-
- News
- Books
Featured Books
- design007 Magazine
Latest Issues
Current IssueProper Floor Planning
Floor planning decisions can make or break performance, manufacturability, and timelines. This month’s contributors weigh in with their best practices for proper floor planning and specific strategies to get it right.
Showing Some Constraint
A strong design constraint strategy carefully balances a wide range of electrical and manufacturing trade-offs. This month, we explore the key requirements, common challenges, and best practices behind building an effective constraint strategy.
All About That Route
Most designers favor manual routing, but today's interactive autorouters may be changing designers' minds by allowing users more direct control. In this issue, our expert contributors discuss a variety of manual and autorouting strategies.
- Articles
- Columns
- Links
- Media kit
||| MENU - design007 Magazine
Estimated reading time: 8 minutes
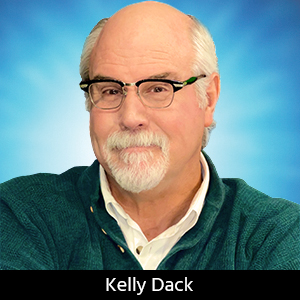
Contact Columnist Form
Target Condition: ‘Dealing’ With PCB Design
Welcome to my new column, where I will be pursuing the need for stakeholder advocacy in the printed circuit board industry. I’ll be deliberating topics essential to helping all of us understand what each PCB project stakeholder needs to achieve 100% acceptability for their stake in a PCB design project. These requirements will be expressed using the same helpful, graphic target condition example methodology which is utilized in the IPC-A-600 and A-610 specifications. I’m looking forward to exploring along with you, the PCB stakeholder, the target condition requirements for PCB sales and business development, engineering, design, procurement, manufacturing, test, inspection, and customer satisfaction.
Stakeholder—There is Power in the Term
Regarding the overall success of the PCB industry, it has been written in the pages of this publication that “Everything starts with design.”1 I agree with this statement as long as the definition of design is based upon a project team approach, one which recognizes all the players or “stakeholders” who have a vested interest in the overall success of a PCB assembly project. There is power associated with the role of a stakeholder. Most PCB project stakeholders are not designers per se, but they have just as much of a vested interest in winning. They are empowered by the knowledge, capabilities, and skill they have managed to acquire over time, but they are too often dis-empowered by being overlooked and misunderstood by other stakeholders due to project team oversights which do not consider their unique requirements far enough in advance.
Winning in the business of electronics must include all aspects of producing a successful printed circuit assembly. Every aspect is represented by a skillful stakeholder who, together with the project team, step up to play their hands against “the house”—the customer or entity which makes all the rules. Individual stakeholders must consider the odds together as a project team before going all in. This is far from a scenario of winner takes all because to get a PCB project successfully to market it takes all to win.
What’s at Stake?This crucial question has been asked around casino gaming tables long before printed circuit project proposals ever existed. When powerful players stepped up to a table, they first had to ante up with something of value—cash, a promissory note or even a deed to property—to offer as a stake in the game.
Any PCB stakeholder—a designer, contractor, supplier management professional, bare board supplier, or electronic manufacturing services (EMS) company—must consider what is at stake before engaging in business. The savvy stakeholder realizes there is risk involved in doing business. Failure to count the cost of the project and consider all the available stakeholder resources required to play in the game risks the valuable time and financial resources of the associated stakeholders if unforeseen odds or circumstances should arise. Too many projects are put at risk of folding due to blatant disregard for stakeholder requirements. If something is at stake, it might be lost or damaged if the players are not successful playing their hand at the table.
After the Dealin’ is Done
Your company has won the business and is revving up to produce the new project. What could go wrong? Plenty, if your fellow-stakeholders don’t get a chance to play their hands. This continues to be a sad fact cited in many a PCB project team’s post-mortem review. Some examples:
- The PCB design routing and stackup was approved and released before the production supplier ever had a chance to verify material availability
- The layout was populated with parts which were not verified for cost
- The layout was sent out for fabrication before the test engineers had a chance to evaluate for accessibility
- The EE forgot to tell supplier management that certain features on the PCB could only be manufactured by a sole source
The list goes on and on. I am a rabid advocate for DFX in printed circuit design. I’ve read, written, and taught extensively on the subject. But now, going into my seventh year working within an EMS organization as a design and manufacturing liaison, I am continuing to see a steady disregard for basic manufacturability, materials sourcing, assembly, and test. Has the predicted tsunami of new EE graduates been too quick to learn the layout tools? Too quick in outputting data “for” their downstream stakeholders before learning what they really need? In many cases, yes. But fresh EE designer stakeholders don’t know what they don’t know. They’ll continue leaning forward, independently running with scissors, so-to-speak, until their fellow stakeholders can kindly and gently introduce them to an extended project team that compels them to learn to provide manufacturing data feasible for helping them to hit their target conditions.
