-
- News
- Books
Featured Books
- design007 Magazine
Latest Issues
Current IssueAll About That Route
Most designers favor manual routing, but today's interactive autorouters may be changing designers' minds by allowing users more direct control. In this issue, our expert contributors discuss a variety of manual and autorouting strategies.
Creating the Ideal Data Package
Why is it so difficult to create the ideal data package? Many of these simple errors can be alleviated by paying attention to detail—and knowing what issues to look out for. So, this month, our experts weigh in on the best practices for creating the ideal design data package for your design.
Designing Through the Noise
Our experts discuss the constantly evolving world of RF design, including the many tradeoffs, material considerations, and design tips and techniques that designers and design engineers need to know to succeed in this high-frequency realm.
- Articles
- Columns
- Links
- Media kit
||| MENU - design007 Magazine
Meeting the Challenge With Design Reuse
May 13, 2021 | Stephen V. Chavez, PCEAEstimated reading time: 2 minutes
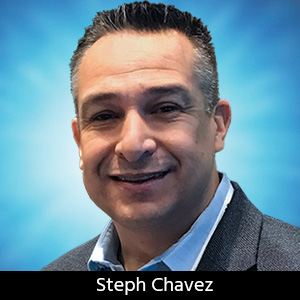
As project schedules get shorter and budgets get squeezed, project managers and small business owners must constantly look at ways to maximize limited funding and resources. But reusable PCB design IP allows us to investigate ways to potentially shorten design cycle time.
Typically, engineering teams are looking for ways to design PCBs faster, better, and cheaper, all with fewer resources. Within those engineering teams, today’s circuit engineers must meet three competing perspectives for success: layout solvability (DFS), performance (DFP), and manufacturing (DFM) requirements with the targeted end-result of maximum placement and routing density, optimum performance, and efficient defect-free manufacturing. I refer to this as the Designer’s Triangle.
A Variety of Challenges
Some of the biggest recurring problems in today’s PCB designs are challenges regarding DFM, constraints, board layout planning, and routing; in general, schematics capture, and documentation for both fabrication and assembly. No matter what EDA tool you are using, the general process is the same:
- Define requirements
- Create libraries if they don’t already exist
- Capture schematics to include constraints
- Integrate into PCB layout for parts placement and signal routing to include appropriate MCAD-ECAD handshakes
- Run SI/EMC/PI simulations (making layout adjustments as required)
- Generate final manufacturing outputs
- Release the final data into your respective product life management system
After this process is followed, send the released manufacturing data outputs to your suppliers to get the PCB fabricated and assembled. This is basically the same approach for design after design and has been for many years now.
However, we often step back and ask, “How can we design faster and better while cutting cost?” It’s tempting to start with your EDA tool, but is greater tool automation enough to make a significant impact here? I believe it can be, to a certain extent.
But in PCB design, the moment of truth comes when you get that initial CCA into the lab and start testing its functionality, especially if it’s an initial prototype. Will it work as designed and meet all the requirements? It potentially becomes Pandora’s Box at that stage in the overall design process. No matter how well you design that PCB layout, if the actual electrical circuit simply doesn’t work or it does not meet the end requirements, then it’s back to the drawing board and another re-spin. This is a recurring issue.
To read this entire article, which appeared in the May 2021 issue of Design007 Magazine, click here.