-
- News
- Books
Featured Books
- smt007 Magazine
Latest Issues
Current IssueSupply Chain Strategies
A successful brand is built on strong customer relationships—anchored by a well-orchestrated supply chain at its core. This month, we look at how managing your supply chain directly influences customer perception.
What's Your Sweet Spot?
Are you in a niche that’s growing or shrinking? Is it time to reassess and refocus? We spotlight companies thriving by redefining or reinforcing their niche. What are their insights?
Moving Forward With Confidence
In this issue, we focus on sales and quoting, workforce training, new IPC leadership in the U.S. and Canada, the effects of tariffs, CFX standards, and much more—all designed to provide perspective as you move through the cloud bank of today's shifting economic market.
- Articles
- Columns
- Links
- Media kit
||| MENU - smt007 Magazine
Estimated reading time: 6 minutes
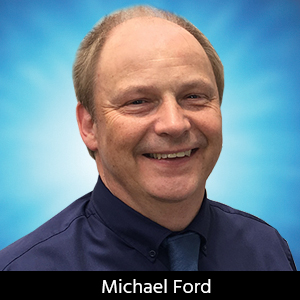
Smart Factory Insights: CFX IIoT Open-Source Hardware
The IPC Connected Factory Exchange standard (CFX) has triggered a rapid evolution in the way that industrial machines communicate in a secure, IIoT-based, plug and play environment. Attention now is on how CFX can be connected to older, “dumber” machines, bringing 100% visibility and control across the whole manufacturing floor, thereby avoiding the numerous technical and financial pitfalls historically experienced.
The Problem
Is it a realistic expectation that something new can be applied to things that are very old? Windows 11, for example, only works on personal computers that have a certain Trusted Platform hardware module, which, though available, had not been included on most personal computers until the requirement was announced. Almost every PC in use today is therefore destined to be scrapped or remain on legacy versions of Windows forever.
Though some would argue that this may create somewhat of a shock to the environment, PCs are far more replaceable than are industrial machines in manufacturing, where we see many cases of machines working well after 25 years or more of use. For sure, these machines are not the fastest or most accurate, but if they are fit for purpose, any machine that has been amortized costs only the floor-space on which it stands, the energy it uses, and the odd bit of maintenance, all of which can make it very cost effective. Are the potentials of modern, digital communication, visibility, and control enough to justify a replacement of a machine, or for the machine vendor to go back and develop CFX support as an option? In many cases, especially beyond the SMT manufacturing area, the answer is “no.”
Historically, as computers became increasingly used in manufacturing, we have seen valiant efforts where users try to extract useful information or establish a form of remote control with machines that are without the ability to communicate, often to the detriment of the machine, sometimes in catastrophic ways. The cost and risk of customized hardware and software, as well as the increasing need for middleware, all contribute to ensuring that communication in such cases has remained basic, inaccurate, and unreliable, as well as a risk to the performance of the machine.
The CFX standard is intended to replace all that. With the free open-source, community-supported Software Development Kit, CFX can be provided with a fraction of the development effort required for bespoke interfaces or the support of other standards. The CFX fully-defined single language for data ensures that middleware is not needed. The IPC qualification program ensures that, when buying new machines, manufacturers have the assurance that they can genuinely plug the machine into the CFX network, and the communication works. No coding needed, no customization, and no unexpected costs or delays. Machine vendors are increasingly embedding CFX into their new machines, and where capable, retrofitting it to recent models. This does leave however, a third category of machines, usually older models, where the native support of CFX is seen as ranging from uneconomic to technically impossible.
As such, MES and other smart, analytics-based solutions that use CFX data are left with gaps in their visibility and control, reducing the overall value potential. Existing mature solutions do offer alternative machine interfaces that fill in some of the gaps, which is effective in those cases where CFX will be provided by the vendor at some point. Looking at assembly beyond SMT, there is a far higher proportion of machines that have no communication ability or use a bespoke method without interoperability or compatibility. Where there is no way to extract useful data, custom third-party or in-house hardware solutions have been created and attached to the machine mechanics and electrical systems, that derive data from specific signals and actions. These have proven to be quite costly both to develop as a case-by-case customized item, and to purchase and maintain. They are usually developed in isolation from the machine vendor, with end-users left to bear the consequences of their actions.