The Thanksgiving I Overplayed My Hand: A DFT Story
I prepared a turkey for my family one year at Thanksgiving. I sourced the bird. I obtained the propane-powered base, frying kettle, and the peanut oil. I watched the “how to” video on YouTube to become a quick expert on how it was done. I lowered the bird into the hot oil and watched it boil to a crispy doneness. I carved it up, plated the meat and placed it upon our kitchen island for all to enjoy. While I had processed this endeavor alone in the safety of the backyard, taking just a quick 30 minutes, my family had been working together all day inside, making stuffing, seasoning, and creating all the side dishes for a traditional turkey dinner which they savored for hours as it roasted in the oven.
To make a long story short, my DFT (deep fried turkey) project was a flop. It missed everyone’s target condition. Good thing there was a diverse project team of family stakeholders working together on a viable alternative. I spent all afternoon working on a deliverable which I alone had determined my family needed. In the end, they didn’t need it. It wasn’t working for them. The crispy skin had a hankering of rancidity from the peanut oil. The meat tasted like peanut oil. It was a Thanksgiving turkey project only a mother could love. My mom did, in fact, empathetically take a slice of breast meat and compliment me on my efforts while she laboriously chewed away on it. Later in the evening she had to pass on the pumpkin pie—her favorite—because her stomach had begun to hurt.
Have we arrived at a time in which there is entirely too much written each month on the topics of designing “for” someone? Is the “design for” message being misconstrued by some, as in my DFT example?
On that day, harmony and fulfillment were experienced by all who worked in the kitchen on the roasted turkey project. Everyone seemed to know what to do and who to call for help. Convection oven profiles were set to ramp up, preheat/soak times were minimal, and peak temperature was set to an even 350°F, calculated and set at 13 minutes per pound “based” on an unstuffed “turn-key.” The succulent meat was successfully excised from its carcass and each side of the breast was gently lifted out by one family stakeholder, set upon the cutting board and precisely cross-cut against the grain by another. This project was a success because the family stakeholders worked together throughout the process by communicating and agreeing on what it takes to meet the target conditions for the entire project team.
Working Together, We Can Beat the House
But can our entire industry of PCB project stakeholders be helped to meet their target conditions? Perhaps it is time for the PCB industry to start designing “with.”
Part of the success of this column will involve reaching out to you regularly to make contact. I want to talk to and hear about your unique experiences as you strive to achieve the target conditions of your specialized requirements for PCB product development. With your help and permission, I want to collect and re-tell your accounts of stakeholder success and failure. You can remain anonymous if you wish, but the idea here is to share your story so we can learn from it. Second, I want to connect you with other potential project stakeholders who can become as familiar as family to you. Who knows? You and that new stakeholder contact might end up working together someday on the same project and be able to help each other reach your target condition requirements.
Who Says You Can’t Choose Your Family?
I know a lot of wonderful people in the PCB industry—stakeholders—each with their own set of target conditions which I want to help them hit. But a quick search on LinkedIn shows there are thousands more of you whom I do not yet know. Perhaps we can connect through this column to share and help others.
I don’t presume to know every PCB project stakeholder’s job inside and out. Over the course of the past few decades, I’ve spent time in my industry roles as a PCB designer, and more recently as a PCB design and manufacturing liaison, learning a lot about stakeholder challenges. But I want our readers to hear these challenges from you so we can process this and learn together. Again, please contact me on LinkedIn or through my column page if you would like the PCB project world to know more about your role in the industry so we might help.
The Denouement: Read ‘Em and Weep
Concurrent engineering (DWF or design with fabrication) and training for evolving manufacturing practices are needed now more than ever. For the short term, our PCB project stakeholder community must become more “woke” to stakeholder limitations and more supportive of present stakeholder capabilities for their short-term projects. Connected, automated, smart factories and the software and systems which support them are here and more are coming quickly. PCB stakeholders must become aware of what is coming so they can adjust, prepare, and tool up because competition and advancements in technology without first building stakeholder relationships and awareness can cause project teams to call the bets before these stakes are raised considerably.
Thankfully, the I-Connect007 family of PCB industry publications provides a voice for PCB project stakeholders to share this information. Month after month, we read about what to watch out for in design in order to avoid overplaying a fellow stakeholder’s hand. May we all become tuned in to one another’s target condition requirements for success and strive to help one another achieve it.
See you next month or sooner!
References
- Everything Starts With Design, Design007 Magazine, June 2019.
More Columns from Target Condition
Target Condition: Floor Planning Without a FloorTarget Condition: The 5 Ws of PCB Design Constraints
Target Condition: Are Autorouters Friend or Foe?
Target Condition: From Dream House to Drill Files
Target Condition: Designing vs. Inventing
Target Condition: ‘Boomer to Zoomer: Do You Copy?’
Target Condition: Advanced Packaging Technologies—Look Before You Leap
Target Condition: My Anti-venom to PCB Cost Adders