-
- News
- Books
Featured Books
- pcb007 Magazine
Latest Issues
Current IssueThe Hole Truth: Via Integrity in an HDI World
From the drilled hole to registration across multiple sequential lamination cycles, to the quality of your copper plating, via reliability in an HDI world is becoming an ever-greater challenge. This month we look at “The Hole Truth,” from creating the “perfect” via to how you can assure via quality and reliability, the first time, every time.
In Pursuit of Perfection: Defect Reduction
For bare PCB board fabrication, defect reduction is a critical aspect of a company's bottom line profitability. In this issue, we examine how imaging, etching, and plating processes can provide information and insight into reducing defects and increasing yields.
Voices of the Industry
We take the pulse of the PCB industry by sharing insights from leading fabricators and suppliers in this month's issue. We've gathered their thoughts on the new U.S. administration, spending, the war in Ukraine, and their most pressing needs. It’s an eye-opening and enlightening look behind the curtain.
- Articles
- Columns
- Links
- Media kit
||| MENU - pcb007 Magazine
EIPC Technical Snapshot: A European Roundup
March 2, 2022 | Pete Starkey, I-Connect007Estimated reading time: 16 minutes
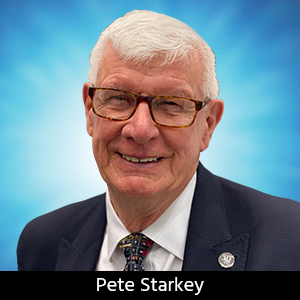
Although it was originally proposed to hold a one-day face-to-face EIPC conference in Frankfurt, travel restrictions in Germany made this impractical. But the Technical Snapshot webinar format has proved so successful that it was decided to run an extended version as an alternative—two sessions, with three presentations each. It worked extremely well. The carefully selected program on February 23 featured excellent speakers, and seamless organisation added up to an outstanding event.
Europe’s Financial Outlook
EIPC board member Dr. Michele Stampanoni, vice president strategic sales and business development at Cicor Group, moderated the morning session, which began with a business outlook on the global electronics industry with emphasis on Europe, prepared by Jon Custer of Custer Consulting and presented on his behalf by EIPC president Alun Morgan.
Morgan began by summarising the situation at the end of 2021, when global GDP had exceeded the 2020 figure by 5.7% although he reminded us that 2020 had been a bad year to compare with. In fourth quarter 2021, GDP was up by 6.9%, but that could be attributed largely to inventory increases. If these were excluded, GDP was effectively up by 1.9%. Consumer prices had soared by 7% in the fourth quarter. Port closures and the blockage of the Suez Canal had caused supply chain disruptions, and it was expected that supply reliability would continue to be an issue in 2022, as well as a continuing rise in transportation costs. Semiconductor sales had been very strong, growing by 25%, and the growth was expected to continue in 2022. Global PCB output grew by 9.9%.
The global outlook, based on World Bank figures for real economic growth from 2019 through 2021 with estimates for 2022 and 2023, indicated that the Euro Area had been the worst-hit in 2020 with -6.5%, whereas China had maintained a positive GDP growth of 2.2% in 2020 rising to 8.0% in 2021 with 5.6% forecast for 2022 and 5.3% for 2023. Corresponding figures for the Euro Area were 5.1%, 4.4%, and 2.2%.
Although European industrial production clearly showed a very sharp dip as we entered the pandemic in early 2020, the composite graph for the Euro 28 countries afterward continued its previous trajectory. There was concern that growth in individual countries like France and Germany continued on a declining trend for specific reasons.
Purchasing Managers' Indices had always been considered key indicators by Custer Consulting, and comparison of January 2022 with December 2021 values for the U.S., Europe, UK, Germany, France, and Japan showed some slowing-down in the U.S. and Germany, although Morgan stressed that all the values were better than 50%, suggesting growth rather than contraction.
The world electronic equipment monthly shipment graphs predictably showed China as the dominant market, with a very clear pattern of seasonality. There was a dip corresponding to the beginning of the pandemic, but this was followed by a dramatic recovery.
The bar chart comparing global electronic supply chain growth in 2021 with 2020 was strongly positive, with the exception of business and office reflecting working-from-home, and a significant negative in the automotive sector for a variety of causes additional to the pandemic effect. The automotive situation was similar in Europe. In the aerospace sector, although civil aircraft production had been severely affected, the space industry had fared quite well.
Overall, 2021 was a better year in most European countries. There was strong growth in PCBs and growth would continue in 2022 but to a lesser degree. Supply shortages, shipping costs, prices and inflation were areas of concern. Shipping costs in particular had risen spectacularly.
Morgan turned his attention to technology trends, and listed the top 10 according to Finances Online: IoT connectivity, robotics adoption, AI, and cognitive transformation, augmented analytics, API-driven productivity, customer support chatbot, blockchain innovation, and digital twin. In his opinion, the key trends to watch were artificial intelligence and augmented reality.
In conclusion, the outlook for 2022 is that growth will continue in all major subsectors. Projections by Deloitte anticipate a GDP growth in manufacturing of 4.1% for 2022. Supply chain disruptions will continue, with shortages and high delivery costs creating headwinds for shippers at a time when demand remains high. Worldwide inflation will likely remain near 5.0% in early 2022 before gradually easing in response to declines in industrial and agricultural commodity prices. On an annual basis, global consumer price inflation will average 4.1% in 2022 before subsiding to 2.8% in 2023. More than 1.3 trillion semiconductors devices are expected to ship in 2022 and PCBs are expected to grow by 8% globally.
