-
-
News
News Highlights
- Books
Featured Books
- smt007 Magazine
Latest Issues
Current IssueSpotlight on India
We invite you on a virtual tour of India’s thriving ecosystem, guided by the Global Electronics Association’s India office staff, who share their insights into the region’s growth and opportunities.
Supply Chain Strategies
A successful brand is built on strong customer relationships—anchored by a well-orchestrated supply chain at its core. This month, we look at how managing your supply chain directly influences customer perception.
What's Your Sweet Spot?
Are you in a niche that’s growing or shrinking? Is it time to reassess and refocus? We spotlight companies thriving by redefining or reinforcing their niche. What are their insights?
- Articles
- Columns
- Links
- Media kit
||| MENU - smt007 Magazine
Estimated reading time: 3 minutes
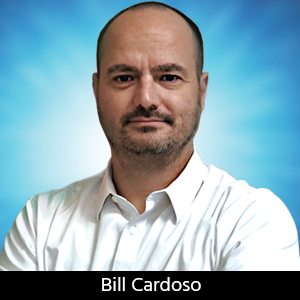
X-Rayted Files: Solving for the Limits of Human Visual Inspection
Media abounds with countless stories about human attention span—namely our shortening human attention span—sometimes blaming the very products many of us are involved in electronics manufacturing. And whether attention spans are getting shorter, or the products we make are contributing to the problem, the limits of human attention—including getting it and holding it—present real challenges for manufacturers.
While there is little definitive evidence to define human attention span, it is generally accepted that healthy adults are capable of 10–20 minutes of focused attention. Of course, we are still able to devote our attention for longer periods to a ball game or feature-length film, for instance, but that behavior involves lapses in attention and refocusing.
Because a key element of quality control in manufacturing is still good old-fashioned visual inspection, it’s important to understand the ability of operators to sustain their focus and what we can do to support their success. From individual components to final inspection of completed assemblies, visual examination by human operators makes an essential contribution to quality assurance. While the fallibility of human inspection presents challenges, there are many ways to address shortcomings, from frequent breaks to improved environmental conditions and the employment of new technology.
Error rates for visual inspection can be as low as 3–10% under the best conditions and as high as 20–30% in suboptimal conditions. Striving for those low error rates requires investment in skilled, experienced, well-trained inspectors. This also demands a comfortable environment, including good lighting, frequent breaks, and low stress levels.
From Juran’s Quality Handbook, we understand that 100% visual inspection is about 87% effective. By instituting 300% inspection, effectiveness can be increased to 99.7%. Of course, implementing triple inspection and the conditions that support it is costly and can slow production. It’s also important to understand that as defect rates go down, so does the effectiveness of visual inspection because of operator expectation bias. Of course, if you are making Hot Wheels, you might be comfortable with higher inspection errors (depending on the failure mode), but if you are a medical device manufacturer, the stakes can be much higher, and there is a demand for the lowest achievable defect rates.
Mitigating human shortcomings in vigilance is an ongoing challenge of quality control efforts. Even under ideal conditions, an inspector’s focus starts to drop off after only 15 minutes, and they should have an extended break after no more than 30 minutes. Advancements in automated sample handling and artificial intelligence are combining to provide a powerful backstop to inspection by human operators. For products that benefit from X-ray inspection, integrating these technologies with high-resolution X-ray inspection systems can support operators in identifying defects or relieve them entirely with fully autonomous X-ray machines.
But imagine the monotony of evaluating a grainy grayscale image of the same part or feature over and over. Just the thought can make your eyes roll back in your head. AI and deep learning can be trained to consistently and reliably identify defects that may be imperceptible for even the most skilled operators without ever losing focus and the risks associated with momentary gaps in attention.
Automated X-ray systems don’t get tired, don’t lose focus, and don’t waver in their consistency. Autonomous X-ray inspection can free up talented and experienced operators for other more productive tasks, and your X-ray system is never going to leave you for a better offer that comes across its LinkedIn feed.
Such systems can also be trained to address every aspect of your inspection requirement by integrating conveyors, cobots, and robots for material handling and sample manipulation. When equipped with autonomous decision making, failed products can easily be segregated and even quarantined. Whether implemented to support or replace visual inspection by humans, the most innovative X-ray inspection system can be designed to support rapid and reliable quality control to achieve 100% inspection without slowing down your production line.
In the case of quality assurance and the challenges of attention span, solutions are emerging that allow for better support of our teams through automation and autonomous decision making, allowing their talents to be redirected to other, more valuable efforts. Such advancements can result not only in improved quality and efficiency but also greater job satisfaction for our manufacturing teams, allowing us to make better things as well as better workplaces.
Dr. Bill Cardoso is CEO of Creative Electron.
More Columns from X-Rayted Files
X-Rayted Files: Best Practices in Buying MachinesX-Rayted Files: ’23 and Me?
X-Rayted Files: Battery-Powered Advancements Keep on Ticking
X-Rayted Files: What’s Cooler Than X-ray?
X-Rayted Files: My Favorite BGA Assembly Ever, Part 3
X-Rayted Files: My Favorite BGA Assembly Ever, Part 2
X-Rayted Files: My Favorite BGA Assembly Ever
X-Rayted Files: Smart vs. Intelligent SMT Factory