-
- News
- Books
Featured Books
- design007 Magazine
Latest Issues
Current IssueAll About That Route
Most designers favor manual routing, but today's interactive autorouters may be changing designers' minds by allowing users more direct control. In this issue, our expert contributors discuss a variety of manual and autorouting strategies.
Creating the Ideal Data Package
Why is it so difficult to create the ideal data package? Many of these simple errors can be alleviated by paying attention to detail—and knowing what issues to look out for. So, this month, our experts weigh in on the best practices for creating the ideal design data package for your design.
Designing Through the Noise
Our experts discuss the constantly evolving world of RF design, including the many tradeoffs, material considerations, and design tips and techniques that designers and design engineers need to know to succeed in this high-frequency realm.
- Articles
- Columns
- Links
- Media kit
||| MENU - design007 Magazine
From DesignCon: What’s Old is New Again with Selective Heat Sinks
November 16, 2021 | Andy Shaughnessy, Design007 MagazineEstimated reading time: 8 minutes
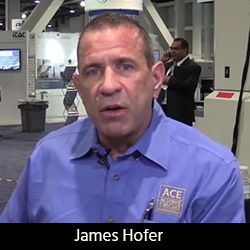
I met with James Hofer, General Manager of Accurate Circuit Engineering, during DesignCon 2021 in San Jose. He discussed some of the new technology they’ve been working on, including copper coins. James explains the benefits of making copper coins—a technology that’s been around for years—in 3D and even laminating them into the board to control heat in one area.
Andy Shaughnessy: How’s it going, James?
James Hofer: It’s going well. It’s been a while, Andy.
Shaughnessy: It has been a while. I understand that you’ve been working on some pretty cool things at ACE. Why don’t you give us an update?
Hofer: We’ve always got cool things going on at ACE. That’s exactly what ACE is all about—manufacturing cool things. Right now, I would say one of our standout technologies that we’re working with is copper coins. Copper coin is not a new term; copper coins are selective heat sinks. They’ve always been in a two-dimensional use. What’s new and exciting about what we’re doing now is looking at them not as a flat chunks of copper that are made into a circle or a square that you embed into a PCB. That technology is not necessarily new, and heat sinks aren’t new.
Let me digress a little. The benefit of a selective heat sink or a copper coin is less weight. You can put the heat sink in the area where it’s needed and not across the entire board. Up until today, that technology has been very linear and two-dimensional. You make it flat. You make it in different thicknesses, and you make it in whatever size you need. It provides a smaller more intimate heatsink with less weight and space than a standard heat sink.
What we’re doing now is milling and forming these selective heat sinks into different shapes and heights. Rather than put a flat, round, 30-mil thick copper coin into a board, we’ll instead make it with some podiums so that the heat sink gets mounted to the board and is below level, except in particular areas where you bring it flush to the surface of the board, or even higher.
We are also developing ways to laminate them into the boards so that the heat sink isn’t a square or a circle, but instead a small post, which, like a plated-through hole, will conduct heat and current. A copper coin that’s a post can be laminated into the board, not a hole, so now a component can sit on it and heat can be pulled directly down that post. What’s nice is that you don’t have a lot of weight because there’s no extra copper that is not directly being used.
We’ve been working on several different ideas and implementing some of them. Some of those are going on vehicles that can’t carry a lot of weight like drones or on wearable tech. We’ve been using some very interesting styles of heat sinks in those. We are also putting them into other packages that have very small form factors. It’s hard to put a 30-mil copper coin on a board that’s 20 mils thick and one inch by three quarters of an inch. But I can machine those coins down to very small, selective areas, and again, when I use the term coin, it actually refers to a selective heat sink. When I can make those into three-dimensional structures and laminate them into the circuit board, the possibilities become quite creative. That is what we do best “bring ideas to reality.”
Shaughnessy: Isn’t that a pain in the butt for you to manufacture?
