-
- News
- Books
Featured Books
- design007 Magazine
Latest Issues
Current IssueAll About That Route
Most designers favor manual routing, but today's interactive autorouters may be changing designers' minds by allowing users more direct control. In this issue, our expert contributors discuss a variety of manual and autorouting strategies.
Creating the Ideal Data Package
Why is it so difficult to create the ideal data package? Many of these simple errors can be alleviated by paying attention to detail—and knowing what issues to look out for. So, this month, our experts weigh in on the best practices for creating the ideal design data package for your design.
Designing Through the Noise
Our experts discuss the constantly evolving world of RF design, including the many tradeoffs, material considerations, and design tips and techniques that designers and design engineers need to know to succeed in this high-frequency realm.
- Articles
- Columns
- Links
- Media kit
||| MENU - design007 Magazine
EIPC Technical Snapshot Review: Microvia Reliability Issues
June 22, 2021 | Pete Starkey, I-Connect007Estimated reading time: 8 minutes
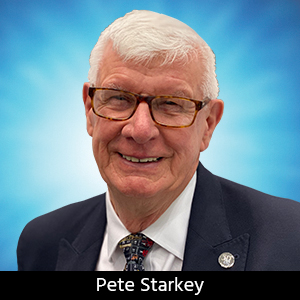
Since the mid-1990s, when they were developed for mass production in the mobile phone industry, microvias have become principal enablers for high-density designs, and have evolved from single-level to complex stacked and staggered structures. They are fundamentally robust interconnects, although some aspects of their reliability are still under investigation.
EIPC’s ninth Technical Snapshot webinar on June 16 brought together four leading specialists, each with a significant viewpoint, to present a hugely informative compilation of current knowledge on the theme of microvia reliability. The event was moderated by EIPC technical director Tarja Rapala-Virtanen, who commented that the work of understanding, identifying, and optimising processes for high-reliability applications required cooperation throughout the supply chain, with PCB manufacturers providing feedback and recommendations to designers.
She introduced the first speaker, Bill Bowerman, director of primary metallization with MacDermid Alpha Electronics Solutions, who focused on the critical importance of the proper cleaning of microvia target pads to remove all residues from the laser drilling process and return pad surfaces to the bulk copper condition to enable subsequent plating to proceed with good adhesion and a well-ordered epitaxial crystal structure. Indeed, control of all aspects of the manufacturing process became increasingly crucial as target pad diameters decreased and reduced contact areas meant that non-optimum conditions were increasingly likely to lead to failure.
He reviewed the characteristics of UV and combination UV/CO2 laser drilling processes, and the corresponding types and amounts of residues remaining on target pads, illustrated by SEM micrographs. UV lasers removed copper, glass, and resin by photon ablation; excessive energy could roughen the target pad and leave a residue of recast copper. CO2 lasers removed only glass and resin by thermal ablation and were stopped at the target pad leaving a thin resin residue on the copper which could subsequently be ablated by a de-focussed UV laser used in combination. Oxidation of the target pad during the cleaning process was a further potential source of contamination that could be difficult to troubleshoot.
Whatever the residue, it was vital that it be removed to ensure optimal adhesion. Bowerman described a typical process sequence for target pad cleaning: horizontal spray microetch, sweller, rinse, epoxy etch, rinse, neutraliser, rinse, glass etch, rinse. The objective was to bring the target pad surface condition back to its clean, bulk, microetched condition with minimal oxidation formation. He illustrated the effect of each process stage with SEM micrographs. It was important that the equipment design gave efficient transfer of process solutions into and out of the microvias, especially as diameters decreased. Traditional agitation methods were not particularly effective, and designs with tightly spaced direct-impingement nozzles were preferred.
Using micrographs of cross-sections, Bowerman showed comparative examples of the interfaces resulting from effective cleaning and incomplete residue removal. In the best case, the interface was almost indistinguishable and deposited copper grains were observed to undergo recrystallisation during thermal testing, whereas a lack of recrystallisation suggested the existence of some preventative barrier. Inspection of the type of fracture after pull-testing the microvia could be used as quick indicator of the effectiveness of the surface preparation process.
A logical follow-on from references to copper recrystallisation made during Bill Bowerman’s discussion of cleaning techniques for microvia target pads, the second presentation came from Dr. Sebastian Zarwell, R&D manager with Atotech Group. He explored and explained the metallurgical aspects of copper recrystallisation and the formation of epitaxial and non-epitaxial copper/copper/copper interfaces in stacked blind microvia structures, with regard to their thermo-mechanical reliability. The relevant interfaces were those between target pad copper, electroless copper and electrodeposited copper.
He showed examples with two different electroless coppers: one demonstrating epitaxial growth, the other non-epitaxial (Epitaxy means the process of growing a crystal of a particular orientation on top of another crystal, where the orientation is determined by the underlying crystal.) He had observed that non-epitaxial interfaces had a higher probability of cracking after a succession of reflow cycles.
