-
- News
- Books
Featured Books
- design007 Magazine
Latest Issues
Current IssueAll About That Route
Most designers favor manual routing, but today's interactive autorouters may be changing designers' minds by allowing users more direct control. In this issue, our expert contributors discuss a variety of manual and autorouting strategies.
Creating the Ideal Data Package
Why is it so difficult to create the ideal data package? Many of these simple errors can be alleviated by paying attention to detail—and knowing what issues to look out for. So, this month, our experts weigh in on the best practices for creating the ideal design data package for your design.
Designing Through the Noise
Our experts discuss the constantly evolving world of RF design, including the many tradeoffs, material considerations, and design tips and techniques that designers and design engineers need to know to succeed in this high-frequency realm.
- Articles
- Columns
- Links
- Media kit
||| MENU - design007 Magazine
Cadence’s Celsius: Don’t End up Holding the Hot Potato!
December 17, 2020 | Clive "Max" Maxfield, Maxfield High-Tech ConsultingEstimated reading time: 13 minutes
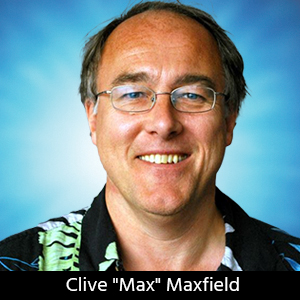
I was just thinking about the party game Hot Potato, which involves players gathering in a circle and quickly tossing a small object such as a beanbag or even a real potato to each other while music is being played. The player who is holding the “hot potato” when the music stops is eliminated, after which the music resumes and the game recommences with the remaining players until only the winner remains standing.
As an aside, although the origins of the hot potato game are not clear, there is reference to a similar game in Sidney Oldall Addy's Glossary of Sheffield Words from 1888. This is particularly poignant for me because I was “born and bred in Sheffield,” as they say. Amazingly enough, this book is still in print 132 years after it was first published. We can only wonder what Sidney would have thought about that, and I can only hope that my own books survive the test of time in such a robust manner.
The reason for my reminiscing on this game is that it reminds me of the thermal issues involved in designing an electronic product—anything from an integrated circuit (IC) to a PCB to a full-up system. In today’s increasingly competitive marketplace, accurate thermal analysis must be performed, and any potential issues have to be identified and addressed as early as possible in the design cycle, otherwise the system will run into problems, market windows will be missed, and someone will be left holding the hot potato. Trust me, you do not want to be that someone.
Figure 1: The complex interactions of electrical-thermal co-simulation require that components in the system be accurately modeled and analyzed in more detail than ever before.
Happily, you don’t have to be the poor soul to whom everyone else is casting aspersions (not me, you understand, because my throwing arm isn’t what it used to be). The reason for my joy is that I was recently introduced to the Celsius Thermal Solver from Cadence, and this bodacious beauty can solve all of our hot potato problems (which isn’t something I expected to hear myself saying when I woke up this morning).
As another aside, most people think Anders Celsius and Daniel Gabriel Fahrenheit invented the temperature scales bearing the names we know and love today. Most people would be wrong! For example, as I discussed in my What the FAQ are Celsius and Fahrenheit? column [1] , Anders initially started off with 0°C representing the boiling point of water, while 100°C represented the freezing point of water. It wasn’t until a year after his death that other users decided to swap them over. If you are interested in this sort of thing, you might also wish to peruse and ponder my What the FAQ are Kelvin, Rankine et al? column [2], which, amongst other things, provides a technique of telling the temperature by timing the chirps of common field crickets. But we digress...
If you know me at all, you will be aware that I can’t see one of today’s state-of-the-art tools like the Celsius Thermal Solver without taking a trip down memory lane to cogitate and ruminate over.
The Way Things Were
In my previous column, Cadence’s Clarity: ‘I Can See Clearly Now…’, I discussed my first position after leaving university, which was at International Computers Limited (ICL) as a member of a team designing central processing units (CPUs) for mainframe computers.
I now appreciate that I was extremely lucky because ICL embraced the concept of a mentorship program. The idea was that each new engineer was assigned to work with an older, more experienced (mentor) engineer. My mentor was my team leader, Dave Potts. At that time, I thought Dave was much older than me. He was definitely much wiser, but, looking back, he was probably only in his mid-20s.
Dave was a wonderful instructor. The reason I’m where I am today (an internationally renowned technology superstar to hear my dear old mother tell the tale) is largely due to the way in which he guided me in my early design efforts. For example, my first task was to design an application-specific integrated circuit (ASIC) to implement a barrel shifter-rotator function that was capable of shifting-rotating 128-bit words by anything from 1 to 128 bits in a single clock cycle.
These ASICs, which were implemented at the 5-micron process node (that’s three orders of magnitude larger than today’s latest and greatest process node), were incredibly limited by today’s standards. For example, each contained only 200 equivalent logic gates. This means that we needed to use a bunch of my ASICs to implement the shifter-rotator. Meanwhile, other members of the team were busily beavering away designing their own ASICs to implement their portions of the system.
If Dave had presented me with the entire shifter-rotator specification in one go, my brains would have leaked out of my ears and I would have had a nervous breakdown. Instead, he broke things down into a series of simpler tasks and built things up layer-by-layer, thereby guiding me to success and instilling a possibly mistaken sense of confidence and self-worth in me.
