-
- News
- Books
Featured Books
- design007 Magazine
Latest Issues
Current IssueAll About That Route
Most designers favor manual routing, but today's interactive autorouters may be changing designers' minds by allowing users more direct control. In this issue, our expert contributors discuss a variety of manual and autorouting strategies.
Creating the Ideal Data Package
Why is it so difficult to create the ideal data package? Many of these simple errors can be alleviated by paying attention to detail—and knowing what issues to look out for. So, this month, our experts weigh in on the best practices for creating the ideal design data package for your design.
Designing Through the Noise
Our experts discuss the constantly evolving world of RF design, including the many tradeoffs, material considerations, and design tips and techniques that designers and design engineers need to know to succeed in this high-frequency realm.
- Articles
- Columns
- Links
- Media kit
||| MENU - design007 Magazine
Why Good PCB Data Management is Essential
November 9, 2021 | Dana Korf, Korf ConsultancyEstimated reading time: 2 minutes
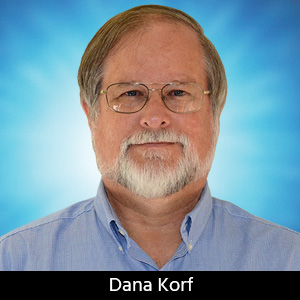
“Data really powers everything that we do.” – Jeff Weiner, LinkedIn
Manufacturing data management consists of four primary components: data transfer, data storage, revision control, and data access.
The PCB fabrication and assembly data management system and process is required to be robust to protect customer IP and ensure that the proper data is used to build the product. The entire process assumes that the provided design data package can’t be built as-is. The design data must be updated/completed after it is received by the manufacturer. Powerful CAD/CAM software has made it easy for designers/companies to pass the final editing and revision control on to their manufacturers. Over time, nefarious entities have significantly improved their ability to steal/copy data in parallel with this, thus complicating data transfer and management.
Conceptually, the required design data should be sent as a single intelligent file to the manufacturers, so production tooling is created without any human intervention. The standard industry process is still based on sending multiple files within the data package. These include the Gerber graphical data, Read.me ASCII file, PDF formatted fabrication print, etc. These files may be sent together in the same Zip/TGZ file or at separate times. This method requires humans to review these files since they often have conflicting data and/or violate the OEM’s acceptability and/or manufacturing capability/preferences. Intelligent data formats, such as IPC-2581, eliminate the additional, and often conflicting, documents by incorporating the intelligence in the CAD data.
Data Package Security and Transmission
When I went through ITAR training many years ago, the most interesting information was how people, companies, or governments would gather pieces of product data and then piece it all together so it could be duplicated. The information could be gathered by breaking into the data storage system, employees copying files and selling them, and/or by intercepting emails.
In one instance that I was involved in, a large OEM contacted my company and asked why we were building their boards, in volume. We checked our records and told them that we didn’t have any order from them. So, they sent us a copy of their data package. We did a database query for datasets with similar characteristics; low and behold, we found a dataset that was an identical match but ordered by another company. In another case, we received an order for a consumer PCB that had a ship-to address for a jewelry dealer in a large Asian city. We informed the OEM, and they took on the investigation at that point. We obviously refused the order.
There are many methods to transmit data between companies using various security methods with complex encoding/decoding protocols. The specific method is generally specified by the ordering company. Good data management is also required within a manufacturing facility to restrict data access to only those who require it. It also denotes that individual logins/passwords, not generic logins for a team of people, are required to log who accessed the data, when it was accessed, and who modified any data. This includes going all the way down to the actual equipment.
To read this entire article, which appeared in the November 2021 issue of Design007 Magazine, click here.