-
- News
- Books
Featured Books
- design007 Magazine
Latest Issues
Current IssueAll About That Route
Most designers favor manual routing, but today's interactive autorouters may be changing designers' minds by allowing users more direct control. In this issue, our expert contributors discuss a variety of manual and autorouting strategies.
Creating the Ideal Data Package
Why is it so difficult to create the ideal data package? Many of these simple errors can be alleviated by paying attention to detail—and knowing what issues to look out for. So, this month, our experts weigh in on the best practices for creating the ideal design data package for your design.
Designing Through the Noise
Our experts discuss the constantly evolving world of RF design, including the many tradeoffs, material considerations, and design tips and techniques that designers and design engineers need to know to succeed in this high-frequency realm.
- Articles
- Columns
- Links
- Media kit
||| MENU - design007 Magazine
Flexible Hybrid Electronics Design: Reducing Time to Market
March 23, 2022 | Sean Nachnani, NextFlexEstimated reading time: 2 minutes
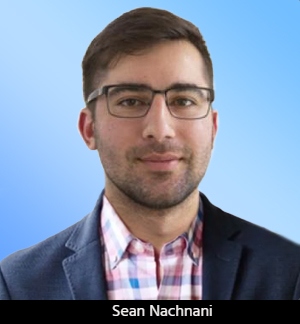
Emerging innovations in the flexible hybrid electronics (FHE) domain are enabling new applications across multiple industries due to their highly flexible structures and additive manufacturing processes. The smaller form factor, lighter weight, and conformal capabilities are ideal for IoT edge devices in health and fitness monitoring, military asset identification and tracking, automotive displays and sensors, aerospace radar, and soft robotics. Significant industry research led by NextFlex is optimizing the processes from design through manufacture for FHE products.
FHE devices provide ideal solutions for many of today’s conformal electronics needs. They allow for the implementation of SWaP-C (size, weight, power, and cost) improvements over their more traditional counterparts. Because these FHE devices bend and flex, however, the design process takes on more of an electromechanical approach. The final product application dictates certain features, such as static or dynamic bending, component placement, and material choices. Moreover, non-conventional flexible substrates and printed conductors require more extensive RF simulation and characterization, unique to each manufacturing process. Without proper tools or experience, these features can instead become detriments that lead to longer design cycles and increased costs. In this article, we will dive into the basics for FHE design and its requirements.
We will discuss the tools NextFlex has developed to simplify the design process, shortening development cycles and ultimately time to market, and we will share how NextFlex and its consortium members from across the ecosystem are coming together to create materials databases and process development kits (PDK). We will describe how the materials and process database, FHE PDKs, reference designs, and managed reuse blocks are part of a new design process vision that promises to streamline FHE design and manufacturing.
Finally, we’ll talk about how, through these efforts, new FHE reference designs are emerging, and how we’ll be using these along with other reference modules to come up with a truly plug-and-play approach to FHE that reduces the amount of time and effort it takes to manufacture and design FHEs.
The Many Considerations When Designing for FHE
When it comes to designing FHE, its application drives the design considerations for the device as both a mechanical and electronic system. These considerations involve an interrelated set of choices based on application, environment, materials, process, and encapsulation.
FHEs have a wide variety of applications; for example, medical bandages that monitor vital statistics, monitoring systems for helicopter rotor blades, security tokens embedded into uniforms, and armbands that warn when a toxic gas concentration is too high. A primary question is whether the application will require a static bend form factor, where we apply the device and it stays as is, or will it be in dynamic, bending, and flex situations.
Then we need to look at the environment where these devices will be deployed. Are they being deployed in the middle of the desert, out on rough seas, in a cockpit above 30,000 feet, or is it on its way to the International Space Station?
To read the entire article, which appeared in the March 2022 issue of Design007 Magazine, click here.
Suggested Items
S&K Aerospace Awarded Major Contract Under DLA Maritime Acquisition Advancement Program
07/02/2025 | BUSINESS WIRES&K Aerospace, LLC has been awarded a significant contract under the Defense Logistics Agency’s (DLA) Maritime Acquisition Advancement Program, managed by the U.S. Naval Supply Command - Weapon Systems Support (NAVSUP WSS) in Mechanicsburg, PA.
Green Circuits to Exhibit Full-Service Electronics Manufacturing Solutions at 2025 SMD Symposium
07/02/2025 | Green CircuitsGreen Circuits, a full-service Electronics Manufacturing Services (EMS) partner to leading OEMs, is pleased to announce its participation in the 2025 SMD Symposium, taking place August 5-7 at the Von Braun Center in Huntsville, Alabama.
I-Connect007 Editor’s Choice: Five Must-Reads for the Week
06/27/2025 | Nolan Johnson, I-Connect007While news outside our industry keeps our attention occupied, the big news inside the industry is the rechristening of IPC as the Global Electronics Association. My must-reads begins with Marcy LaRont’s exclusive and informative interview with Dr. John Mitchell, president and CEO of the Global Electronics Association. For designers, have we finally reached the point in time where autorouters will fulfill their potential?
Knocking Down the Bone Pile: Tin Whisker Mitigation in Aerospace Applications, Part 3
06/25/2025 | Nash Bell -- Column: Knocking Down the Bone PileTin whiskers are slender, hair-like metallic growths that can develop on the surface of tin-plated electronic components. Typically measuring a few micrometers in diameter and growing several millimeters in length, they form through an electrochemical process influenced by environmental factors such as temperature variations, mechanical or compressive stress, and the aging of solder alloys.
RTX, the Singapore Economic Development Board Sign MOU Outlining 10-year Growth Roadmap
06/20/2025 | RTXRTX and the Singapore Economic Development Board (EDB) have signed a Memorandum of Understanding (MoU) which outlines a 10-year roadmap to further long-term strategic collaboration in Singapore.