-
- News
- Books
Featured Books
- smt007 Magazine
Latest Issues
Current IssueWhat's Your Sweet Spot?
Are you in a niche that’s growing or shrinking? Is it time to reassess and refocus? We spotlight companies thriving by redefining or reinforcing their niche. What are their insights?
Moving Forward With Confidence
In this issue, we focus on sales and quoting, workforce training, new IPC leadership in the U.S. and Canada, the effects of tariffs, CFX standards, and much more—all designed to provide perspective as you move through the cloud bank of today's shifting economic market.
Intelligent Test and Inspection
Are you ready to explore the cutting-edge advancements shaping the electronics manufacturing industry? The May 2025 issue of SMT007 Magazine is packed with insights, innovations, and expert perspectives that you won’t want to miss.
- Articles
- Columns
- Links
- Media kit
||| MENU - smt007 Magazine
Estimated reading time: 6 minutes
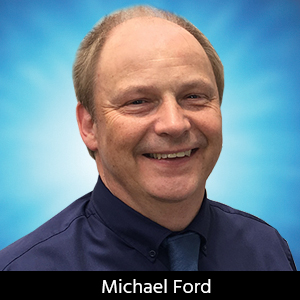
Smart Factory Insights: Digital Transcendence—Fear of The Unknown
The first three industrial revolutions have brought us automation of physical tasks through adoption of mechanical and electrical machines, the benefit of which has been quite easy to appreciate. Industry 4.0 automation, however, is driven almost exclusively from the digital realm, representing a whole new world of intangibility. With manufacturing being rather averse to unplanned change or risk, unless there are very compelling reasons, how do we get to fully trust digital technology needed for our businesses today, taking us toward manufacturing digital transcendence?
Wouldn’t it be amazing to have god-like powers, to be able to look down across the completely automated factory that simply, efficiently, and perfectly, making whatever products are required, whenever needed, and without human dependencies? All actions and activities would be automated in the mix of mechanical and software automation, lights out. This is the extreme and potentially obtainable goal, but with quite a few challenging steps to be taken in getting us there.
Several steps have already been taken. Data captured from machines and operations can be more instantly transmitted and contextualized for various uses today than ever before. We can remotely monitor machines and operations from the other side of the planet, if we so wish. Software has been evolving, not only to bring us, as humans, holistic factory information, with which we make operational decisions in a faster, smarter, and more reliable way, but has already started to make those decisions for us. We accept results, for example, from automated inspection and test machines that alert us to potential quality issues, instruction from Lean supply-chain tools that orchestrate material logistics based on production progress and planned future activities, and actionable information from dashboards that alerts us to trends.
Hang on a minute. Do we trust all these decisions? Smart software technology is still evolving, with many challenges yet to fully overcome. It starts with the problem of data collection. Other than IPC-CFX, for which not every machine vendor has yet received IPC qualification, other data exchange technologies do not guarantee the integrity, content, or meaning of information, leaving gaps in the data that often go unobserved. Decisions are being made by software automation that are based on access to only a certain part of the true holistic picture. Proof of this is apparent as we see examples that include:
- Instances of work-orders being created and scheduled by ERP without the actual physical materials being available
- The failure of an in-circuit test operation resulting in a “no fault found”
- A dashboard indicating a ridiculous number for OEE at the start of a production run
These are all examples of where data and software are incomplete, that contextualization is being assumed or even guessed. How many times do we turn off and on again our computers, phones, tablets, printers, televisions, etc.? Something went wrong, something quite unknown to us, but we know enough about what to do to fix it. This does not inspire confidence.
Today’s reality is that we will not transcend into the full digital world of Industry 4.0 until these kinds of problems have been solved and trust created. This is not an unexpected issue per se. We continue to use human operators for assembly tasks that automation, even after many years of evolution, has not yet found a way to competently and cost effectively replace. The same is, of course, happening in software, with “AI” algorithms evolving over time, with improved visibility and therefore decision-making, though we are much closer to the start of the journey with software than we are with hardware automation, a whole +1.0. We find ourselves therefore on a progressive journey.
The trust element is vital for ongoing adoption. Almost all of us are still driving our cars manually, even though more automated features are being added, such as LIDAR-driven emergency braking and automated steering following the lines on the road, are successfully being introduced. However, we don’t yet totally trust that the software can provide full autonomous driving in all conditions. Is it the software itself that we don’t trust or something else? Hardware failures are also possible, which are addressed, we expect, by a degree of redundancy and fail-safe design. Far more likely would be the problems with the vast variety of road conditions due to unexpected or unrecognized fixed and mobile hazards, weather events, and human nature. Some very clever people work on the development of automotive software, yet the most important people in the mix are those who implement and experience it, then provide feedback as it works in the real world.
The same is true in the evolution of artificial intelligence (AI) manufacturing software. To whatever extent software is “smart” in today’s world, it takes an inspired and informed user to get the most benefit from the software’s functionality, and to understand the real opportunities and limitations. To be afraid of the software, to install it, and then, from a distance, expect to have it work without ongoing interaction and support is counterproductive. With mechanical automation, we have accepted the necessity to keep an eye on the performance and efficiency, as maintenance and repair will ultimately be needed. Software does not wear out, and there is no need for users to get into the bits and bytes levels of detail, but it is essential to understand how the software becomes progressively integrated as a member of the overall manufacturing resources team. As manufacturing practices develop and evolve toward digitalization, more software functions will be utilized, driving further benefits and new functional development, extending the reach of the software “AI,” creating further business opportunities.
For this whole scenario to be an acceptable part of manufacturing, there needs to be visibility, trust, and flexibility between customers and software vendors that reduces the risk of any adverse issue. What is most effective is selecting the right tools that enable low-risk, trustworthy functionality, and interoperability, and that progress at a rate at which manufacturing practices evolve. Bespoke software and middleware components should be avoided, as by their static nature, and bring limitations and barriers which eventually trigger step-changes in solution choices. Products from companies offering holistic, yet fully interoperable solutions, based around industry standards and thought leadership, represent a great start.
Customers of manufacturing operations today are expecting to see a plan. To not have a plan toward digitalization is increasingly being seen as a wasted opportunity, a risk that competitiveness, and hence customer value, is not being taken seriously. As with climate change, no one expects to create the fully autonomous digital factory overnight, but manufacturers should be putting into place the education, skills and strategy needed that take smart manufacturing toward its end goal. Each company will adopt different paths, as priorities and software selections differ. Having people in the organization with the right skills and expectation is essential. As holistic “AI” utilization within manufacturing is probably not on offer from most universities currently, human resource managers need to search for those candidates who are able to grasp the vision and methodology for manufacturing digitalization, to grow their experience and allow them to gain the trust within the organization.
To achieve manufacturing digital transcendence, we need to know what we are transcending into, and trust those who are enabling that journey for us, in this case, driven by incremental creation of benefits, all of which align to medium- and long-term business goals.
This column originally appeared in the December 2021 issue of SMT007 Magazine.
More Columns from Smart Factory Insights
Smart Factory Insights: Making Rework a Smart Business OpportunitySmart Factory Insights: The Sustainability Gold Rush
Smart Factory Insights: Today’s Manufacturing Jobs Require a New Skill Set
Smart Factory Insights: Compose Yourself, Mr. Ford
Smart Factory Insights: The Smart Business Case for Local PCB Manufacturing
Smart Factory Insights: Manufacturing Digital Twin—Spanners in the Works
Smart Factory Insights: Machines, People, and AI
Smart Factory Insights: Is Sustainability in Manufacturing a Benefit or Burden?