This was back in the mists of time we used to call 1980. The team of which I was a part was working on a mainframe computer called the S4L. Dave was a veteran from the previous 2900-series of machines, which were themselves predated by the 1900-series. I wasn’t involved in the thermal side of things, but some of the older engineers told me that the 1900-series had employed a chilled-water forced-air cooling system. They also told me about an unfortunate incident in the early days of the program when the cooling system had passed the dewpoint threshold causing moisture to precipitate out of the air. They described what ensued as being “like a tropical rainstorm inside the CPU cabinet,” which resulted in the contents of the cabinet ending up as a pile of rust.
I must admit that many of the nitty-gritty details from those days of yore have faded from my memory. However, such are the wonders of modern technology that, even though I haven’t seen Dave for 30 years, I tracked him down via LinkedIn and we enjoyed a transatlantic video call a couple of hours ago as I pen these words.
After reminiscing a little about the old days, I started to ask questions about some of the things I’d forgotten, like the sizes of the circuit boards and power supplies and suchlike. Dave told me that the power supply unit (PSU) for the 2980 computer he’d worked on, the predecessor to the S4L, had involved a motor generator that generated three phases at 415 volts, and that was located some distance away in a back room because of the noise it created. The three phases from the generator were chopped up by thyristors and smoothed by trays of capacitors (the PSU cabinet holding the thyristors and capacitors was 6 x 6 x 2 feet in size). The resulting supply was 5.2 volts at 1,800 amps. I just had to read those numbers again to make sure I wasn’t dreaming. Amazingly enough, there was also a rheostat on the side of the PSU cabinet that could be used to adjust the voltage by +/- 10%.
I’m not sure as to the PSU for the S4L because Dave and I both left ICL before the project was completed, but Dave says that it would have probably ended up looking similar to that for the 2980. In the case of the S4L, the ASICs we were designing were about 1-inch square, and each one dissipated between five and ten watts. The circuit boards were humongous by today’s standards. We’re talking about 2 x 3 feet in size and about 1/4” thick, with multiple power and ground planes and numerous signal layers. It’s scary to think that these boards were plugged into even bigger backplane boards.
The S4L was also designed to use forced-air cooling. Our ASICs were implemented using emitter-coupled logic (ECL). Dave says we didn’t have “hot spots” per se because everything ran hot. Each ASIC had its own heatsink with spines to dissipate the heat. The only way to probe one of the circuit boards when the computer was in operation would have been to use an extender card, which would have resulted in the board in question being out of the cooling airflow. The team leaders feared that the chips on the board on the extender would run so hot as to melt the solder and drop off the board. Although this would have removed them from the thermal equation and mitigated the thermal problem, it goes without saying that the performance of the computer and the quality of its calculations would have suffered.
As Rachel Caine, the American writer of science fiction, fantasy, mystery, suspense, and horror novels, said in one of her books, “God, it was hot! Forget about frying an egg on the sidewalk; this kind of heat would fry an egg inside the chicken.” I dare not think what she would have said about the S4L. Thankfully, as I mentioned earlier, Dave and I had left the project before it reached this stage.
Page 1 of 2
Suggested Items
Driving Innovation: Direct Imaging vs. Conventional Exposure
07/01/2025 | Simon Khesin -- Column: Driving InnovationMy first camera used Kodak film. I even experimented with developing photos in the bathroom, though I usually dropped the film off at a Kodak center and received the prints two weeks later, only to discover that some images were out of focus or poorly framed. Today, every smartphone contains a high-quality camera capable of producing stunning images instantly.
Hands-On Demos Now Available for Apollo Seiko’s EF and AF Selective Soldering Lines
06/30/2025 | Apollo SeikoApollo Seiko, a leading innovator in soldering technology, is excited to spotlight its expanded lineup of EF and AF Series Selective Soldering Systems, now available for live demonstrations in its newly dedicated demo room.
Indium Corporation Expert to Present on Automotive and Industrial Solder Bonding Solutions at Global Electronics Association Workshop
06/26/2025 | IndiumIndium Corporation Principal Engineer, Advanced Materials, Andy Mackie, Ph.D., MSc, will deliver a technical presentation on innovative solder bonding solutions for automotive and industrial applications at the Global Electronics A
Fresh PCB Concepts: Assembly Challenges with Micro Components and Standard Solder Mask Practices
06/26/2025 | Team NCAB -- Column: Fresh PCB ConceptsMicro components have redefined what is possible in PCB design. With package sizes like 01005 and 0201 becoming more common in high-density layouts, designers are now expected to pack more performance into smaller spaces than ever before. While these advancements support miniaturization and functionality, they introduce new assembly challenges, particularly with traditional solder mask and legend application processes.
Knocking Down the Bone Pile: Tin Whisker Mitigation in Aerospace Applications, Part 3
06/25/2025 | Nash Bell -- Column: Knocking Down the Bone PileTin whiskers are slender, hair-like metallic growths that can develop on the surface of tin-plated electronic components. Typically measuring a few micrometers in diameter and growing several millimeters in length, they form through an electrochemical process influenced by environmental factors such as temperature variations, mechanical or compressive stress, and the aging of solder alloys.