Using techniques which included electropolishing and focused-ion-beam machining combined with scanning electron microscopy, and transmission electron microscopy combined with energy-dispersive X-ray spectroscopy, the copper/copper/copper interfaces had been precisely located and it could be seen that an epitaxial interface originated from the unhindered grain growth of copper crystals from the target pad into the nanoscopically fine-grained plated copper layers. A non-epitaxial interface indicated suppressed copper diffusion, caused by a high concentration of organic contaminants at the aligned grain boundaries. Energy-dispersive X-ray spectroscopy had detected only copper, nickel, and palladium at an epitaxial interface, whereas organic residues were present on the target pad on non-epitaxial examples. It had also been shown that a typical cause of a non-epitaxial interface between electroless and electroplated copper was a critically high codeposition of additives such as brighteners and levellers during the initial stages of electroplating.
“The microvia is the Ugly Duckling of PCB processing,” said Dr. Maarten Cauwe, R&D team leader of advanced packaging at the Interuniversity Microelectronics Centre (IMEC) in Belgium, who was a member of IPC’s committee studying weak microvia interfaces. At this EIPC webinar, he set out to give a higher-level view of some of the challenges in microvia design, modelling, and testing that he had encountered during an IMEC project funded by the European Space Agency (ESA). Referring to the reliability of HDI technology in general, his opinion was that the microvia would not be the first structure that could be expected to fail in a fatigue mode—features like buried vias and high-aspect-ratio through-vias would be more likely candidates. And with reference to the 16 pages of ESA microvia process guidelines, he used an elaborate Ishikawa diagram to summarise the processing challenges that could lead to weak microvia interfaces.
Design considerations for individual microvias included drill diameter, pad diameter, aspect ratio and placement with respect to other via structures, especially buried vias. For multiple microvias there was the additional issue of choosing between stacked or staggered configurations of which he showed a range of different examples, together with calculated values for strain under thermal cycling conditions. Regarding the design of test coupons, Dr. Cauwe advised inclusion of representative buried vias, and referred to the details of the propagated D-coupon in IPC-2221B Appendix A Version 2 .0, and a typical IST coupon.
“What makes testing microvias so challenging?” He explained that their small size made mechanical strain measurement difficult. And their tendency to self-heal during thermal cycling was a further complication. But simple microsectioning could still give useful information, even if the advanced techniques referenced in Zarwell’s presentation were not accessible.
Considering actual test methods and their associated test coupons, Cauwe cited IPC-TM-650 2.6.27B: convection reflow assembly simulation, IPC-TM-650 2.6.7.2C: air to air thermal shock, IPC-TM-650 2.6.26A, method B: current induced thermal cycling and IPC-TM-650 2.6.26A, method A: interconnection stress testing.
After demonstrating comparative test results for different microvia/buried via configurations and values derived from modelling, with calculated relative life expectancies, he concluded that there was no single, ideal test method to evaluate microvias. All test methods applied elevated stress levels to assess the quality of the microvia, and poorly manufactured microvias were detected by continuous resistance monitoring during stress application.
He emphasised that experience was key in evaluating test results. Test houses continued to learn every day and a thorough understanding of the impact of design variables, manufacturing processes and test parameters was probably more important than the choice of a microvia test method.
The technique of interconnection stress testing referred to by Cauwe was described in detail by Jason Furlong, CTO at PWB Interconnect Solutions in Canada, in his presentation entitled “Microvia testing and analysis of complex HDI designs using IST.”
Having reviewed the range of equipment and services provided by PWB Interconnect Solutions, he described the evolution of the interconnection stress test for microvias and associated coupon designs with examples from 1999 and 2020. Coupons were designed to replicate specific product types, and their structures had changed dramatically over the years. A whole range of failure modes had been observed—he listed eight: separation from target pad, microvia corner cracks, microvia barrel cracks, microvia pull-out, cap cracking, cap separation, buried via corner cracking, and buried via barrel cracking. Furlong commented that every industry sector had its own unique combination of failure modes, such that it was not possible to quote a common baseline. During more than two decades of operation, over 3,500 unique microvia IST coupons had been designed and more than 55,000 had been tested.
He showed an example of an X-type coupon, with standard general dimensions and features, but with a specific via pattern characteristic of the final product, and indicated six different configurations of microvia structure as described in Cauwe’s test programme.
The test method was taken from The European Cooperation for Space Standardization (ECSS) standard ECSS-Q-ST-70-60C. Furlong described the details of the actual testing by current-induced thermal cycling (IPC-TM-650 2.6.26 Method A) with continuous resistance monitoring of power and sense circuits, and reviewed the results in great detail. In fact, no failure occurred in the standard IST test, and six coupons were selected for continued extended testing to 5% fail at 190°C. One three-stack microvia coupon failed at cycle number 4272, one two-stack-plus-staggered at cycle 7199 and one staggered-plus-two-stack at cycle 11500. In each case, thermal imaging was used to identify the failing via which was then microsectioned to identify the cause of failure.
In all of the EIPC Technical Snapshot webinars that I have attended, I have never observed such an extensive Q&A session. The level of interest in the microvia reliability topic, the quality of the presentations and the willingness of the presenters to share their knowledge and experience resulted in the Q&A lasting almost as long as the webinar itself, and very few delegates signed off before it was over. Thank you, EIPC, for a splendid event.