-
- News
- Books
Featured Books
- design007 Magazine
Latest Issues
Current IssueAll About That Route
Most designers favor manual routing, but today's interactive autorouters may be changing designers' minds by allowing users more direct control. In this issue, our expert contributors discuss a variety of manual and autorouting strategies.
Creating the Ideal Data Package
Why is it so difficult to create the ideal data package? Many of these simple errors can be alleviated by paying attention to detail—and knowing what issues to look out for. So, this month, our experts weigh in on the best practices for creating the ideal design data package for your design.
Designing Through the Noise
Our experts discuss the constantly evolving world of RF design, including the many tradeoffs, material considerations, and design tips and techniques that designers and design engineers need to know to succeed in this high-frequency realm.
- Articles
- Columns
- Links
- Media kit
||| MENU - design007 Magazine
From DesignCon: Insulectro Educating Designers About New Materials
September 9, 2021 | Andy Shaughnessy, Design007Estimated reading time: 9 minutes
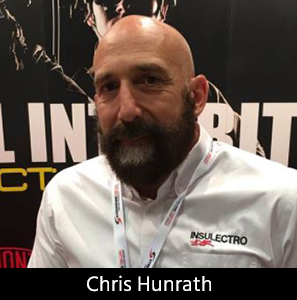
I recently met with Insulectro VP of Technology Chris Hunrath at DesignCon 2021. We discussed a variety of new laminates that Insulectro is distributing, as well as some newer processes and the need to educate designers on the ins and outs of cutting-edge laminates.
Andy Shaughnessy: Hi, Chris. Long time, no see. How are things going at Insulectro?
Chris Hunrath: It’s been a while, hasn’t it? We’ve been busy on a lot of different fronts. Certainly, there have been a lot of challenges with getting certain materials with the container terminal issues. But we’ve also been working on a lot of new technology, and some old technology that’s new to PCBs. One example is mSAP. There’s been a lot of interest in mSAP, the modified semi-additive technology. We’ve been working on some thin dielectric materials. Film-based dielectrics are something we’ve been working with on the DuPont side for some time. But it’s having higher relevance now.
We’re seeing some unusual copper weights for these new high-power chips, like 1.5-ounce copper. We’re just in the middle of introducing a new embedded resistor technology. So, yes, there have been several areas where we’re working on some new technology.
Shaughnessy: As far as the additive and the semi-additive processes, how do they change a designer’s job?
Hunrath: Well, I like to say you’re basically standing the trace on edge. A trace that would be, let’s say, a half-ounce thickness, which is about 0.7 mils give or take, might be 3 mils wide. Imagine a trace that’s 1 mil wide, but 1 or 2 mils tall. Now that could be good or bad, depending on what you’re designing.
For a differential pair, that could be a useful thing. Really modified semi-additive has been around a long time, used in chip packaging and more recently in mobile devices, but it’s not that common in larger PCBs. We have some materials that make that more feasible to bring into most PCB shops. Then it opens up some design opportunities that you wouldn’t normally have. And mSAP even has the potential for yield improvement on designs that utilized plated subs by both improved plating wrap and fine line circuit formation.
Here’s the best way to think of mSAP: Instead of printing and etching a foil of a given thickness, you’re electroforming the traces in a plating bath. And what you can do with light through photoresist is different than what you can do with etch chemistry on copper foil. That allows us to get to the geometries you can’t do with regular print and etch.
Shaughnessy: And that gives you the straight trace wall?
Hunrath: Right. It gives you straight trace walls, but also you’re not having to etch sideways when you etch down through a thicker foil. At the same time, you’re reaching down, because you’re imaging a photoresist with the light through the thickness of the photoresist. It’s just a way of being able to electroform your traces, and you don’t have some of the restrictions from basically the physics of the chemistry reacting with the copper foil.
Shaughnessy: It opens up a can of worms, mainly in positive ways, but there are some things that you have to do differently, right?
Hunrath: Yes, but it opens your design possibilities. You can put the traces closer together, but more importantly you can make the traces taller and not have to worry about etch factors. From a design standpoint, I think the designers need understand that the PCB fab capabilities are different than the chip package fab but mSAP brings these closer together on the larger landscape of the PCB. In combination with the fabricators, the PCB designers just have to get a handle on what is possible. Then I think you’ll see some things change.
Shaughnessy: What segments of the industry would you think are going to benefit most from mSAP?
Hunrath: Well, certainly organic chip packages or interposer boards, to some extent, those things. But there’s no reason why you couldn’t use it on, let’s say, a tight BGA fan-out or a high pad-count BGA package. This is one example of the technology, and it might not be on every layer. Let’s say only layer two would have this modified additive process for the fan out. PCB fabricators are already doing sequential lamination where you laminate, drill, plate, image, plate again and repeat. They’re doing this multiple times anyway. Just changing out the foil, or in the case of an Averatek process, using that seed layer, the other process steps would be basically the same. The major difference is the base foil or conductor is very thin. In my example, layer two would be where you use the ultra-thin conductor and be the layer where you do that tight fan out.
