-
- News
- Books
Featured Books
- smt007 Magazine
Latest Issues
Current IssueWhat's Your Sweet Spot?
Are you in a niche that’s growing or shrinking? Is it time to reassess and refocus? We spotlight companies thriving by redefining or reinforcing their niche. What are their insights?
Moving Forward With Confidence
In this issue, we focus on sales and quoting, workforce training, new IPC leadership in the U.S. and Canada, the effects of tariffs, CFX standards, and much more—all designed to provide perspective as you move through the cloud bank of today's shifting economic market.
Intelligent Test and Inspection
Are you ready to explore the cutting-edge advancements shaping the electronics manufacturing industry? The May 2025 issue of SMT007 Magazine is packed with insights, innovations, and expert perspectives that you won’t want to miss.
- Articles
- Columns
- Links
- Media kit
||| MENU - smt007 Magazine
Estimated reading time: 7 minutes
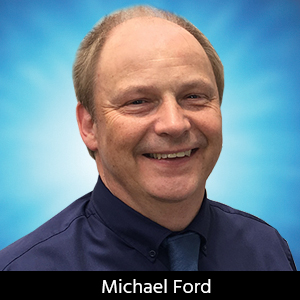
Smart Factory Insights: Has the Industry 4.0 Gold Rush Ended?
Industry 4.0, though only five years old, already has a checkered history. With buzzwords flying, existing technologies—re-branded as Industry 4.0 solutions—have been in demand. Manufacturers embarked on the Industry 4.0 “gold rush” to gather as much data as possible, and by whatever means necessary, to get those nuggets of smart manufacturing credibility. Today, the more mature approach of Industry 4.0 is emerging with consideration of a real return on investment (ROI) as well as sustainability. Taking advantage of such maturity may have been the smartest option all along.
The early pioneers of smart manufacturing have been doing a great job, with immense investment, sacrifice, and some compelling success stories, especially for enhanced automation of continuous manufacturing in Asia and agile manufacturing in Europe; this has demonstrated how far automation can be expanded when aided by smart software.
For these companies to “strike gold” was easy in some respects—assuming that there was enough investment available to meet the needs of bespoke solution development. This is because of the lobbying of machine vendors, utilization of middleware, and to financially assist custom solution providers to develop bespoke and specialist pieces of software, was based loosely on older industry standards and proprietary technologies. The downside of the approach was the inability to show a convincing ROI, especially considering the risks that had to be accepted with unplanned downtime as solutions needed to be adjusted and refined. The sustainability of such gold rush solutions has now become a real operational and financial burden as both requirements and technologies inexorably move forward.
The nice aspect about this early gold rush is that it has fractured the paradigm that manufacturing has been an area of short-sighted, tightly controlled investment. From the OEM perspective, manufacturing is a not-for-profit operation that simply converts raw materials into final products for sale with all associated profits accounted to the sales organization. There is extreme sensitivity in the manufacturing cost, as by the time the product has gone from the factory to the final point of purchase, the cost will have been marked up by 10, 100, or even 1,000 times (in extreme cases). An overspend of just a few cents on materials, energy, correction of defects, etc., can rapidly erode expectations for profitability, forcing up prices to a greater extent than many expect. Extreme costs of smart automation, therefore, have their effects if ROI is not rapidly achieved. The risk, however, is that in most gold rush examples, the effects are achieved slowly, a risk most manufacturers in the industry have been willing to accept.
As movies have recorded the history of squabbles and sacrifices made by those who rushed to be the few successful prospectors to make their fortunes in “them thar hills,” I wonder whether the pioneers of smart manufacturing will be regarded in the same way. Gold today represents a very reliable, predictable, and safe investment, making or preserving money in a more ordered and controlled way, which, other than the occasional heist or two, allows everyone to work together. For smart manufacturing, the same condition is emerging, with increasing interoperability of solutions and data, based on standards specifically developed within the industry for this purpose. Solutions that adopt these standards, and the core principles on which they are based, are the solutions that make smart Industry 4.0 viable, thus enabling it to deliver a very reliable, robust, and sustainable ROI.
The fundamental principles that are common to the best of these standards are the essential ingredients that make the use and adoption of smart manufacturing solutions cost effective and relatively risk-free. They are discussed below.
IoT/IIoT Messaging vs. Integration/Interfaces
The use of messaging enables different applications and solutions to become interoperable and complementary to each other without depending on licensing of shared proprietary code, and hence intellectual property (IP). In the gold rush, many companies expanded their solutions through code-sharing integration, either with different point-solutions that each provider had acquired, or by APIs with close partners. The costs for this development and ongoing dependency continue to be extremely high; it is duplicated repeatedly in slightly different ways for each customer.
