-
- News
- Books
Featured Books
- design007 Magazine
Latest Issues
Current IssueAll About That Route
Most designers favor manual routing, but today's interactive autorouters may be changing designers' minds by allowing users more direct control. In this issue, our expert contributors discuss a variety of manual and autorouting strategies.
Creating the Ideal Data Package
Why is it so difficult to create the ideal data package? Many of these simple errors can be alleviated by paying attention to detail—and knowing what issues to look out for. So, this month, our experts weigh in on the best practices for creating the ideal design data package for your design.
Designing Through the Noise
Our experts discuss the constantly evolving world of RF design, including the many tradeoffs, material considerations, and design tips and techniques that designers and design engineers need to know to succeed in this high-frequency realm.
- Articles
- Columns
- Links
- Media kit
||| MENU - design007 Magazine
The EMS/Designer Relationship: Kelly's Story
August 25, 2021 | I-Connect007 Editorial TeamEstimated reading time: 3 minutes
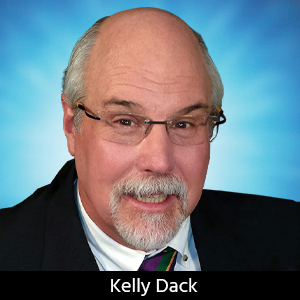
In a recent discussion with John Vaughan and Kelly Dack, we explored how parts availability information can reverberate back to the design team in unexpected ways. Dack starts this topic by pointing out a real-world situation that happens almost daily at a production EMS facility. In this part of the interview, Dack details how a parts availability issue can restart the design all the way back with the OEM design team.
Barry Matties: Kelly, you’ve been on the design side, and you’ve probably been in both circumstances where you’ve known the fabricator and where you have not known the fabricator at the beginning of the design process. What’s the contrast between those two?
Kelly Dack: The contrast is the different levels of communication. When I say communication, I mean documentation.
I’ve got a story that will explain the challenge. There’s a big shortage in the supply chains right now forcing us to swap out chips. Chips are becoming unavailable. In the EMS industry, there is a lot of redesign required because of chip availability issues. A board that’s been designed for five or eight years around a chip packaged in a quad-flatpack is suddenly unavailable and the only replacement may be a half millimeter pitch BGA. An outside designer, typically, will incorporate that new half millimeter pitch BGA into the existing design and lo and behold, they have to use a different scale in their routing technology.
The designer takes the existing 0.006” wide line and reduces it to get it down to 3.5 mil to break out of the BGA. That’s fine; it looks great on the screen. However, the fabricator, who has been building this board for years and years, doesn’t have the level of outer layer capability for print, etch, and plate of a three and a half mil line. Now what? That’s the problem. The designer says, “Any of our bare board prototype suppliers can do that.” Which is true. The existing offshore supplier, however, cannot.
This is the communication element. We must figure out a viable solution for the disconnect between the designer and the fab that builds this board. There are several ways to approach this. Could the designer have used via-in-pad or HDI technology to break out from this 0.56 millimeter pitch BGA? The supplier could make those adjustments, but the supplier can’t do outerlayer three mil, three-and-three spacing using the same stackup. The one ounce base copper is just too thick.
There are so many opportunities for disconnect after a design has been released for production and goes through change. Communication is the only way to see the project with success upfront. In other words, if the designer had access to the capability of the supplier building the board, the designer could have chosen the proper stackup and routing solution. Instead, because the designer chose a route without communication, it forced the EMS supplier to go source the board with viable material thickness, which is going to shoot the cost, quoting, and timing all over the map.
John Vaughan: Early alignment is critical in my view, so that it doesn’t end up with purchasing driving the decision-making process. Had the designer aligned early on with the PCB fabricator, that would have solved the issue, right?
Dack: Yes.
Matties: How much time would that have saved?
Dack: Everything is quick time to market; time is of the essence. So, when we discover that a chip is obsolete, or isn’t accessible, the clock is still ticking on the project. Typically, it can take a week or two in a production environment just to receive all the quoting back, then to get commitment for availability of the new part. I wouldn’t be surprised if it takes more than four to six weeks to implement a change like that.
Matties: That’s very costly.
Johnson: And yet this is more prevalent than it has ever been historically in our industry—all these components on extended lead time. Designers must manage, redesign, and even completely reconfigure their vendor list in order to deliver on this new design. There is so much to communicate.
To read this entire conversation, which appeared in the August 2021 issue of SMT007 Magazine, click here.