Axiomatic and DSM Design Methodologies
Alex Stepinski of Smart Process Design in Poland, a specialist in advanced manufacturing and high-output, cost-efficient value creation, gave some knowledgeable insight into opportunities for European re-shoring with a technical roadmap exploring the economic viability of greenfield PCB fabrication.
His agenda began with an introduction to the principles of axiomatic and DSM design methodologies. I learned that axiomatic design is a systems design methodology using matrix methods to systematically analyse the transformation of customer needs into functional requirements, design parameters, and process variables. Design structure matrix (DSM) methodology is a tool for analysing and managing complexity in a project by focusing on interactions and interfaces between project elements.
In a PCB manufacturing context, he compared brownfield and greenfield fabrication projects. Brownfield facilities typically had equipment of various vintages with varying chemistries, and a lot of variation in people and their experience. The big difference with the greenfield was that everything was put together as a single project and it favoured the use of axiomatic design principles. Functional requirements would be developed to meet specific customer attributes, followed by the development of design parameters and process variables. With everything calculated to be independent it was straightforward to manage and to model.
To adopt such principles in a brownfield situation is much more complex, but a start can be made with a design structure matrix: products, people, skills, and process activities, all mapped to each other, and the nature of the interaction identified at each interface. Tools are available to enable efficient roadmaps to be developed using the axiomatic approach to greatly improve the efficiencies of the system.
Stepinski turned his attention to green technologies, mentioning that there were already a few facilities in the U.S. running with close-to-zero water consumption. Latest techniques even enabled zero consumption using humidity from the air to replace water lost to fume extraction. Open-source zero-liquid-discharge system designs are currently on the market, for which capital expenditure was up to 40% less than conventional systems and operating expenditure between 30% and 92% less, giving proven returns-on-investment of two to five years.
He estimates that 70% of PCB fabrication chemicals are recyclable with current technology, but recycling is typically used only for generic commodity chemicals because proprietary process suppliers are very protective of their formulation details.
On the subject of automated handling, Stepinski sees the Pareto frontier for low-mix mass production to be low-tech in-line automation, whereas the Pareto frontier for high-mix new-product-introduction or brown-field is based upon custom automated-guided-vehicle systems. But in-between new product introduction and mass production, automation is typically surpassed by low labour costs. He suggested a new product family approach to the work cells based on a production part approval process and product lifecycle management with process: product interface mapping. Although collaborative robots offered some opportunities, he considers there is an urgent need for standardisation in the automation approach. There are also many opportunities for automation of indirect labour functions, for example, in laboratory analysis and simple artificial intelligence loops with in-line metrology could substantially reduce indirect labour demand for production part approval.
He briefly outlined the benefits of digital-twin modelling and model-based systems-engineering methodologies to define the most effective ways of building products and optimising pricing.
Stepinski has recently been involved in the development of four different OEM PCB fabrication facilities in the U.S., manufacturing product technologies ranging from double-sided, through advanced aerospace HDI to semi-additive processing. He quoted some impressive cost-savings and production efficiencies, and he remarked that each of these facilities uses no more than 200 litres of water per day, with a headcount less than 25% of that of a typical PCB plant.Page 1 of 2
Suggested Items
SHENMAO Strengthens Semiconductor Capabilities with Acquisition of PMTC
07/10/2025 | SHENMAOSHENMAO America, Inc. has announced the acquisition of Profound Material Technology Co., Ltd. (PMTC), a premier Taiwan-based manufacturer of high-performance solder balls for semiconductor packaging.
KYZEN to Highlight Understencil and PCB Cleaners at SMTA Querétaro Expo and Tech Forum
07/09/2025 | KYZEN'KYZEN, the global leader in innovative environmentally responsible cleaning chemistries, will exhibit at the SMTA Querétaro Expo & Tech Forum, scheduled to take place Thursday, July 24, at Centro de Congresos y Teatro Metropolitano de Querétaro.
Driving Innovation: Direct Imaging vs. Conventional Exposure
07/01/2025 | Simon Khesin -- Column: Driving InnovationMy first camera used Kodak film. I even experimented with developing photos in the bathroom, though I usually dropped the film off at a Kodak center and received the prints two weeks later, only to discover that some images were out of focus or poorly framed. Today, every smartphone contains a high-quality camera capable of producing stunning images instantly.
Hands-On Demos Now Available for Apollo Seiko’s EF and AF Selective Soldering Lines
06/30/2025 | Apollo SeikoApollo Seiko, a leading innovator in soldering technology, is excited to spotlight its expanded lineup of EF and AF Series Selective Soldering Systems, now available for live demonstrations in its newly dedicated demo room.
Indium Corporation Expert to Present on Automotive and Industrial Solder Bonding Solutions at Global Electronics Association Workshop
06/26/2025 | IndiumIndium Corporation Principal Engineer, Advanced Materials, Andy Mackie, Ph.D., MSc, will deliver a technical presentation on innovative solder bonding solutions for automotive and industrial applications at the Global Electronics A