-
- News
- Books
Featured Books
- smt007 Magazine
Latest Issues
Current IssueWhat's Your Sweet Spot?
Are you in a niche that’s growing or shrinking? Is it time to reassess and refocus? We spotlight companies thriving by redefining or reinforcing their niche. What are their insights?
Moving Forward With Confidence
In this issue, we focus on sales and quoting, workforce training, new IPC leadership in the U.S. and Canada, the effects of tariffs, CFX standards, and much more—all designed to provide perspective as you move through the cloud bank of today's shifting economic market.
Intelligent Test and Inspection
Are you ready to explore the cutting-edge advancements shaping the electronics manufacturing industry? The May 2025 issue of SMT007 Magazine is packed with insights, innovations, and expert perspectives that you won’t want to miss.
- Articles
- Columns
- Links
- Media kit
||| MENU - smt007 Magazine
Factors Affecting Quality of Solder Joints in Multi-Busbar Interconnection
August 17, 2021 | Narahari S. Pujari, MacDermid Alpha Electronics SolutionsEstimated reading time: 1 minute
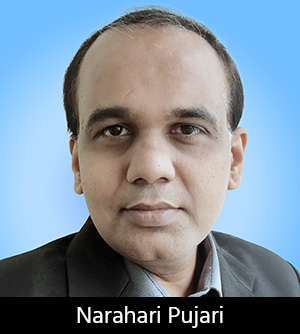
Introduction
Tabbing and stringing is the dominant method in the market for making crystalline silicon (c-Si) solar cell modules. Soldering ribbons are used as an interconnection medium in this process on the four or five busbars of the front- and back-side metallization. The process is well established and proven reliable [1]. However, there are still challenges to obtain high efficiency, cost-effective solar electricity. These challenges include [1,2]:
1. Low-cost manufacture with higher power output.
2. Reduce the amount of silver (Ag) paste per cell.
3. Achieve current redundancy.
4. Introduction of fine gridline print in front metallization to reduce electrical and optical losses.
5. Implementation of simple and low-cost processing along with advanced cell architectures to achieve higher efficiencies (>20%) in the field.
Amongst several new interconnection technologies, multi busbar (MBB) interconnection promises to alleviate some of the above problems. The technology was first introduced in 2006 [3] and over a period of time several approaches to achieve MBB interconnection have been emerged. Soldering [2], low temperature alloy lamination (Smart wire) [3,4], woven fabrics assisted soldering [5], and the prefabricated interconnected grid method (Merlin) [6], etc. to name few. The MBB technology of soldering is the closest to the traditional cell interconnection technology. The current module equipment can be upgraded to assemble MBB modules.
Schmid company was the first one to develop a special stringer machine for MBB modules. Now, several Chinese equipment manufacturers are developing this kind of machine. Typically, MBB cells are interconnected by seven to 15 solder coated copper wires with circular cross-section (diameter between 200 and 450 µm on each side of the solar cell. The wires are soldered by infrared soldering on silver pads printed on the front and back of the cells.
This article originally appeared in the August 2021 issue of SMT Magazine. To read the entire article, click here.
Testimonial
"The I-Connect007 team is outstanding—kind, responsive, and a true marketing partner. Their design team created fresh, eye-catching ads, and their editorial support polished our content to let our brand shine. Thank you all! "
Sweeney Ng - CEE PCBSuggested Items
Real Time with... IPC APEX EXPO 2025: Winner of the IPC Best Student Poster Award
04/29/2025 | Real Time with...IPC APEX EXPOSebastian Carrillo, winner of the Best Student Technical Poster Award, shares insights on his research in nanotechnology and plasmonics. His work on a metal insulator nano array focuses on light-matter interactions at the nanoscale. With advancements in manufacturing, applications include sensing technologies and photovoltaic systems. Sebastian discusses his project involving simulations and optical experiments. His career goals are in research, and he encourages students to seize academic opportunities.
Burkle's Marco Schaible Joins VDMA Photovoltaic Equipment Division’s Executive Board
12/13/2024 | Burkle AmericaThe Photovoltaic Production Equipment Department of the VDMA held regular elections at its board meeting on December 5 and confirmed the top management. Prof. Dr. Peter Fath, RCT Solutions GmbH, was re-elected as Chairman of the Board and Dr. Stefan Rinck, Singulus Technologies AG, was re-elected as Deputy Chairman.Burkle America is proud to announce that Marco Schaible, our Vice President of PV and Glass Solutions, has been confirmed as a member of the new Executive Board for the VDMA’s Photovoltaic Production Equipment Division. This appointment reflects Marco’s exceptional expertise and commitment to advancing innovation and competitiveness in the German-European solar machinery industry.
Gstar Announced the Strategic Move: Groundbreaking of Silicon Wafer Factory Construction in Indonesia
05/03/2024 | PRNewswireRecently, Gstar held a groundbreaking ceremony for its silicon rod and silicon wafer factory, marking the beginning of the rapid construction phase.
MacDermid Alpha Launches ALPHA SF828-MBB Photovoltaic Liquid Flux for Advanced Multi-busbar Interconnections
11/21/2023 | MacDermid AlphaMacDermid Alpha Electronics Solutions, a leader in integrated materials and technologies for the electronics industry, introduces ALPHA® SF828-MBB.
Cambridge GaN Devices, Neways Sign an Agreement to Develop Inverter Products
11/17/2022 | NewaysCambridge GaN Devices (CGD), a clean-tech semiconductor company that develops a range of energy-efficient Gallium Nitride (GaN)-based power devices that enable more sustainable electronics, and Neways Electronics (Neways).