Shaughnessy: Are today’s EDA tools set up to do this? Does the designer using a typical tool have to do anything differently for additive processes?
Hunrath: Well, certainly the design rules would have to change and/or the rules for DFM would have to change. Because again, you can do things with this that you couldn’t do normally. So that’s one aspect of what we’re seeing interest in. But the other thing is embedded passives. And with DuPont we have some new liquid Kapton technology that allows you to print high-temperature resistors on inner layers. And from the printer electronics industry, there are some new tools to be able to do the printing. No board shop I know of wants to go back to screen printing in a big way.
It’s not that they couldn’t do it, but if you look at our market, it’s more of a small quantity, high-mix market. With an inkjet printer, that’s a whole other story. It’s fine for things like solder mask and legend. But it’s not necessarily good for either resistor or conductors because the particles have to be a certain shape to work with those kinds of conductive inks. But with DuPont’s new liquid polyimide technology and a nozzle printer, we could do some things now we couldn’t do before. We have some folks interested in working with us and developing that technology, where you could just print your resistors on your inner layers. It’s cool and I’m looking forward to it.
Shaughnessy: Are you still going out and teaching the designers about how to use this material?
Hunrath: Through COVID and the pandemic, we’ve been doing a ton of webinars. We had a series of webinars that were general topics where anybody could sign up and join. But we’ve also been doing individualized webinars where a particular customer, whether it be an OEM or fabricator, would get together online and we would present a topic of their choice. These were mostly either design or material science-based. Or a little bit of both, depending on what their interest is.
Shaughnessy: In one of our surveys, we asked designers what they have trouble keeping up with. And a lot of them said material options, because there are so many new laminates coming online.
Hunrath: It’s a hot topic right now. I mean, it’s everything from copper foil to resins to mSAP foils, because it can all go along with the mSAP technology. I know I’m jumping around a little bit, but what goes along with this is high-resolution photoresists that can do that work. Because you need a resist that’s thick enough to be a mold for the plating if you’re electroforming your circuits. But it has to have that capability of being able to do those fine features in the higher thicknesses.
Everything from imaging to embedded passives, I mean, we can do webinars on any of those topics. And we have some design experts with us now, people like Mike Creeden have been great because they’ve been able to get customers the solutions they need, both from a design standpoint and a material standpoint.
Shaughnessy: Yes, a lot has happened in the last 18 months. The last time I saw you all was at DesignCon and IPC APEX EXPO last year.
Hunrath: Yes, this is overdue. It’s nice to be able to meet with folks again. Even though we’ve been able to do a lot online, it’s just not the same. It’s nice to get out and see folks again. I’m hoping we don’t go back to where we were year ago.
Shaughnessy: I don’t think we will. I think we’ve had enough lockdowns.
Hunrath: I don’t think so either. But we’ve stayed very busy. And we’re still challenged in bringing new people into the industry. That’s something that we try to do. I don’t know if you’ve seen any of our PumaNews newsletter, but there are a whole string of topics that we publish on every month.
Shaughnessy: I’ll have to check that out.
Hunrath: We cover everything in PumaNews, from material science-based stuff to design things to some things that are more personal. We tend to do a feature on some of our employees each month. I’m trying to use that as a way to attract some new people in the industry.
Shaughnessy: For 10 years or so, I didn’t see any young people coming into this industry. But that’s changing as I see more young people in PCB design and manufacturing now.
Hunrath: Yes. There are some fabricators and some CEMs that have done a better job than others in bringing people into the industry. Hopefully that will continue. We, along with some other companies, participate in the USPAE (the U.S. Partnership for Assured Electronics). One of the topics that came up is bringing new people into the industry.
I’ve talked to some folks who are either chemical or mechanical engineers, and they thought they’d be doing something in high-volume manufacturing, like manufacturing toilet paper or something along those lines. They interned at a PCB shop and they’re thinking, “Well, this is interesting.” And they’ve stayed in the business and I’m hoping to see more of that as time goes on. But we’ve got to get out there and get that message out.
Shaughnessy: Yes. It’s a great industry.
Hunrath: Yes, it is. I think in the U.S., too, people are starting to appreciate the importance of keeping, at least some of it, viable here in the states. It could be a good career for somebody. And you’ll never be bored. There are plenty of things to do in many different area, whether it’s design side, fabrication, or materials.
Shaughnessy: Will you be at PCB West?
Hunrath: Yes. It’s in our backyard; at least, the backyard for one of our most important branches.
Shaughnessy: Are you going to have a big party at IPC APEX EXPO?
Hunrath: We’ll have our get-together, what we call the Epic Event. And at the show, we’ll also have a large booth where we create a technology village. It’ll be DuPont, Isola, and the copper foil folks from Denkai. We’ll have a big group there. And this way, both OEMs, designers, and fabricators can come and see information on a lot of different products all at once.
Shaughnessy: It sounds good. Good seeing you, Chris. Thanks for speaking with me.
Hunrath: Thank you, Andy.