-
- News
- Books
Featured Books
- design007 Magazine
Latest Issues
Current IssueProper Floor Planning
Floor planning decisions can make or break performance, manufacturability, and timelines. This month’s contributors weigh in with their best practices for proper floor planning and specific strategies to get it right.
Showing Some Constraint
A strong design constraint strategy carefully balances a wide range of electrical and manufacturing trade-offs. This month, we explore the key requirements, common challenges, and best practices behind building an effective constraint strategy.
All About That Route
Most designers favor manual routing, but today's interactive autorouters may be changing designers' minds by allowing users more direct control. In this issue, our expert contributors discuss a variety of manual and autorouting strategies.
- Articles
- Columns
- Links
- Media kit
||| MENU - design007 Magazine
Estimated reading time: 4 minutes
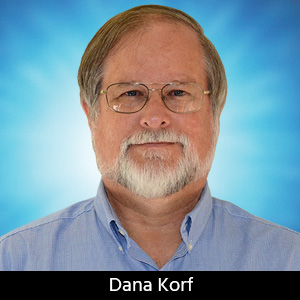
Dana on Data: The Critical Importance of the Fab Product Engineer
Billions of dollars are spent yearly on CAD and CAM software to produce complex PCB designs and fabricate PCBs. The final technical manufacturing decisions generally are made by one person for each design. This is the PCB fabricator product engineer (also called planner, pre-CAM engineer, MI engineer, etc.). But I don’t think most design, procurement, or NPI teams understand how critical this person is to the data transfer success and liability protection. One bad keystroke or misunderstanding can create a PCB that won’t meet customer expectations.
It is relatively straightforward to open the design data package, read all the non-intelligent data, run a design rule check on the provided digital data and create an error, sorry DFM, report to be negotiated with the designer. The complexity arises when the non-documented “rules” and history, when available, must be merged into the recommendation for DFM closure. And then just to help, the person only is scheduled to spend one hour getting to the final decision.
The initial DFM reviews’ intent is to balance the design technical requirements against the highest factory yield and lowest production and material costs in order to reduce manufacturing risks and maintain the highest yields. Projected yield may be lowered, and processing/inspection time increased to fit the design into the existing capability, but these can only be adjusted to a point where it won’t make business sense to try to build it. The PE will be in the middle of these negotiations.
PEs must ensure that every T is crossed, and I is dotted. This level of documentation is required for the day a customer calls and says, “The boards don’t work, it is all your fault, I’m sending them back and you’re paying for them all plus assembled parts.” One of first areas of investigation is the initial engineering change approvals that are documented during the DFM process. These show that the designer either proposed or at least approved of the change causing the issue. This can save the fabricator thousands of dollars.
Product engineers are the de facto technical owner for the design for the lifetime in the factory. All design modifications proposed during manufacturing and any single event adjustment that may be required must be approved by the PE prior to being implemented. They make the technical decision on whether the customer allows the modification without prior approval, or the line must be stopped to get approval. This is because there is significant soft knowledge that just can’t be documented or verified by the factory’s engineering or quality control departments.
What are some of these key soft knowledge and communication skill areas?
- Does the customer want a lot of feedback, or is feedback discouraged? (Sometimes this is a very emotional topic.)
- Do you know how to handle the response to “the last fabricator didn’t ask that question or have that problem” in a positive manner?
- Is there a CEM involved in the decision, and do they have a good communication channel with the designer? The PE needs to believe that a “right” answer is being received.
- What are the functional requirements of the PCB? Knowledge of the environmental, thermal, electrical, mechanical, flexibility, etc. requirements may influence material recommendations.
- Does the design conform to their own company spec, for which the fabricator may be held financially liable for if they are not compliant?
- Who has the final design control decision when the design is being ordered through a broker or CEM? Many responses may be received. But only the approved technical contact can make the final response.
- The PE must have an excellent understanding of the manufacturing process and capability.
- Which hard-and-fast fabricator process engineering rules can be broken and/or adjusted to get the design to fit?
- When does the PE call an internal meeting to discuss a proposed process, which in effect stops the progress of the tooling process?
- Have the knowledge to provide acceptable impedance controlled stackup modifications that only modify what the design team wants to be modified, though not specified.
- Ability to write the CAM editing instructions for approved adjustments.
- Create the special instruction notes for the production travelers.
- Understand what I call the DFM transfer mood. An example of bad juju is a designer in North America grudgingly having to interact with a lower-cost Asian source selected by purchasing as a cost reduction, instead of the local NPI shop they have been working with for years and have a good understanding with one another.
The bond and trust between the PE and the designer are unique. Once these engineers form a high comfort working level, it is not uncommon for the designer to request that same PE for every design. It is common for a highly functioning front-end engineering (FEE) team to assign a customer’s jobs to the same PE as much as they can. Of course, for PCB fabricators with hundreds of customers this may not always be possible for every design.
One wrong keystroke, one misinterpretation, and the PCB will not perform as expected. Fortunately, this does not happen often. When you are on your next Zoom call or visit to the factory, reach your hand out and thank them for their help as part of your NPI team. They’ll appreciate it.
Dana Korf is the principal consultant at Korf Consultancy LLC.
More Columns from Dana on Data
Dana on Data: Best Practices in Interpreting Drawing Notes—‘Use Latest Revision’Dana on Data: The Missing AI-NPI Link
Dana on Data: Merging 2D Electrical, 3D Mechanical Worlds
Dana on Data: Resurrecting IPC Class 1
Dana on Data: The Evolution of Fabrication Drawing
Dana on Data: The Insane PCB DFM Process
Dana on Data: eCAD PCB Design Deficiencies
Dana on Data: Nuke the Netlist