-
- News
- Books
Featured Books
- design007 Magazine
Latest Issues
Current IssueProper Floor Planning
Floor planning decisions can make or break performance, manufacturability, and timelines. This month’s contributors weigh in with their best practices for proper floor planning and specific strategies to get it right.
Showing Some Constraint
A strong design constraint strategy carefully balances a wide range of electrical and manufacturing trade-offs. This month, we explore the key requirements, common challenges, and best practices behind building an effective constraint strategy.
All About That Route
Most designers favor manual routing, but today's interactive autorouters may be changing designers' minds by allowing users more direct control. In this issue, our expert contributors discuss a variety of manual and autorouting strategies.
- Articles
- Columns
- Links
- Media kit
||| MENU - design007 Magazine
Estimated reading time: 3 minutes
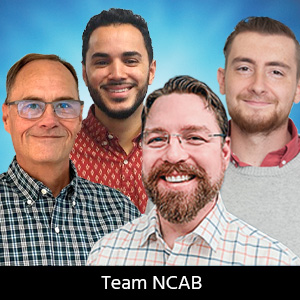
Fresh PCB Concepts: Does the Assembly Process Damage a PCB? (Part 1—Soldering)
A few years ago, a colleague contacted me with a question: “How can we solder boards with a Tg of 180°C or even 200°C at temperatures of 225-245°C without damaging the board? Even with leaded boards the peak reflow temperatures are way above the board’s Tg. How is this possible?”
The answer is simple. Every time a printed circuit board is exposed to soldering temperatures it is damaged. This is the case not only for lead-free soldering applications but also for eutectic soldering consisting of tin-lead. The Tg is one of several parameters to be aware of. In the case of Tg, many designers refer to the value as a gauge of stability. A high Tg product has less thermal expansion in the Z-axis. Below Tg the laminate epoxy resin system is hard and solid. You can expect the rate of thermal expansion to be around 25 ppm/°C. Above Tg the epoxy becomes soft and pliable. When the epoxy becomes soft and pliable the rate of expansion can be up to 10 times the expansion rate compared to the expansion rate below the Tg value. Tg 180°C material is more stable than Tg 140°C laminate due to the 40 degree range of the epoxy system remaining hard and solid.
The parameter that best determines when the board starts to take thermal damage is referred to as the maximum continuous operating temperature (MOT). MOT is a parameter that is tested for and certified by Underwriters Laboratories (UL). A bare board manufacturer shall build a qualification sample through their most destructive process and submit it to UL for compliance testing. A board with a certified MOT of 130°C shall take no thermal damage in the field when exposed to temperatures at or below 130°C. Above the MOT value the epoxy resin the PCB is made from starts to breakdown at the molecular level. As the molecular bonds break due to heat stress, energy is released. The released energy appears as smoke. The higher the temperature the board is exposed to the faster the damage occurs. Damage is cumulative.
Dry baking moisture out of a PCB is a good example of the damage threshold. For a PCB, the dry bake temperature must be above the boiling point of water (100°C) but below the MOT. Theoretically speaking, you can dry bake a board with a MOT of 120°C at 110°C for a year and the epoxy resin the PCB is made from shall take no thermal damage. Likewise, if the dry bake temperature is 121°C the epoxy resin would start taking damage. Theoretically speaking at one degree above MOT it would take months to do any real damage. At 300°C the PCB is damaged so quickly that delamination occurs in less than a minute. The higher the temperature the less time it takes to burn away the epoxy resin the PCB is made from. In reality, the MOT is the tested value. The actual PCB may exceed this value by a few degrees.
Every time a printed circuit board is exposed to assembly temperatures the epoxy resin holding the PCB together takes damage. This is the case for conventional eutectic soldering temperatures as well as lead-free soldering temperatures. This is where the decomposition temperature (Td) value comes in. By definition, this is the temperature at which a 5% weight loss occurs by thermal gravimetric analysis (TGA). Decomposition is the breaking of chemical bonds in the resin system. The epoxy resin in the laminate is basically burning up. A 2% to 3% weight loss of this nature will adversely affect circuit performance. The damage caused from decomposition is cumulative. This places a limit on the number of lead-free assembly cycles at temperature on a printed circuit board.
The higher the Td the slower the rate of burn. Materials with a Td at or below 300°C are fine for eutectic tin-lead soldering. Materials with a Td above and beyond 300°C are more suited for lead-free soldering. In this case, the higher the Td value the more thermally resistant the epoxy resin is, and the higher the better. Highly rated Td material shall still burn away but at a slower rate of decay. Lead-free assembly compliant laminates are typically phenolic cured epoxy systems. Phenolic cured epoxy systems typically have a higher Td compared to the traditional dicey cured epoxy systems. It is for this reason that dicey cured epoxy systems are not considered lead-free assembly friendly.
Soldering has always done damage to printed circuit boards. Tin lead soldering hasn't been damaging enough to be a big concern at the eutectic soldering temperatures applied. Lead free soldering is and should remain a concern to everyone.
David Duross is an engineering director for NCAB Group USA.
More Columns from Fresh PCB Concepts
Fresh PCB Concepts: Designing for Success at the Rigid-flex Transition AreaFresh PCB Concepts: More Than Compliance—A Human-centered Sustainability Approach
Fresh PCB Concepts: Assembly Challenges with Micro Components and Standard Solder Mask Practices
Fresh PCB Concepts: The Power of a Lunch & Learn for PCB Professionals
Fresh PCB Concepts: Key Considerations for Reliability, Performance, and Compliance in PCBs
Fresh PCB Concepts: Traceability in PCB Design
Fresh PCB Concepts: Tariffs and the Importance of a Diverse Supply Chain
Fresh PCB Concepts: PCB Stackup Strategies—Minimizing Crosstalk and EMI for Signal Integrity