-
- News
- Books
Featured Books
- design007 Magazine
Latest Issues
Current IssueAll About That Route
Most designers favor manual routing, but today's interactive autorouters may be changing designers' minds by allowing users more direct control. In this issue, our expert contributors discuss a variety of manual and autorouting strategies.
Creating the Ideal Data Package
Why is it so difficult to create the ideal data package? Many of these simple errors can be alleviated by paying attention to detail—and knowing what issues to look out for. So, this month, our experts weigh in on the best practices for creating the ideal design data package for your design.
Designing Through the Noise
Our experts discuss the constantly evolving world of RF design, including the many tradeoffs, material considerations, and design tips and techniques that designers and design engineers need to know to succeed in this high-frequency realm.
- Articles
- Columns
- Links
- Media kit
||| MENU - design007 Magazine
Lee Ritchey on Reducing Respins by One
December 30, 2020 | I-Connect007 Editorial TeamEstimated reading time: 3 minutes
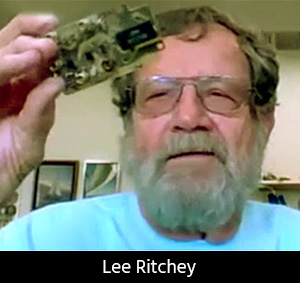
I-Connect007 recently spoke with Lee Ritchey about the subject of continuous improvement with a focus on DFM, specifically looking at the benefits of reducing the number of respins by just one. A longtime instructor and one of the authors of Right the First Time: A Practical Handbook on High-Speed PCB and System Design, Lee has spent decades preaching the value of solid DFM practices, so we asked him to discuss why so many OEMs accept multiple respins with each design project and what designers could do to eliminate just one spin. He also shares some of the lessons in reducing respins that he learned in the early days of Silicon Valley.
Andy Shaughnessy: We’ve been talking about making 2021 the year of continuous improvement, and we came up with an idea. What if we eliminated just one spin from every cycle and kept that as a goal? Of course, your book Right the First Time came to the top of our conversation. Many companies continue to build respins into the project budget, but what about the wasted hours?
Lee Ritchey: You picked a topic that I actually know something about. I have stories. Some of them are horror stories! But if you have one less respin than the competition, you’re at the market first. That has been historically the business model of Intel and IBM. Of course, Intel and AMD have roughly the same kind of processors, with one exception: AMD has never been first to market. Originally, that was because they had to spin the silicon a couple of times. The people at Intel realized the person who’s first to market gets to define the playing field, and they spent huge amounts of money on simulation tools.
One of my favorite stories is the first Pentium processor. It was the first time a processor had been shipped on the first artwork. They got a lot of press on that. During the press conference, somebody asked how they did it, and the project manager said, “We didn’t cut silicon until we got a DOS prompt on the emulator.” They spent the money on upfront design, and that’s sort of defined that field ever since.
There were two where I have really clear experience. One of them was with 3Com, where they would assume they were going to spin the design and rush to get a prototype. The usual reason was so that the engineers had something to work on, and almost never was that something right.
I did a brief piece on this, which wasn’t even a respin; it had to do with how much money we spent to accelerate getting the prototype of a PCB. In the case I was working on there, the difference between a three-day turn and a 10-day turn was only about $5,000, and they wouldn’t spend it.
One evening, we were doing the budget for the next quarter, and it came out to a little bit less than $2 million a week to run the project. I told management, “If I spend $5,000 and take a week out of this budget, doesn’t that make good sense for our return on investment?” Finally, someone had quantified the cost of time for them because no one had done that.
And that’s not even a respin; that’s just being smart about where you spend premiums. Now, that gives you a yardstick for how much a respin costs. If you’re lucky, and a respin only takes six weeks and $2 million, isn’t it worth spending another week getting it right? I think so.
To read this entire interview, which appeared in the December 2020 issue of Design007 Magazine, click here.
Suggested Items
DownStream Acquisition Fits Siemens’ ‘Left-Shift’ Model
06/26/2025 | Andy Shaughnessy, I-Connect007I recently spoke to DownStream Technologies founder Joe Clark about the company’s acquisition by Siemens. We were later joined by A.J. Incorvaia, Siemens’ senior VP of electronic board systems. Joe discussed how he, Rick Almeida, and Ken Tepper launched the company in the months after 9/11 and how the acquisition came about. A.J. provides some background on the acquisition and explains why the companies’ tools are complementary.
Elementary Mr. Watson: Retro Routers vs. Modern Boards—The Silent Struggle on Your Screen
06/26/2025 | John Watson -- Column: Elementary, Mr. WatsonThere's a story about a young woman preparing a holiday ham. Before putting it in the pan, she cuts off the ends. When asked why, she shrugs and says, "That's how my mom always did it." She asks her mother, who gives the same answer. Eventually, the question reaches Grandma, who laughs and says, "Oh, I only cut the ends off because my pan was too small." This story is a powerful analogy for how many PCB designers approach routing today.
Connect the Dots: The Future of PCB Design and Manufacturing
07/02/2025 | Matt Stevenson -- Column: Connect the DotsFor some time, I have been discussing the increasing complexity of PCBs and how designers can address the constantly evolving design requirements associated with them. My book, "The Printed Circuit Designer’s Guide to… Designing for Reality," details best practices for creating manufacturable boards in a modern production environment.
Siemens Turbocharges Semiconductor and PCB Design Portfolio with Generative and Agentic AI
06/24/2025 | SiemensAt the 2025 Design Automation Conference, Siemens Digital Industries Software today unveiled its AI-enhanced toolset for the EDA design flow.
Cadence AI Autorouter May Transform the Landscape
06/19/2025 | Andy Shaughnessy, Design007 MagazinePatrick Davis, product management director with Cadence Design Systems, discusses advancements in autorouting technology, including AI. He emphasizes a holistic approach that enhances placement and power distribution before routing. He points out that younger engineers seem more likely to embrace autorouting, while the veteran designers are still wary of giving up too much control. Will AI help autorouters finally gain industry-wide acceptance?