-
- News
- Books
Featured Books
- design007 Magazine
Latest Issues
Current IssueProper Floor Planning
Floor planning decisions can make or break performance, manufacturability, and timelines. This month’s contributors weigh in with their best practices for proper floor planning and specific strategies to get it right.
Showing Some Constraint
A strong design constraint strategy carefully balances a wide range of electrical and manufacturing trade-offs. This month, we explore the key requirements, common challenges, and best practices behind building an effective constraint strategy.
All About That Route
Most designers favor manual routing, but today's interactive autorouters may be changing designers' minds by allowing users more direct control. In this issue, our expert contributors discuss a variety of manual and autorouting strategies.
- Articles
- Columns
- Links
- Media kit
||| MENU - design007 Magazine
Estimated reading time: 5 minutes
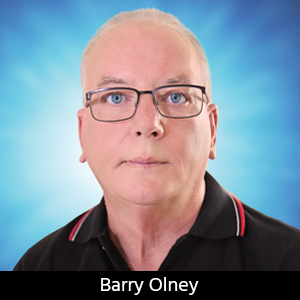
Beyond Design: Stackup Configurations to Mitigate Crosstalk
Crosstalk arises because of the unintentional coupling of electromagnetic fields. The current trend is toward smaller, faster boards with lower IC core voltages. But, as the supply voltage drops from 3.3V to 1.5V, the allowable noise margin is more than half. Also, the closer parallel trace segments are spaced, due to limited real estate, the greater the chance of coupling. The reflections created by crosstalk erode the noise margin. We cannot eliminate crosstalk, but as PCB designers it is our job to ascertain how to control and manage the predicted interference.
Crosstalk is three dimensional and dependent on the signal trace separation, the trace to plane(s) separation, parallel segment length, the transmission line load, and the technology employed. But crosstalk also varies depending on the physical stackup configuration. In this month’s column, I will delve into the properties of microstrip and stripline crosstalk and how to mitigate the concern.
Crosstalk can be induced by the following stackup configurations as illustrated in Figure 1:
- Microstrip edge coupled
- Stripline edge coupled
- Dual stripline broadside coupled
- Dual stripline broadside-edge coupled
Figure 1: Crosstalk stackup configurations.
The first two edge coupled configurations are well known—and for good reason—they are also commonly used for differential pairs. Close coupling is good for maintaining impedance, rejecting noise and avoiding slew, but not good for crosstalk. The other two configurations are broadside coupling, which has many disadvantages: the main one being layer-to-layer registration during fabrication. IPC Class 3 specifies ±2 mil registration between any two adjacent layers but it may be more like ±4 mil for a combination of layers nudging the impedance way out. Also, broadside coupling requires a very thick dielectric material between adjacent signal layers which will generally render the substrate too thick. On the plus side, it can be a good solution for navigating a connector pin array, maintaining impedance with no reference place. Broadside-edge coupling requires less dielectric thickness but is very difficult to predict the impedance due to alignment issues. Impedance aside, any coupling of unrelated signals should be avoided.
There are two types of crosstalk: forward and reverse. These are also termed far-end (FEXT) and near-end (NEXT) crosstalk, which refers to where the crosstalk is measured—at the load or the receiver, respectively.
Interestingly, there is a unique property of the stripline configuration in that the ratio of mutual capacitance (Cm) equals that of the mutual inductance (Lm) which cancels out the forward crosstalk (Kf) component (equation 1). Whereas reverse crosstalk (Kb in equation 2) is the addition of the two, consequently it is always present to some degree.
Figure 2 shows the near- and far-end crosstalk for a microstrip configuration where the victim traces are adjacent to the aggressor trace (1.5V @ 1GHz). In this case, the traces are 4 mils wide, 40 ohms impedance with a 4-mil spacing. Crosstalk falls off rapidly with the square of the distance and the degree of impact is related to the aggressor signal voltage, the proximity of trace segments, and proximity to the plane(s).
