-
- News
- Books
Featured Books
- smt007 Magazine
Latest Issues
Current IssueSupply Chain Strategies
A successful brand is built on strong customer relationships—anchored by a well-orchestrated supply chain at its core. This month, we look at how managing your supply chain directly influences customer perception.
What's Your Sweet Spot?
Are you in a niche that’s growing or shrinking? Is it time to reassess and refocus? We spotlight companies thriving by redefining or reinforcing their niche. What are their insights?
Moving Forward With Confidence
In this issue, we focus on sales and quoting, workforce training, new IPC leadership in the U.S. and Canada, the effects of tariffs, CFX standards, and much more—all designed to provide perspective as you move through the cloud bank of today's shifting economic market.
- Articles
- Columns
- Links
- Media kit
||| MENU - smt007 Magazine
Estimated reading time: 6 minutes
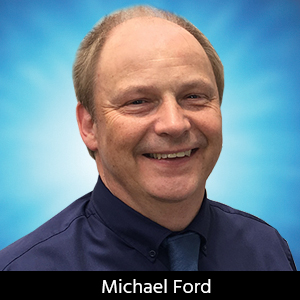
Smart Factory Insights: Changing Roles in the Digital Factory
Obviously, the level of maturity within the electronics assembly industry, in terms of core technologies, is high and relatively stable. Experts once required to have a specialized knowledge of materials and processes are giving way to those experienced in the application of automated and computerized solutions. It is time to reinvent the expectations and qualifications that we seek in managers, engineers, and production operators to attract and support a different kind of manufacturing innovation.
When SMT first came along, I naively thought that it could not be that difficult to pick up a component and place it on a PCB in the desired location, though there did seem to be challenges at times. Technology and expertise flourished, machines became faster, and materials became smaller. With PCB dimensions and spacing reducing in line with the material sizes, we saw the same challenges coming around, over and over again, related to cleaning and access for testing and inspection, for example.
After 30 years of SMT production, with an immense contribution of technology and work by people far cleverer than myself in these specialized areas, I still maintain that PCB assembly is not complicated. This perspective comes from the observation that the location at which this know-how resides has changed from once being needed in each and every SMT factory across the world to now being within the domain of the machine vendor and materials suppliers. Today, we trust the machines and materials that we buy—sophisticated, matured, yet progressive commodities that simply perform the intended work efficiently and reliably. Creating an SMT configuration to meet any line configuration requirement is as easy today as ordering off-the-shelf products, selecting the best tools for the job from any one of many vendors.
This has all coincided with the trend of experts in the core technologies leaving manufacturing either to go on to work with machine vendors or simply retiring. The key question is, “Does this create a void?” Up to fairly recently, perhaps yes, but now I don’t think that it is such a serious issue. If our minds stay in the “analog” factory of yesterday, we have everything pretty much covered, with results in terms of efficiency, productivity, flexibility, and quality being as good as they ever can be. Any incremental challenges today are met predominantly by vendors, and manufacturing can continue as is.
Of course, this is not an option. Factory-centric improvements now become the differentiators. In many areas, the consequence of variation continues to present challenges, but the details needed to identify anomalies in a timely fashion and then track the root causes are not practically possible for humans to do unaided. In areas of low labor cost, we have already seen many people with relatively low skills being thrown at these challenges, such as material and product logistics, as well as planning optimization and quality control.
As product-mix has increased, the whole of the shop floor gets into a mess, with continuous fire-fighting. This is not the profile of people that we need for smart manufacturing; in other words, we cannot replace the skilled experts that we once had with unskilled workers. As the industry has trended away from mass production toward the extreme of mass-customization, we need to reinvent the technologies that are associated with these factory-level functions.
As automated machines reduced the need for manual work in terms of core manufacturing technology and assembly activities, software automation replaces the dull and repetitive calculations done currently by people who are using tools such as Excel to perform their planning, material management, and quality control, in addition to legacy ERP or even MES systems. The way going forward in terms of factory operational improvement is digital, and the people needed are those who understand how to utilize software and systems to improve manufacturing and how to differentiate between them.
The use of real-time data within manufacturing thus far has been limited; it has been constrained by a lack of timely availability of data that has a consistent meaning and can be trusted to be used for investigative processes and decision making. The main driver toward digitalization for most companies has been the gathering of traceability data, which itself has been a haphazard affair. Thankfully, the digital manufacturing world is finally going through the revolution long promised by Industry 4.0 and smart manufacturing. Industry standards—most notably from IPC in the form of the Connected Factory Exchange (CFX), the IPC Digital Twin, exact traceability of IPC-1782, as well as the Digital Product Model Exchange (DPMX), which is also known as IPC-2581—enable completely reliable interoperability of data when used with the right tools.
Having standards in place, however, is only the start. Few applications in the realm of MES, etc., have been ready for these technology changes, but the volunteer companies behind these open industry standards are clearly setting the pace, providing an unprecedented opportunity for factory visibility, control, optimization, and quality, as well as further automation opportunity. What is really needed now in manufacturing are people with the skills to understand the use of data in manufacturing, the difference and consequence of selecting technologies, and how to bring about changes and manage manufacturing based on what the data shows.
It is quite fortunate that skills and experience in computing are growing, but manufacturing is not the most famous or attractive place to which people with those skills are attracted. But this is something that needs to change, as this is the way in which factories will differentiate themselves within the industry against their peers. The whole approach to recruitment and role definition needs to change to take advantage of technologies that are now available. We all now need to market manufacturing careers in context with this new digital age and be less concerned about the loss of past dependencies.
There is still one final challenge, however. The momentum with legacy practices within manufacturing remains strong. As manufacturing has been slow to have easy access to good data, managers within manufacturing and the supply chain have become introspective, with the whole of their professional world contained within the four walls of the factory, believing—with very decreasing merit—that many that propose such pioneering digital technologies represent a risky path and that so-called experts are simply trying to make their bad business work. For sure, unless you have the skills in-house to know what technologies and solutions are out there—which work and which do not and how they specifically relate to the needs of production—it is very easy to make a mistake and go with a company name that “you will never get fired for choosing” only to find yourself locked into a solution that is isolated from the rest of the industry, including from machines themselves that you depend on.
Trust needs to be built between incumbent senior management and the new profile of manufacturing engineers, managers, and operators. Successfully addressing new challenges always works best with an open mind. The reality is that with these new skills in new roles comes the need for training and experience in manufacturing itself. The incumbent skills are at least as important as the new ones. The successful companies will be those that create the right balance of hybrid sets of skills, manufacturing, and digital technology formed by communication, trust, and mutual respect. This is not politics, after all.
This column originally appeared in the December 2020 issue of SMT007 Magazine.
More Columns from Smart Factory Insights
Smart Factory Insights: Making Rework a Smart Business OpportunitySmart Factory Insights: The Sustainability Gold Rush
Smart Factory Insights: Today’s Manufacturing Jobs Require a New Skill Set
Smart Factory Insights: Compose Yourself, Mr. Ford
Smart Factory Insights: The Smart Business Case for Local PCB Manufacturing
Smart Factory Insights: Manufacturing Digital Twin—Spanners in the Works
Smart Factory Insights: Machines, People, and AI
Smart Factory Insights: Is Sustainability in Manufacturing a Benefit or Burden?