-
- News
- Books
Featured Books
- design007 Magazine
Latest Issues
Current IssueAll About That Route
Most designers favor manual routing, but today's interactive autorouters may be changing designers' minds by allowing users more direct control. In this issue, our expert contributors discuss a variety of manual and autorouting strategies.
Creating the Ideal Data Package
Why is it so difficult to create the ideal data package? Many of these simple errors can be alleviated by paying attention to detail—and knowing what issues to look out for. So, this month, our experts weigh in on the best practices for creating the ideal design data package for your design.
Designing Through the Noise
Our experts discuss the constantly evolving world of RF design, including the many tradeoffs, material considerations, and design tips and techniques that designers and design engineers need to know to succeed in this high-frequency realm.
- Articles
- Columns
- Links
- Media kit
||| MENU - design007 Magazine
The Top Five Reasons Products Fail EMI Testing
May 12, 2021 | Kenneth Wyatt, Wyatt Technical ServicesEstimated reading time: 2 minutes
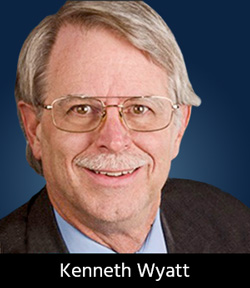
Introduction
The three top product failures I see constantly in my consulting practice are radiated emissions, radiated susceptibility, and electrostatic discharge. After reviewing and testing hundreds of products over the years, I’ve come to the conclusion that products fail these tests for five common reasons (somewhat in order of incidence):
PCB design—Poor layout and layer stack-up.
Cable shield termination and pigtails—Cable shields are not terminated to enclosure or lack of common mode filtering for unshielded products, plus shield pigtails used.
Gaps in the return path—High-frequency clocks or signals crossing gaps in the return path.
Power distribution design—Poor power distribution network (PDN) design.
Shielding design—Apertures or slots in the shielded enclosure that are too long.
1. PCB Design
The single most important factor in achieving EMC/EMI compliance revolves around the printed circuit board design. It’s important to note that not all information sources (books, magazine articles, or manufacturer’s application notes) are correct when it comes to designing PCBs for EMC compliance—especially sources older than 10 years or so. In addition, many “rules of thumb” are based on specific designs, which may not apply to future or leveraged designs. Some rules of thumb were just plain lucky to have worked.
PCBs must be designed from a physics point of view and the most important consideration is that high frequency signals, clocks, and power distribution networks (PDNs) must be designed as transmission lines. This means that the signal or energy transferred is propagated as an electromagnetic wave. PDNs are a special case, as they must carry both DC current and be able to supply energy for switching transients with minimal simultaneous switching noise (SSN). The characteristic impedance of PDNs is designed with very low impedance (0.1 to 1.0 ohms, typically). Signal traces, on the other hand, are usually designed with a characteristic impedance of 50 to 100 ohms.
Understanding PCB design is all about two important concepts: all currents flow in loops and high frequency signals are propagated as electromagnetic waves in transmission lines. These two concepts are closely related and coupled to one another.
Currents Flow in Loops
Circuit theory suggests that current flows in loops from source to load and back to the source. In many cases of product failure, the return path has not been well defined and in some cases, the path is broken. The problem circuit designers often miss is defining the return path of a high frequency signal back to the source. If you think about it, we don’t even draw these return paths on the schematic diagram—we just show it as a series of various “ground” symbols.
To read this entire article, which appeared in the May 2021 issue of Design007 Magazine, click here.
This article originally appeared in the January 2020 issue of Interference Technology and is reprinted here with permission.