Estimated reading time: 3 minutes
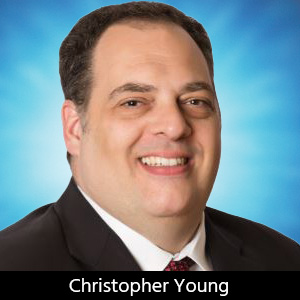
Adventures in Engineering: Supply Chain Management
AS9100 Revision C, released in 2009, was meant to make risk management an integral part of avionics product development and production. In addition, it required the measurement of a multitude of key metrics: delivery performance, requirements conformance, and eliminating re-occurring corrective actions to name a few. AS9100 Revision D, released in 2016, further bolstered the intentions of Revision C by increasing the emphasis on risks encountered in overall company operations and risks involving human factors1.
As “just in time” has become “just late” and many of us are struggling to avoid “just not going to happen,” perhaps we should examine our supply chain situation, learn from it, and adjust (AS9100, Revision E).
Toward the end of 2021, the National Business Aviation Association (NBAA) indicated, “Low inventories and longer shipping times are threatening to disrupt the flow of aircraft parts.” In particular, the NBAA announced, “One of the most pronounced shortages involves the semiconductor chips at the heart of many modern aircraft systems.”2 These semiconductor supply issues seem to be driven primarily by the following: A series of unfortunate semiconductor fab fires, a large rise in demand preceded by a pandemic-induced lull, and labor shortages. Traditional avionics product development timeframes have ranged from 18–36 months and aircraft Line Replaceable Unit (LRU) production lead times were around 20–30 weeks. Semiconductor component lead times have pushed upward of 70-plus weeks, roughly equaling the lower end of a traditional product development cycle and two to three times that of typical production lead times.
Highly extended component manufacturing lead times lead to component unavailability among commonly approved distributors (such as Digi-key, Mouser, Arrow, Newark, Avnet etc.). The current drought of highly complex semiconductors (FPGAs, microprocessors, microcontrollers) has caused a rush to non-standard supply chain alternatives (brokers), significantly increasing production costs. My experience with legitimate brokers is that I can typically obtain hard to find components at five to 10 times the original component cost plus the labor cost of the non-conforming material report (NCMR). These NCMRs routinely involve a material review board comprised of engineering, manufacturing, and quality personnel, a lot of people’s time and thus a lot of the company’s money being spent. Keeping with the intent of the latest AS9100 quality standards increased efficiency and reduction of non-conforming material is of keen interest. I suggest that quality processes be updated within avionics organizations such that proven “non-standard supply chain alternatives” be an allowable path such that it does not trigger an NCMR. I believe the current semiconductor supply issues will provide opportunities for gathering data on alternate component distributors (brokers). This data can then be used as a means for providing structured guidance for using component brokers in avionics supply chains in a future revision of AS9100.
Component availability dominance within avionics development programs have typically been limited to ASICs and to have the availability or rather the shortage of general-purpose semiconductor ICs dominate development programs has felt unusual at best. Until the last couple of years, I have not experienced widespread shortage of semiconductor ICs as a roadblock to a development project. The issue at hand is that the design engineers typically need access to components, demo-boards, and preliminary/integration prototypes to produce a design such that a functional prototype can be built to production standards (conformity), roughly speaking. This functional prototype can then undergo certification testing (DO-178, DO-160, MOPS, etc.) to obtain any applicable technical standard order authorizations (TSOA) and/or type certificates (TC). AS9100 in its current revision requires the use of a proven development process. Many companies adopt a process based on the Hardware Design Life Cycle, as described in RTCA/DO-2543, which include informal design verification throughout the conceptual/preliminary and detailed design phases. Formal verification activities (typically used as credit/evidence for certification) are performed as a step toward transition into production. The before-mentioned verifications require physical hardware and present a major delay in development with lead times easily exceeding 52 weeks (a calendar year). I suggest updating quality processes such that components for engineering development may be purchased and stored through production for multipurpose use (formal/informal verification) by a set of processes rather than a bill of materials (BOM). Components can be identified and acquired early in the design process or even prior to it (research) as a means of expediting access of hardware for verification.
These are only two examples of how processes may be adapted to meet the challenges widespread semiconductor IC shortages pose. And yes, they are simple in concept and possibly difficult in detail, but worth consideration given these unprecedented times.
References
- AS9100, Wikipedia.com.
- “Overcoming Supply Chain Challenges,” NBAA, Nov/Dec 2021.
- RTCA/DO-254, Design Assurance Guidance for Airborne Electronic Hardware.
Chris Young is owner/lead engineer at Young Engineering Services LLC.
More Columns from Adventures in Engineering
Adventures in Engineering: A Penny Primer on PCB Design FundamentalsAdventures in Engineering: 5G Expansion and Radar Altimeters
Adventures in Engineering: Data Management Not Just Checking the Boxes
Adventures in Engineering: Connectors—The Right Fit
Adventures in Engineering: A Purpose-Driven Prototype
Adventures in Engineering: Test Points—The Other Side
Adventures in Engineering: The Ecosystem of Autonomous Flight
Adventures in Engineering: It's Pronounced 'Tooling Holes'