The use of IIoT messaging, however, especially when defined by open standards, means that data is exchanged without any form of code dependency. Data can be freely exchanged between authorized parties and managed through standard security and access protocols. It should be noted that IIoT is very resilient to cybersecurity incidents, as there is no commonality of code or databases that would otherwise allow cross-contamination. Where an open standard is adopted, there is only one interface needed to connect everything, therefore avoiding costs of duplication and variation between use-cases.
Plug-and-play vs. Middleware
Though the use of IIoT allows for the open exchange of data, an equally important aspect of that data exchange is the mutual definition of the data content, that is, the language of communication. The principle of plug-and-play is to provide assurance that there is no need for the translation or conversion of data, which for the gold rush solutions proves extremely challenging and expensive to resolve. In the event of a slight change in any system behavior or specification, renewed development and testing could be required, which often results in lost operational time. The use of third-party technology to bridge the communication gap further complicates things as they are called in to fix sudden urgent issues for which they feel no responsibility—thus, justified premium rates to support. True plug-and-play requires an industry standard that aligns the meaning of all types of data into one language, such that there is no need for translation or conversion, bringing a massively reduced risk of failure throughout the life of any related solution.
Interoperable Specialization vs. Domination
Both software and hardware companies in the assembly manufacturing industry have their own areas of expertise and focus. In any factory, there will naturally be the need to use “the best tool for the job,” with overall solutions made up from many different vendors and each selected for their specific capabilities to perform in their required roles. The attempt by larger companies to seek domination in this environment, which allows them to provide wider solutions extending far beyond their core competence, is a far weaker and unsustainable solution than allowing individual hardware and software solution providers working together in an interoperable environment. Solution vendors who commit to providing everything that is needed are often having to develop bespoke solutions that are specific to each customer to fill in the gaps between their current capabilities and customer expectation. The gold rush pioneers have been caught out by this in many cases, an issue which is rarely satisfactorily resolved, and in fact increases in scope as manufacturing requirements and solution technologies change.
To many, explanations of IPC’s Connected Factory Exchange (CFX) standard may appear to be “just another standard” with which to exchange information around the factory, but when broken down into its fundamental values it is an excellent example of how it is becoming a complete game-changer. It is establishing the way in which all companies can now take a very much less expensive and risky path toward smart manufacturing. Hardware vendors that take their value to their customers seriously are embracing CFX and other initiatives that promote interoperability in the digital factory, with the forward-thinking software vendors also learning to do the same. Each provides a complementary value.
Is the industry yet in the situation that smart manufacturing is available at a low cost and risk to the operation? It is definitely on the way. There is still work to do to see qualification of all machine communications against the IPC-CFX standard, but the number is increasing and accelerating with time. Other standards, such as the IPC Digital Twin, published at the end of 2020, are also poised to bring another level of interoperability throughout the industry, this time related to the secure exchange of data at a system level between previously difficult-to-bridge silos.
The Industry 4.0 gold rush is effectively over once interoperability is established. Smart Industry 4.0 manufacturing is now at a “Goldilocks moment.” Rather than feeling the cost of data acquisition, operations are feeling the benefits from the use of such data. Value is created through the contextualization of collected information and relating operations together with production configurations, product design and BOM information, materials and tooling data—the holistic analysis of which detects and measures variation, identifies potential defects, and triggers actions and alerts that improve throughput, on-time delivery, quality, and productivity.
For those who want to differentiate themselves to gain competitive advantage, it can be done today with minimal cost and risk as compared to the gold rush days of Industry 4.0, if you are careful about the hardware and software tools that you select; those IPC qualified solutions that provide IIoT-based, plug-and-play exchange of data. Today is when the really smart people invest in Industry 4.0. Is that you?
This column originally appeared in the April 2022 issue of SMT007 Magazine.
More Columns from Smart Factory Insights
Smart Factory Insights: Making Rework a Smart Business OpportunitySmart Factory Insights: The Sustainability Gold Rush
Smart Factory Insights: Today’s Manufacturing Jobs Require a New Skill Set
Smart Factory Insights: Compose Yourself, Mr. Ford
Smart Factory Insights: The Smart Business Case for Local PCB Manufacturing
Smart Factory Insights: Manufacturing Digital Twin—Spanners in the Works
Smart Factory Insights: Machines, People, and AI
Smart Factory Insights: Is Sustainability in Manufacturing a Benefit or Burden?