-
- News
- Books
Featured Books
- pcb007 Magazine
Latest Issues
Current IssueInventing the Future with SEL
Two years after launching its state-of-the-art PCB facility, SEL shares lessons in vision, execution, and innovation, plus insights from industry icons and technology leaders shaping the future of PCB fabrication.
Sales: From Pitch to PO
From the first cold call to finally receiving that first purchase order, the July PCB007 Magazine breaks down some critical parts of the sales stack. To up your sales game, read on!
The Hole Truth: Via Integrity in an HDI World
From the drilled hole to registration across multiple sequential lamination cycles, to the quality of your copper plating, via reliability in an HDI world is becoming an ever-greater challenge. This month we look at “The Hole Truth,” from creating the “perfect” via to how you can assure via quality and reliability, the first time, every time.
- Articles
- Columns
- Links
- Media kit
||| MENU - pcb007 Magazine
Estimated reading time: 4 minutes
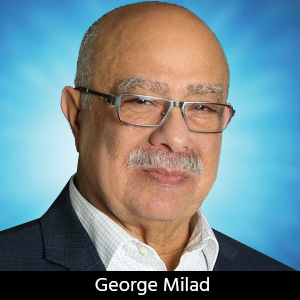
The Plating Forum: RAIG (Reduction Assisted Immersion Gold) for Gold Surface Finishes
RAIG was introduced a few years ago to meet the requirements of newer designs. Since its inception, more designers are finding RAIG gold to be a viable alternative to standard immersion gold. RAIG gold is a mixed-reaction bath that functions as immersion gold; with a reducing agent, it also functions as an electroless (autocatalytic) bath.
The reactions start simultaneously with the introduction of the substrate (nickel, palladium, or copper). Because the immersion reaction is a displacement reaction, it diminishes over time as the substrate becomes less available for deposition. The electroless reaction continues, relying on the reducing agent present in the electrolyte, rather than on substrate availability. RAIG gold is limited in how much gold it can deposit, as compared to a pure electroless gold. It is ideally suited for deposits of 3–6 µin.
Curbing the immersion reaction and allowing gold thickness to build autocatalytically expands the operating window by allowing thicker gold to deposit without nickel corrosion. A thicker gold layer (3–6 µin), is beyond the capability of standard immersion gold electrolytes, but is desirable for many applications, as it widens the operating window for gold wire bonding.
Figure 1: The effect of gold thickness on the operating window of the bonding force.
Figure 1 shows the relationship between gold thickness and the strength of the wire bond. Two thicknesses of gold, 0.05 mm (2.0 µin) and 0.2 mm (8.0 µin) were bonded using a 0.25 mm gold wire at three different bonding forces (25, 50 and 75g force). Ultrasonic power (mW) and time (sec) were held constant. The wires were then pulled and the break point in the wire was recorded. Bond lifts (E) and brakes at the heel of the bond (D) indicated weak or non-reliable bonds. Break points (B and C) were indicative of a reliable bond.
The data shows that both thicknesses could produce robust joints. However, the thinner (0.05 mm) gold required a higher gram force to form a reliable bond. The thicker gold (0.2 mm) produced reliable bonds at lower gram force, opening the operating window for the bonding parameter.
For gold wire bonding applications, designers prefer to specify a gold thickness of 3–5 µin, which is beyond the capability of immersion gold. Increasing dwell time in an immersion gold bath is the most common cause of nickel corrosion.
RAIG Applications
RAIG gold is an immersion gold replacement for ENIG, ENEPIG and EPIG. It meets the design requirement for thicker gold with no nickel corrosion, in a single plating step.
ENIG
ENIG is a common gold surface finish that is solderable and aluminum wire bondable. It is also used as a contacting surface. ENIG is non-electrolytic and does not require bussing or connectivity during plating. It is ideal for SMT pads. The choice of chemicals and the conditions of plating are important to avoid corrosion of the nickel. Nickel corrosion, also referred to as “black pad,” occurs in the gold bath. Immersion gold deposition is, in essence, a corrosion or displacement reaction. If conditions are not controlled, nickel may go into solution at the expense of hydrogen ions without gold deposition, creating nickel corrosion.
Under controlled plating conditions, nickel corrosion does not occur. It can occur, however, if the nickel deposit is uneven, the gold bath pH is too low, the gold concentration is below spec or the dwell time in the bath is too long. Such conditions are usually avoidable, except when the design requires thicker immersion gold (in excess of 2.5 µin).
Some manufacturers attempt to achieve this thickness by extending the dwell time in the gold bath, however, immersion gold baths are not designed to deposit more than 2.5 µin. If higher gold (3–5 µin immersion gold (RAIG).
Electroless gold is not common at PWB manufacturing sites. Electroless gold requires an immersion gold strike prior to electroless deposition. Adding another gold bath is a costly proposition. RAIG gold is a single bath that can deposit 3–5 microinches of gold without corrosion.
ENEPIG
This finish is gaining a lot of traction. ENEPIG forms the most reliable solder joint with lead-free solder and is also a gold-wire-bondable surface. In a previous column, I discussed the possibility of nickel corrosion beneath the palladium layer under certain condition, one being extended dwell time in an immersion gold bath to achieve higher gold thickness. The use of RAIG gold allows for a thicker deposit without nickel corrosion.
EPIG vs. EPAG
EPIG (electroless palladium/immersion gold) and EPAG (electroless palladium autocatalytic (electroless) gold) are nickel-free surface finishes that prevent the signal loss associated with electroless nickel deposits. They are widely valued for high frequency RF applications.
As discussed, thicker gold (greater than immersion gold) increases the wire bond operating window. EPAG is promoted as the answer to the thickness limitations of immersion gold. Autocatalytic gold requires an immersion gold underlay and is a difficult bath to control. RAIG gold deposits a higher gold thickness than immersion gold in a single gold plating step. The hybrid EPIG/EPAG using RAIG gold produces the desired thickness without the complexity of an additional electroless bath.
The concept of reduction-assisted immersion gold RAIG baths is coming into its own as more manufacturers and OEMs recognize its benefits, most notably the ability to deposit a thicker layer of gold (3–6 µin) with no corrosion of the underlying nickel, in a single gold plating step.
This column originally appeared in the March 2021 issue of PCB007 Magazine.
More Columns from The Plating Forum
The Plating Forum: Reduction Assisted Immersion Gold for ENEPIG Surface FinishThe Plating Forum: Surface Finish Evolution from Conventional to Advanced
The Plating Forum: Plating in Electronic Applications
The Plating Forum: How the Pandemic Impacted PCB Manufacturing
The Plating Forum: The Significance of IPC ENIG Specification 4552 Revision B
The Plating Forum: The IPC Surface Finish Specifications
The Plating Forum: An Overview of Surface Finishes
The Plating Forum: DIG—The Next Generation