-
- News
- Books
Featured Books
- design007 Magazine
Latest Issues
Current IssueAll About That Route
Most designers favor manual routing, but today's interactive autorouters may be changing designers' minds by allowing users more direct control. In this issue, our expert contributors discuss a variety of manual and autorouting strategies.
Creating the Ideal Data Package
Why is it so difficult to create the ideal data package? Many of these simple errors can be alleviated by paying attention to detail—and knowing what issues to look out for. So, this month, our experts weigh in on the best practices for creating the ideal design data package for your design.
Designing Through the Noise
Our experts discuss the constantly evolving world of RF design, including the many tradeoffs, material considerations, and design tips and techniques that designers and design engineers need to know to succeed in this high-frequency realm.
- Articles
- Columns
- Links
- Media kit
||| MENU - design007 Magazine
The Key to Eliminating Bad Design Data: Constant Vigilance
March 9, 2021 | I-Connect007 Editorial TeamEstimated reading time: 2 minutes
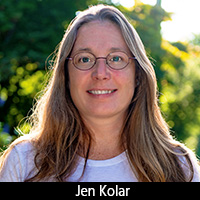
The I-Connect007 editorial team recently met with Jen Kolar and Mark Thompson of Monsoon Solutions to discuss ways to eliminate bad data from the design process, whether that be from CAD libraries, parts vendors, chip makers, or customers themselves. They key in on some problems and obstacles that allow incorrect data into the design cycle, and then highlight possible solutions.
Barry Matties: There are just so many places where you can introduce bad data into the design cycle. And as you both know, one of the biggest challenges is to get the data that you really need to be accurate right from the start. And, if it’s wrong at the beginning, it’s wrong all the way through.
Jen Kolar: It’s like any additive process, where the errors are added along the way. You have garbage in, garbage out in each step along the way. Maybe you have a thoughtful front-end designer who does a thoughtful design and gives really good input, but you have a PCB designer who’s sloppy and leaves half the detail out of the fab notes. Maybe it was good data into them, but they didn’t translate all that to the fab shop. Or maybe they had good data from one point, but you have those additive errors. Maybe there was a partial error at the beginning, but it just builds and builds, and gets worse and worse.
Matties: The thing is, if it’s good at one point, you have so many different points where it can go off the rails. It could be a combination of good data here, bad data there.
Kolar: I couldn’t agree more, and I think part of it is dependent on who’s driving the schedule in a project; a lot of times, the people driving the schedule just care that it’s started. You have management saying “Start,” so whoever is designing the project is saying, “Okay. I’m still figuring out my electrical design, but I’ve been told to put it in schematic.” You can end up with a project that takes a lot longer, costs more, and works poorer than if you’d just waited and started two months later.
Matties: And you’ll probably be doing multiple re-spins on it as well.
Kolar: Exactly. There are a lot of different sources of poor data: There’s just lack of knowledge, schedule pressure, sloppiness, and there is misinformation. There have been a number of times that we have engineers send us reference designs and say, “Just do what the reference design says.” Then we get to argue that the reference designs have nothing to do with manufacturability, and you repeat that cycle over and over. From our perspective, when you’re getting input data, ideally, you’re getting enough variants of it that you have something to validate against. Maybe I get a board file that has some of the parts loaded. Then, maybe I also have a STEP file or mechanical data that I can sanity-check against that, or the schematic, which is also going to have some callouts.
To read this entire interview, which appeared in the March 2021 issue of Design007 Magazine, click here.
Suggested Items
DownStream Acquisition Fits Siemens’ ‘Left-Shift’ Model
06/26/2025 | Andy Shaughnessy, I-Connect007I recently spoke to DownStream Technologies founder Joe Clark about the company’s acquisition by Siemens. We were later joined by A.J. Incorvaia, Siemens’ senior VP of electronic board systems. Joe discussed how he, Rick Almeida, and Ken Tepper launched the company in the months after 9/11 and how the acquisition came about. A.J. provides some background on the acquisition and explains why the companies’ tools are complementary.
Elementary Mr. Watson: Retro Routers vs. Modern Boards—The Silent Struggle on Your Screen
06/26/2025 | John Watson -- Column: Elementary, Mr. WatsonThere's a story about a young woman preparing a holiday ham. Before putting it in the pan, she cuts off the ends. When asked why, she shrugs and says, "That's how my mom always did it." She asks her mother, who gives the same answer. Eventually, the question reaches Grandma, who laughs and says, "Oh, I only cut the ends off because my pan was too small." This story is a powerful analogy for how many PCB designers approach routing today.
Connect the Dots: The Future of PCB Design and Manufacturing
07/02/2025 | Matt Stevenson -- Column: Connect the DotsFor some time, I have been discussing the increasing complexity of PCBs and how designers can address the constantly evolving design requirements associated with them. My book, "The Printed Circuit Designer’s Guide to… Designing for Reality," details best practices for creating manufacturable boards in a modern production environment.
Siemens Turbocharges Semiconductor and PCB Design Portfolio with Generative and Agentic AI
06/24/2025 | SiemensAt the 2025 Design Automation Conference, Siemens Digital Industries Software today unveiled its AI-enhanced toolset for the EDA design flow.
Cadence AI Autorouter May Transform the Landscape
06/19/2025 | Andy Shaughnessy, Design007 MagazinePatrick Davis, product management director with Cadence Design Systems, discusses advancements in autorouting technology, including AI. He emphasizes a holistic approach that enhances placement and power distribution before routing. He points out that younger engineers seem more likely to embrace autorouting, while the veteran designers are still wary of giving up too much control. Will AI help autorouters finally gain industry-wide acceptance?