In an outer layer microstrip configuration, the mutual capacitive coupling between adjacent traces is generally weaker than the mutually inductive coupling, driving the FEXT co-efficient negative, as can be seen in the simulation. However, forward crosstalk does not exist in the stripline configuration. The fine balance between inductive and capacitive coupled crosstalk produces almost no observable forward crosstalk (Figure 3). This shows the near-end crosstalk of a stripline configuration for 4 mil wide, 40 ohms impedance traces with a 4-mil spacing. Notice how there is no FEXT component of the noise. Also, the peak amplitude of the crosstalk has been considerably reduced. All other factors being equal, here is just another good reason why one should always route high-speed signals on the inner layers of a multilayer PCB. Stripline edge coupled signals can also be placed closer to each other compared to the microstrip equivalent leaving more space for routing, which is always welcomed.
The easiest way to reduce crosstalk from a nearby aggressor signal is, of course, by increasing the spacing between the signals in question. Crosstalk falls off very rapidly with distance. Crosstalk plummets roughly quadratically with increased separation. By doubling the spacing, it cuts the crosstalk to roughly a quarter of its original level. A good rule of thumb for this is Gap = 3X trace width. However, in today’s complex designs it is not always possible to use up valuable real estate to satisfy the above. Also, different technologies should not be mixed as higher voltages create higher crosstalk. And long parallel trace segments should be avoided.
Figure 4: Crosstalk vs. trace spacing (edge coupled).
Figure 4 shows the effect of the edge coupling on the crosstalk for both microstrip (outer layers) and stripline (inner layers). Note that the stripline has about one-quarter the crosstalk of the microstrip. Also, microstrip crosstalk tends to radiate from the outer layers of a multilayer PCB whereas stripline confines the EM fields between the planes.
Crosstalk also depends on the load which may vary considerably when driving banks of memory modules, for example. Keep in mind that the total crosstalk on each victim trace is the total crosstalk from each of several nearby aggressors, all of which sum up to produce the maximum value.
Both forward and reverse crosstalk can be arbitrarily reduced by separating the aggressor(s) from the victim trace(s) or by reducing the height of the dielectric above/below the planes. The latter also requires a reduction in trace width to maintain the impedance. If real estate is a premium, as it generally is on dense, high-speed designs, then routing on the inner layers and avoiding broadside coupling may be good solutions.
Key Points:
- Crosstalk is three dimensional and is dependent on the signal trace separation, the trace to plane(s) separation, parallel segment length, the transmission line load, and the technology employed
- Crosstalk also varies depending on the physical stackup configuration
- Close coupling is good for maintaining impedance, rejecting noise and avoiding slew, but not good for crosstalk
- Far-end (FEXT) and near-end (NEXT) crosstalk refer to where the crosstalk is measured—at the load or the receiver, respectively
- A unique property of the stripline configuration is that the ratio of mutual capacitance equals that of the mutual inductance, which cancels out the forward crosstalk component
- The peak amplitude of the stripline crosstalk is considerably less than microstrip
- Stripline edge coupled signals can also be placed closer to each other compared to the microstrip equivalent leaving more space for routing
- The easiest way to reduce crosstalk from a nearby aggressor signal is by increasing the spacing between the signals in question; crosstalk falls off very rapidly with distance
- Different technologies should not be mixed as higher voltages create higher crosstalk
- Long parallel trace segments and broadside coupling should be avoided
- The stripline configuration has about one-quarter of the crosstalk of the microstrip for the same spacing
Resources
- Beyond Design: Controlling the Beast, Crosstalk Margins, by Barry Olney.
- Trace Design for Crosstalk Reduction, by Scott McMorrow, Samtec.
This column originally appeared in the February 2021 issue of Design007 Magazine.
More Columns from Beyond Design
Beyond Design: Effective Floor Planning StrategiesBeyond Design: Refining Design Constraints
Beyond Design: The Metamorphosis of the PCB Router
Beyond Design: Radiation and Interference Coupling
Beyond Design: Key SI Considerations for High-speed PCB Design
Beyond Design: Electro-optical Circuit Boards
Beyond Design: AI-driven Inverse Stackup Optimization
Beyond Design: High-speed Rules of Thumb