-
- News
- Books
Featured Books
- pcb007 Magazine
Latest Issues
Current IssueInventing the Future with SEL
Two years after launching its state-of-the-art PCB facility, SEL shares lessons in vision, execution, and innovation, plus insights from industry icons and technology leaders shaping the future of PCB fabrication.
Sales: From Pitch to PO
From the first cold call to finally receiving that first purchase order, the July PCB007 Magazine breaks down some critical parts of the sales stack. To up your sales game, read on!
The Hole Truth: Via Integrity in an HDI World
From the drilled hole to registration across multiple sequential lamination cycles, to the quality of your copper plating, via reliability in an HDI world is becoming an ever-greater challenge. This month we look at “The Hole Truth,” from creating the “perfect” via to how you can assure via quality and reliability, the first time, every time.
- Articles
- Columns
- Links
- Media kit
||| MENU - pcb007 Magazine
LPKF Celebrates 20 Year Anniversary of Laser Plastic Welding Division
December 23, 2020 | LPKFEstimated reading time: 2 minutes
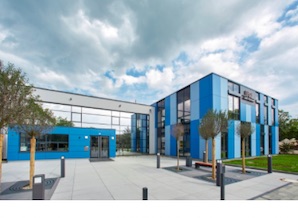
The engineers of the then LaserQuipment AG, a spin-off of Bayerisches Laserzentrum in Nuremberg-Erlangen, laid the groundwork for laser plastic welding. At that time – just like now at LPKF – they developed and produced laser systems for joining injection-molded parts. Production services for laser plastic welding have also been a field of activity since then. Initially received with hesitation in the market, laser-welded plastics are widely used today in medical technology, consumer electronics – and in every recently built car. No one wants to do without compact and lightweight, yet stable, control devices such as parking sensors anymore.
The Technology
In laser transmission welding, two components are welded together. They differ slightly in their material properties: one of the parts is transparent to the laser wavelength used and the other absorbs the laser energy. The heat that arises locally in the absorbing part during the process is transferred through a slight mechanical pressure applied to the second part, which results in both parts melting at the weld seam – and a reliable joint with the same strength as the parent material. Many different plastics with various geometries can be welded in this way.
In the early days of the company, relatively small welding heads for line integration in the automotive industry were the focus of developments. They were supplemented by complete systems for standalone operation. Various welding methods became dominant for different application fields. For example, cylindrical bodies are joined with radial welding systems, whereas large 3D parts are welded using a special, patented LPKF method. “Hybrid welding” is LPKF’s name for a method using multiaxis robots to enable fast and flexible processes. In addition, with LPKF systems, even transparent plastics can be laser-welded.
Outlook
With the systems, which have been developed and optimized over the years as expertise has been gained, the most diverse of components – large or small, with wide or narrow weld seams, exhibiting simple or complex geometries – can be joined without any problems. Today, extensive automation of the laser machines is just as natural as easy-to-use hardware and software that ensure the traceability of individual production steps are. As a result, the welded products even meet the exacting requirements in the automotive and medical technology industries.
Simon Reiser, on board as Managing Director since 2019, is proud of his employees’ achievements. “There are now over 1,200 LPKF systems for laser plastic welding in use on all continents of the world; more than 3,000 different processes are carried out with these systems. In the automotive industry, nearly every OEM supplier is using LPKF systems.”
He also sees many opportunities for the future. “The still-growing plastics market is changing and is still searching for solutions, for example, for the further treatment of recycled plastics or new materials. LPKF is working on innovative solutions for this, too, so that the advantages of laser technology – cleanliness and joining without chemicals or chip formation – over other joining technologies can continue to be used in as many application areas as possible.”
Testimonial
"Our marketing partnership with I-Connect007 is already delivering. Just a day after our press release went live, we received a direct inquiry about our updated products!"
Rachael Temple - AlltematedSuggested Items
LPKF Strengthens LIDE Technology Leadership with New Patent Protection in Korea
09/04/2025 | LPKFLPKF Laser & Electronics SE today announced that its groundbreaking LIDE (Laser Induced Deep Etching) technology has received additional patent protection in Korea through the Korean Patent Office (KPCA), effective September 1, 2025.
UHDI Fundamentals: UHDI Technology and Industry 4.0
09/03/2025 | Anaya Vardya, American Standard CircuitsUltra high density interconnect (UHDI) technology is rapidly transforming how smart systems are designed and deployed in the context of Industry 4.0. With its capacity to support highly miniaturized, high-performance, and densely packed electronics, UHDI is a critical enabler of the smart, connected, and automated industrial future. Here, I’ll explore the synergy between UHDI and Industry 4.0 technologies, highlighting applications, benefits, and future directions.
CEE PCB Launches PCBpedia: A New Knowledge Hub for Circuit Board Technology
09/03/2025 | CEE PCBCEE PCB, a leading manufacturer of PCBs and FPCs, is responding to the growing demand for reliable technical knowledge. With PCBpedia, CEE introduces a new knowledge platform featuring expert articles on key topics in circuit board technology – from FPC design rules to surface finishes.
Coming Soon: The Advanced Electronics Packaging Digest
08/27/2025 | Marcy LaRont, I-Connect007The upcoming Advanced Electronics Packaging Digest is a curated, condensed monthly publication designed to keep you informed and engaged with the fast-moving world of advanced electronics packaging (AEP). In our inaugural September issue, we will begin at the foundation with an in-depth interview featuring Matt Kelly, CTO of the Global Electronics Association. Kelly and his Technology Solutions Team approach advanced packaging from a holistic systems perspective.
Nordson Reports Q3 Fiscal 2025 Results and Updates Full Year Guidance
08/21/2025 | BUSINESS WIRENordson Corporation reported results for the fiscal third quarter ended July 31, 2025. Sales were $742 million compared to the prior year’s third quarter sales of $662 million.