-
- News
- Books
Featured Books
- design007 Magazine
Latest Issues
Current IssueShowing Some Constraint
A strong design constraint strategy carefully balances a wide range of electrical and manufacturing trade-offs. This month, we explore the key requirements, common challenges, and best practices behind building an effective constraint strategy.
All About That Route
Most designers favor manual routing, but today's interactive autorouters may be changing designers' minds by allowing users more direct control. In this issue, our expert contributors discuss a variety of manual and autorouting strategies.
Creating the Ideal Data Package
Why is it so difficult to create the ideal data package? Many of these simple errors can be alleviated by paying attention to detail—and knowing what issues to look out for. So, this month, our experts weigh in on the best practices for creating the ideal design data package for your design.
- Articles
- Columns
- Links
- Media kit
||| MENU - design007 Magazine
Seven Tips for Your Next Stackup Design
February 1, 2021 | Eric Bogatin, University of Colorado, BoulderEstimated reading time: 4 minutes
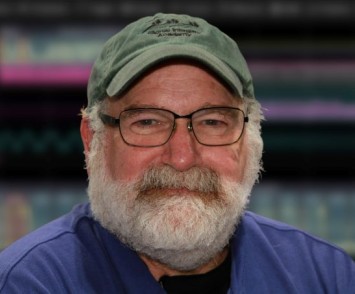
If interconnects were transparent, the stackup in your board would just be about how many layers you would need to route all the connections between components. In fact, some test boards that are strictly testing continuity and isolation do exactly this. Each layer is a dense packing of narrow signal traces connecting an array of pogo pin pads on the top side to an array of connectors to an ATE on the bottom side.
But rarely do we have the luxury of designing a board just for connectivity. When interconnects are not transparent, we must engineer them to reduce the noise they can generate. This is where design for signal integrity, power integrity and EMC—collectively high-speed digital engineering—are so important.
Seven Tips for Stackup
1. An important element in reducing the noise contributions from the interconnects comes from the stackup of the board and the layer assignments. The very first step is to engineer all signal layers with at least one adjacent plane as the return path. This will reduce the crosstalk between the signal-return paths: the microstrip traces on the outer layers and stripline traces on the inner layers.
2. The striplines can be either one signal layer between two planes or two signal layers between two planes. With two signal layers between two planes, there is the danger of excessive crosstalk if signals on adjacent layers are routed broadside to each other.
3. To avoid this problem, it is best to route the adjacent signal layers in dual stripline stackups orthogonally. One signal layer is routed in the x-direction, the other in the y-direction.
4. When interconnects must distribute 10 A of current or less, traces as wide as 200 mils can carry the 10 A of current in 1 oz copper with an acceptable temperature rise. But, with larger currents, like 20 A or more, it may be necessary to use wide planes to distribute the current from the power generators to the power consumers on a board. This is when some of the planes should be allocated as dedicated power planes.
The challenge is balancing the requirements of power distribution with the requirements for reduced crosstalk from signals changing return planes.
In principle, a signal line will see exactly the same characteristic impedance if the return plane is at ground potential or 12 V potential or anywhere in between. The problem with using a different voltage plane than ground to carry return current is when the signals change layers.
5. When a signal trace switches layers, we use a via to carry the signal current. If the return plane also changes, we will achieve the lowest crosstalk between all the signals switching layers when we also provide a via to carry the return current from the starting plane(s) to the final plane(s). This is a lowimpedance via shorting between the two different return planes. This is only possible if the return planes are the same voltage. If they are at different voltages, we can’t add a shorting via between them. This is a strong motivation to only use ground planes as the return planes for signals.
6. At best, if the two planes are a different voltage, we can add shorting vias between the two planes with a DC blocking capacitor between them. The loop inductance through a DC blocking capacitor can be as much as 5x higher impedance of a direct shorting via. It is a poor approximation to a shorting via, but the best we can do.
7. When signals change return planes and the planes are at different voltages, we run the risk of launching high bandwidth return currents into the cavity formed by the two planes. This is a source of long-range crosstalk and potentially a source of radiated emissions noise. One solution to reduce the noise in the power-ground cavity is by using very thin dielectric in these layers. This suggests that when power planes are used, they should be paired with closely spaced adjacent ground planes.
Once the order of the signal layers and planes is set, the dimensions can be calculated based on the line width of signal traces, the dielectric constant of the laminates used, and the target single-ended or differential impedance. This is where a 2D field solver comes in handy to define the cross section of microstrip traces, single layer stripline and dual layer strip line traces.
If you don’t follow these tips, it does not mean your board will not work. Unfortunately, there is no way of knowing if your stackup design will work or not unless you do a detailed analysis based on the driver models and 3D electromagnetic analysis of all the worst-case signal and power paths. Implementing these tips is about risk reduction.
They are part of a balanced diet of best stackup design practices, best signal routing design practices, and best power distribution design practices. And like all design guidelines, buyer beware. Always consider the best design practices, but also always do your own analysis.
This article appeared in the January 2021 issue of Design007 Magazine.
Suggested Items
Copper Price Surge Raises Alarms for Electronics
07/15/2025 | Global Electronics Association Advocacy and Government Relations TeamThe copper market is experiencing major turbulence in the wake of U.S. President Donald Trump’s announcement of a 50% tariff on imported copper effective Aug. 1. Recent news reports, including from the New York Times, sent U.S. copper futures soaring to record highs, climbing nearly 13% in a single day as manufacturers braced for supply shocks and surging costs.
I-Connect007 Editor’s Choice: Five Must-Reads for the Week
07/11/2025 | Andy Shaughnessy, Design007 MagazineThis week, we have quite a variety of news items and articles for you. News continues to stream out of Washington, D.C., with tariffs rearing their controversial head again. Because these tariffs are targeted at overseas copper manufacturers, this news has a direct effect on our industry.I-Connect007 Editor’s Choice: Five Must-Reads for the Week
Digital Twin Concept in Copper Electroplating Process Performance
07/11/2025 | Aga Franczak, Robrecht Belis, Elsyca N.V.PCB manufacturing involves transforming a design into a physical board while meeting specific requirements. Understanding these design specifications is crucial, as they directly impact the PCB's fabrication process, performance, and yield rate. One key design specification is copper thieving—the addition of “dummy” pads across the surface that are plated along with the features designed on the outer layers. The purpose of the process is to provide a uniform distribution of copper across the outer layers to make the plating current density and plating in the holes more uniform.
Trump Copper Tariffs Spark Concern
07/10/2025 | I-Connect007 Editorial TeamPresident Donald Trump stated on July 8 that he plans to impose a 50% tariff on copper imports, sparking concern in a global industry whose output is critical to electric vehicles, military hardware, semiconductors, and a wide range of consumer goods. According to Yahoo Finance, copper futures climbed over 2% following tariff confirmation.
Happy’s Tech Talk #40: Factors in PTH Reliability—Hole Voids
07/09/2025 | Happy Holden -- Column: Happy’s Tech TalkWhen we consider via reliability, the major contributing factors are typically processing deviations. These can be subtle and not always visible. One particularly insightful column was by Mike Carano, “Causes of Plating Voids, Pre-electroless Copper,” where he outlined some of the possible causes of hole defects for both plated through-hole (PTH) and blind vias.