-
- News
- Books
Featured Books
- design007 Magazine
Latest Issues
Current IssueProper Floor Planning
Floor planning decisions can make or break performance, manufacturability, and timelines. This month’s contributors weigh in with their best practices for proper floor planning and specific strategies to get it right.
Showing Some Constraint
A strong design constraint strategy carefully balances a wide range of electrical and manufacturing trade-offs. This month, we explore the key requirements, common challenges, and best practices behind building an effective constraint strategy.
All About That Route
Most designers favor manual routing, but today's interactive autorouters may be changing designers' minds by allowing users more direct control. In this issue, our expert contributors discuss a variety of manual and autorouting strategies.
- Articles
- Columns
- Links
- Media kit
||| MENU - design007 Magazine
Estimated reading time: 5 minutes
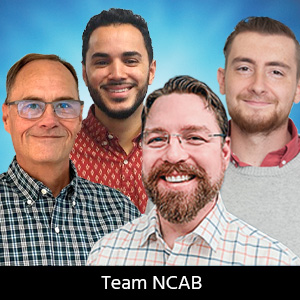
Fresh PCB Concepts: High-tech PCBs from Design to Volume Production
When producing high-tech PCBs from design to volume production, this is an area where customers often do not reach their initial targets regarding time, cost, and performance. With this column, let’s explore this topic.
NCAB Group as a whole last year produced 4,100 new high-tech parts, requiring close cooperation with our customers. I bring this up because, after this many jobs together, we have learned from each other about what is important when producing high-tech PCBs
We define the following as high-tech since these areas/products are where higher demands need to be placed on suppliers:
- HDI
- Flex
- Flex-rigid
- Rigid
- Impedance
- Blind via holes
- Buried via holes
- IPC type VII plugging
- Aspect ratio ?8:1
- Tight tolerances
Based on what we learned, these are the most important factors when producing a high-tech PCB.
- Total project cost: It is important to make it right from start and choose technologies and features carefully. The PCB price is determined here, but it is even more important that the total cost is under control.
- Time: In our business, that is “time to production,” where design and prototypes are milestones to reach the overall target—volume production.
- Quality: That the PCBs have the performance and process window to become producible in volume with good yield, and so that the next steps—assembly and box build—work seamlessly and smooth.
- Competence: Applied knowledge, i.e., knowledge that is close to where the questions arise. The applied knowledge of the design will “live and follow” the PCB and the application during the whole product lifecycle.
- Process control: This is one of the most important factors—to have correct initial value/input, not only for how you can produce, but how the PCBs are actually produced. This is the key to be able to take responsibility for a successful result; for design, prototypes and the cost of volume production.
The three phases of producing a new part all affect and overlap with each other.
Figure 1: The three phases of producing a new part.
Design
Here the creation starts; 85–95% of the cost and function is determined in this phase. All decisions regarding performance, quality, and process window are determined, as well as the price. A design that is based on knowledge of volume production is almost exclusively cheapest and takes the least time from the project start to full volume production.
Prototype
This phase is important because this is when the design is tested. Here it is important to be in control of the features that differentiate prototypes and volume deliveries. It is optimal when prototypes and volume go through the same manufacturing process. Many people claim that time is one of the most important factors in this phase, and I agree, but most important is that the prototype delivery is relevant for future volume (it cannot go any faster than that).
Volume
The target is that volume deliveries shall always be the best and most cost-efficient. To succeed, knowledge about the manufacturing process and the capability is absolutely crucial. This is where the true cost will be exposed. A good design in a badly matched process is expensive, either overcharged or with insufficient quality. On the other hand, a bad design cannot be “fixed,” regardless of process; the result is almost always wrong price and low quality.
The link between design and volume is absolutely crucial, particularly with high-tech, complex boards. It is very important to make a specification of the features and quality you are seeking.
Besides expertise, there are tools needed to support a project. A DFM from your supplier on the artwork of a design will generate reports for design rules, same net spacing, measures of different features, etc. Using tools for adjusted stackups has also become more common. Controlled impedance demands even more.
Every effort should also be made to ensure the boards are built to smoothly transfer into volume production at a later stage. This is especially true for more complex builds where stackups are vital and impedances need to be transferable to later full volume production. It is my experience that prototype factories typically solve what needs to be solved in order to deliver on time, and consequently the feedback of any possible problems or improvements are left out.
One should always consider seamless production when it comes to build-up and material features so that the prototypes delivered will function in coming volume production. In this stage all engineering questions (EQs) are addressed to assure the design and prototype are optimal for volume production.
Capabilities should also be tested at any factory used. The reason is simple: If you look at each factory´s website, they offer a broad capability. Each technology within a factory needs to be qualified within a capacity range.
Let’s use microvia as an example. Most factories have laser drills for drilling the holes, but this is not enough to produce high-quality microvia. Demands need to be put on the plating processes that will fill the holes with copper, which is the most crucial step. Furthermore, it is important with correctly operated cleaning rooms and layer stack processes.
PCBs are designed, manufactured and built into a PCBA according to IPC standards. There are however a variety of limitations in IPC. Underlying specifications should be put in place as well which will fill these limitations. One example is the surface treatment lead-free HAL. According to IPC, it shall be covering and solderable. This is not good enough as it can generate problems in the supply chain. By 60 µm, thickness problems might arise in the SMD process with paste print; on the other hand, “covering” is a rather weak statement. Our specification demands 1–40 µm because we know by experience that it will enable 12 months solderability and a good process window.
When designing and producing any PCB, a variety of factors need to be considered to get from the initial design to volume production. But with a high-tech PCB these factors are even more crucial. Complex designs will always increase both the cost and concerns for quality on a PCB and are not as easily able to be transitioned to volume production. This needs to be considered during the initial concept of an idea, and I always recommend involving your supplier as early as possible in the design phase.
Ruben Contreras is a program manager and field application engineer at NCAB Group.
More Columns from Fresh PCB Concepts
Fresh PCB Concepts: Designing for Success at the Rigid-flex Transition AreaFresh PCB Concepts: More Than Compliance—A Human-centered Sustainability Approach
Fresh PCB Concepts: Assembly Challenges with Micro Components and Standard Solder Mask Practices
Fresh PCB Concepts: The Power of a Lunch & Learn for PCB Professionals
Fresh PCB Concepts: Key Considerations for Reliability, Performance, and Compliance in PCBs
Fresh PCB Concepts: Traceability in PCB Design
Fresh PCB Concepts: Tariffs and the Importance of a Diverse Supply Chain
Fresh PCB Concepts: PCB Stackup Strategies—Minimizing Crosstalk and EMI for Signal Integrity