The Solution
Applying the same principles to a hardware-based solution, as has been applied to software, the key “gotchas” of additional hardware/middleware solutions can be avoided. Creating open-source hardware means that predominantly off-the-shelf components can be assembled in a standard way to create a proven modular, flexible interface, driven internally by software based on the existing CFX SDK with additional firmware. This project has been started with a design based on the very popular, powerful, and affordable Raspberry Pi computer, with flexible, modular I/O connections that utilize the CAN-BUS interface. Small CAN modules can be located around a specific target machine, each equipped with sensor connections that derive information about the various machine operations. This can be achieved using non-invasive technologies, to not require any electrical connection to the machine other than through designated ports where available.
All intellectual property (IP) related to this solution, in terms of both hardware and software, is to be free and open-source, available for anyone to utilize, and for anyone to contribute to. This removes the duplication of effort designing the various modules that are needed to support a wide range of different machines that are out there. This is intended for use in different ways:
- Manufacturers can take the designs and quickly and reliably create CFX interfaces for equipment they own that has no native CFX vendor support.
- Machine vendors can take the designs to make their own approved CFX boxes in a cost-effective way, providing CFX solutions for those machines which cannot be natively supported with CFX software alone.
- Hardware/software solution creators can provide standards-based CFX machine connection services for a range of equipment.
Working together, machine vendors, solution providers, and their manufacturing customers work to ensure that CFX hardware-based endpoints are created that are consistent, interoperable, cost effective, posing no risk to the machine operation, and provide enough functionality through CFX to fill the gaps in the smart factory network. It is likely that such hardware-based interfaces could become fully CFX qualified, as sensors and designs are developed and built upon within the community. Collectable information potentially includes:
Basic
Sensors for:
- Active machine operation and status (e.g., light-tower sensor)
- Product arrival, movement, departure from the endpoint
- Material setup sensing
- Error conditions
Barcode reader:
- Product ID reading and confirmation for tracking and route enforcement
- Material verification
- Operator login
Machine port connection:
- RS-232, RS-485, Ethernet and SMEMA, Hermes connections
Isolated contacts for:
- Setting machine operation mode (start/stop)
Local terminal:
- Configuration and setup
Advanced
Sensors for:
- Predictive maintenance: temperature, vibration, energy patterns, specific mechanism cycle count
- Routing confirmation
Local terminal for:
- Online/offline mode recognition
- Debug and diagnostics
- Local machine learning
Inter-standards gateway:
- OPC-UA/MT-Connect/CAM-X, etc., conversion to CFX
The key to the success of this project is to gain the involvement of many influencers across the industry, including end-users, machine vendors and solution providers. There is already a small team involved, including experts from the Raspberry Pi design team, the UK’s Manufacturing Technology Centre (MTC), Aegis software, and of course, the IPC. The team is focused on creating an open standard set of hardware and software, driven by industry consensus, following the guidelines and principles of IPC standards development.
The fundamental value of this initiative is to open and enable Industry 4.0 digital manufacturing in areas that native CFX software alone cannot penetrate. Providing open source of hardware design, components, and software means that all potential applications of CFX can be considered, with pitfalls of cost and risk associated with bespoke design and deployment avoided. In particular, we would encourage machine vendors to see this as an opportunity to expand their Industry 4.0 footprint for older machines, with low risk and cost, but significant value to customers.
The outreach is to any company or individual that may be interested, to contact the team, to help with the initial hardware and software framework development, as well as the testing and trialing of prototypes to be used as showcases.
This column originally appeared in the March 2022 issue of SMT007 Magazine.
More Columns from Smart Factory Insights
Smart Factory Insights: Making Rework a Smart Business OpportunitySmart Factory Insights: The Sustainability Gold Rush
Smart Factory Insights: Today’s Manufacturing Jobs Require a New Skill Set
Smart Factory Insights: Compose Yourself, Mr. Ford
Smart Factory Insights: The Smart Business Case for Local PCB Manufacturing
Smart Factory Insights: Manufacturing Digital Twin—Spanners in the Works
Smart Factory Insights: Machines, People, and AI
Smart Factory Insights: Is Sustainability in Manufacturing a Benefit or Burden?