-
- News
- Books
Featured Books
- design007 Magazine
Latest Issues
Current IssueAll About That Route
Most designers favor manual routing, but today's interactive autorouters may be changing designers' minds by allowing users more direct control. In this issue, our expert contributors discuss a variety of manual and autorouting strategies.
Creating the Ideal Data Package
Why is it so difficult to create the ideal data package? Many of these simple errors can be alleviated by paying attention to detail—and knowing what issues to look out for. So, this month, our experts weigh in on the best practices for creating the ideal design data package for your design.
Designing Through the Noise
Our experts discuss the constantly evolving world of RF design, including the many tradeoffs, material considerations, and design tips and techniques that designers and design engineers need to know to succeed in this high-frequency realm.
- Articles
- Columns
- Links
- Media kit
||| MENU - design007 Magazine
Altium’s Nexar Platform Unites Design, Supply Chain, and Manufacturing, Part 1
September 2, 2021 | I-Connect007 Editorial TeamEstimated reading time: 6 minutes
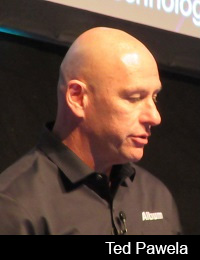
The I-Connect007 Editorial Team recently spoke with Ted Pawela, chief ecosystem officer and head of the Nexar business unit at Altium. Ted discussed Altium’s new Nexar cloud platform which aims to build an ecosystem that connects designers, supply chain companies, and manufacturers.
Andy Shaughnessy: Ted, start us off with some background on Nexar and walk us through what it’s like using it as a customer.
Ted Pawela: Nexar is closely related to Altium 365, the cloud platform that we introduced for our end users a little over a year ago, The Nexar brand refers to both a business unit within Altium, and our cloud platform to enable partners to participate in our electronics focused ecosystem. From a technology standpoint, we have a single cloud platform that is “double sided” in that one side faces users—Altium 365—and the other side faces partners. That is Nexar.
Nexar offers an API and access to all of the information that’s associated with the printed circuit board. We’ve been building an underlying data model that I like to call a PCB information model. This data model represents everything associated with the PCB, including all of the component and parts information, including manufacturability information, the design itself – literally everything needed to define a PCB.
Some of this is ready to access today, yet the work to make this fully complete is still underway. And there’s obviously a lot already there from our foundation of CAD tools, but we’re now working hard to build the PCB information model and API out to encompass all of the things that will make us more connected to other design tools, as well as manufacturing and supply chain.
For example, if you need to do signal integrity analysis, in general, what people do is export out of Altium Designer into an intermediate file format, then they’ll import that information into a signal integrity tool. Often this leads to translation errors that create more manual work for people, and worse yet, incorrect results. We want to eliminate all of that by providing direct access to PCB information in its original form. So in this case what we’re doing is offering API access for other software companies to be able to integrate their tools.
Nolan Johnson: Does this mean you can include core expertise along the entire design flow that you may not have at Altium directly?
Pawela: Yes. So that’s exactly what we’re trying to do. And for our partners, we like to say it’s zero friction, zero cost. We want to make it easier for you to easy for partners to do that. And the idea is that we think that we win off the back of creating a better user experience and then attracting more and more users to our tools and our platform and gaining market share in that way.
Johnson: This is an interesting concept. Traditionally, that data transfer from one tool to another has been a file exchange; it sounds like this is based more on a schema going into which different applications can plug to get the information they’re looking for.
Pawela: That’s exactly right. And the thing is we know that every time there is an export into a different format, whether that’s Gerber, ODB++, or something else, there are things that can go wrong. In terms of that translation, then you read it in and you translate it into yet another format. And that’s silly. If we could offer direct access to fit just the information that’s needed. And often in those kinds of integrations, you don’t need everything in the design. So it’s a waste to have to do that export and import of all the information if all you need are a few key parameters, for example.
Many people have asked all of us in this industry, for a long time, to make our file formats open. And so we’re doing that by exposing all of those parameters through a single, more modern API. And then that way, people can get access to any of our tools, whether it’s NEXUS, our enterprise PCB design product, or it’s Altium Designer, or even CircuitMaker.
Shaughnessy: You have partners that are both software companies and manufacturers. As a designer, I specify XYZ fab. What am I going to see about XYZ Fab?
Johnson: To build on Andy’s question, it seems pretty obvious how this works for a CAD tool. But once you start pushing the design down into the manufacturing chain, I would think things become a little different.
Pawela: Yes. This again is one of those areas where ultimately everybody who designs a PCB, generally, wants to get that PCB made. And that is a very inefficient process. I’ve heard from a lot of customers who say, “Why do you guys...?” And when they say you guys, they mean all of us, whether it’s ourselves or our competitors, but “why do you make me and my manufacturing partner go through this merry-go-round of sending my design files back and forth multiple times, across time zones and without any real context or intent explaining why I’ve chosen to do things a certain way, and delay my project by days or weeks? And by the way, when he tells me what those issues are, well, he’s not going to tell me in the context of my design. He’s going to send me an Excel file with a list of exceptions and I’ve got to go track down and figure out. And that’ll happen two, three, or five times on every board. I was hoping to get my PCB back in 10 days and I’ve spent 10 days and we haven’t even started manufacturing yet because we’re still talking about the design.”
That’s precisely the problem that we’re trying to address here by connecting the design activity with manufacturing in ways that make collaboration so natural you don’t even have to think about it. With context, or design intent made clear; in real-time or asynchronously, and in a way that makes design changes and the conversations leading to those changes a part of the design record.
Johnson: I’m hoping to paint a picture for the fabricators and the assemblers about how they interact with Nexar.
Pawela: Our plan is to enable them to connect their systems to receive customer design data directly to Altium 365. You may have seen that probably close to two months ago now we made an investment into a company called MacroFab that I’m sure you guys are quite familiar with. We’re working with MacroFab to figure out all the plumbing and carpentry required to connect the design environment to manufacturing partners and their CAM groups and so forth. And we’re working also with other of the tools providers that are closely connected to CAM like, for example, Frontline.
We’re in discussions with Frontline about how to connect their tools more closely with our tools so that again, there’s no file exchange, but also so that they have an opportunity for their customers, the fabricators, to give signals to the designers earlier in the process about things that may need to be adjusted, or they might want to consider and so forth.
We’re working through that now. It’s our expectation and our plan that we’re going to target January of 2022 as the moment that we would effectively launch the service from within Altium 365. You’ll be able to ask for a board to be manufactured and get a price and pretty much instantly know your turnaround time.
To read Part 2 of this conversation with Ted Pawela, don’t miss the September issue of PCB007 Magazine.