Hofer: Well, I hate to say it, but that’s the other description of ACE. We are not the guys you go to with a punch and crunch circuit board that anybody can build. We are the “pain in the butt guys.” When somebody else says “no,” we’re usually the guys who get it done. In fact, I have three customers who literally came to us saying, “I don’t think this can be done because the last two places we went to could not do it.” And we did it.
I guess the pain in the butt is training your brain to think outside of the box to stop looking at it the same way you’ve looked at it for many, many years, and instead, try to make a fresh slate of your mind. You have to say, “If I could do this, would that work?” That’s one of our in-shop jokes: “We’re too stupid to say no.” But, when you don’t say “no,” then you must find a way to make it work.
We have literally, at times by trial and error, found a way to make it work. Once you make the first one work, the technology follows behind it. It’s like in the old days: The first time somebody made a 3-mil line and space, the next day, everybody wanted 3-mil line and space.
We like that. I personally find that exciting and rewarding because it opens brand-new doors. As you know, ACE is all prototype. We want to be on the leading edge of technology. We want to do the stuff the other guys can’t. I get hurt when I get a quote for something that everybody can build and they go, “Wow, your prices are so high.” Yes. Because anybody can build a six-layer board. I could build one in my garage. But, with a three-dimensional copper coin embedded in six different spots in a three-inch board, well, not everybody can do that, and no one can do it in their garage. That’s where we stand out.
Shaughnessy: What would a designer need to know to start implementing the selective heat sink?
Hofer: Call your fabricator, because the technology is still in its infancy and there are no set rules of what you can and can’t do. Some of the stuff that we’re doing, other folks would literally say, “It can’t be done.” I would say to the designer, number one, release your limitations, think outside the box, and then consult with your fabricator. Sometimes people know the answer, but they need somebody to tell them what it is. Kind of like when you say, “Where are my glasses? Oh, they’re here on top of my head.”
Shaughnessy: I do that quite frequently.
Hofer: No, the technology’s not easy. It’s unique. But what makes it exciting is that it opens up an entire new way of thinking about heat sinks. That’s where we’re at now, and I love it.
Shaughnessy: That’s great. And you also have some new RF microwave technology going on.
Hofer: Yes. Before RF, back when we were at 2G cell phones, we made the decision that RF microwave and antennas would be the wave of the future. It was one heck of a good move, because right now everything is about how fast and how far it can transmit. The days of physical wiring and fiberoptics are going away. The way to really reduce limitations is to be able to send everything through RF, through microwave, and to do that, you must have antennas. That’s what we specialize in. We make some of the best in the business. I wish I could tell you some of the stuff we’re making. I wish I could.
I have some cool boards in my booth, but I can’t put the really cool stuff out because it’s still too new technology. RF and microwave is going up and up, and faster and farther, and we are there with it.
Shaughnessy: That worked out. So, I know that you all stayed open throughout the lockdown, and you gave your employees cleaning solutions to disinfect their homes. You really looked after your staff.
Hofer: We never were allowed to shut down the facility. We had several tier one prime contractors send us letters about the importance of essential businesses staying open. We put in a very robust and generous process to keep COVID out of the facility. We’ve had a multitude of employees stay home with pay because they may have been exposed while outside the shop and didn’t know if they had COVID, and that’s our policy. You think you might have been exposed, don’t come to work. Text us. We’ll pay you to stay home. While that might sound expensive, in the end it is just smart.
We have been in business since COVID started. We’re still going full speed, where some facilities would have to shut down for a day or two because COVID was brought into the workplace. The cost of that is far more than the cost of reassuring your employees that they’re covered no matter what and asking them to stay home. We, to this day, are COVID-free. Those policies have been lightened a little due to vaccinations. Though, I am honestly considering whether I should tighten them up again because of the Delta variant.
Most of my employees still wear masks. All my unvaccinated workers, although I’m not allowed to know who they are, all wear a mask. We still offer our employees $50 if they get vaccinated. I think we’re at 83% vaccination rate.
Shaughnessy: It’s an interesting dynamic, where the personal meets the professional. Well, it’s been great talking with you, James. Thanks for your time.
Hofer: Great talking to you, Andy. Thank you.