelines. This month’s contributors weigh in with their best practices for proper floor planning and specific strategies to get it right.
Showing Some Constraint
A strong design constraint strategy carefully balances a wide range of electrical and manufacturing trade-offs. This month, we explore the key requirements, common challenges, and best practices behind building an effective constraint strategy.
All About That Route
Most designers favor manual routing, but today's interactive autorouters may be changing designers' minds by allowing users more direct control. In this issue, our expert contributors discuss a variety of manual and autorouting strategies.
- Articles
- Columns
- Links
- Media kit
||| MENU - design007 Magazine
Estimated reading time: 3 minutes
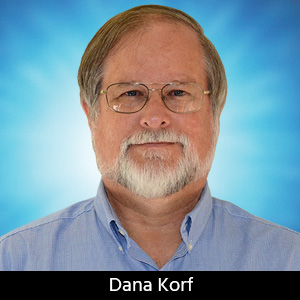
Dana on Data: Reducing PCB Specification Interpretation Issues
The PCB industry has accepted a low-quality level of provided documentation from its customers for the past several decades. It is not uncommon to hear that 90–95% of all data packages that are provided for quoting and production cannot be quoted or fabricated as provided due to missing data, wrong data, unclear requirements, and/or conflicting data.
Many documents within the data package are provided to the PCB manufacturer when an order is placed. These documents, and the specifications within, may have been used at other companies by engineers or procurement folks and brought into the new company to create a data package template. Often, there are requirements that conflict or are open to interpretation, and the designer and procurement person do not review all of the requirements for applicability or ensure that they and the manufacturer have an identical interpretation.
Resolving specification-related issues can take a lot of time, so the manufacturer may make an interpretation for un-resolved questions to quickly release the job to manufacturing. Common “top-level” specifications are IPC-6012 for rigid PCBs and IPC-6013 for flexible PCBs. Let’s review one common fabrication print note and ask, “How do you interpret this note?” (By the way, there is no singular correct answer.)
Note: “Build to the Latest Version of IPC-6012”
This note, or an equivalent note, is included on most fabrication drawings and PCB acceptance specifications for rigid boards. Sometimes, it is also included in the purchase order. In this example, IPC-6012 just changed from revision D to revision E this year. This simple requirement has many interpretations.
Which of the following interpretations do you think is correct?
- The PCB was first built at revision A1 when IPC-6012 was revision D. Now, the PCB revision has been updated from revision A1 to A2 after IPC-6012 revision E has been released.
- Does the fabricator update the A2 revision to the revision E?
- Does the manufacturer use revision D that was used on the A1 version?
- A fabricator has run 100 different part numbers for the customer for a couple of years using revision D. After IPC-6012 is updated to rev E:
- Should the manufacturer put all existing part numbers on engineering hold to be reviewed and updated to comply with revision E the next time they are ordered?
- Who will pay for this review and potential re-tooling?
- Who will verify if the changes affect the PCB performance or qualification?
- Can the fabricator ship excess inventory from the boards built to revision D under the new purchase order?
- Does the manufacturer leave these part numbers alone using IPC-6012 rev D?
I suggest giving this quiz to your team and suppliers and seeing if everyone arrives at the same answer.
What Requirements Are in IPC-6012?
IPC-6012 is an excellent document for specifying qualification and performance specifications for rigid boards. It provides solid specifications for designers and companies that do not have in-house PCB fabrication expertise. The specification is also used as an incoming acceptance specification often used to reject PCBs that do not meet the requirements.
IPC-6012 has over 20 AABUS references where it specifies that a requirement SHALL be agreed upon between the user and subscriber, as applicable. The specification requires that these are addressed prior to releasing the board for production. In my experience, this concurrence does not normally happen for commercial PCBs.
Verify the Interpretation Before the Order
Problems arise when the company designing, ordering and/or fabricating the PCB do not interpret all the referenced specifications in the same way. These potential issues can be mitigated when the entire supply chain fully understands every minute detail of each specification and agree to the interpretation in writing. Creating a general acceptance specification stating your requirements will negate having to get these answered for every part number.
If it is left open to interpretation, the requirements become a suggestion, or, as George Carlins states, "I don’t like to think of laws as rules you have to follow, but more as suggestions."
Have a happy holiday season, and I pray that 2021 will be a much safer and calmer new year.
Dana Korf is the principal consultant at Korf Consultancy LLC.
More Columns from Dana on Data
Dana on Data: Best Practices in Interpreting Drawing Notes—‘Use Latest Revision’Dana on Data: The Missing AI-NPI Link
Dana on Data: Merging 2D Electrical, 3D Mechanical Worlds
Dana on Data: Resurrecting IPC Class 1
Dana on Data: The Evolution of Fabrication Drawing
Dana on Data: The Insane PCB DFM Process
Dana on Data: eCAD PCB Design Deficiencies
Dana on Data: Nuke the Netlist