-
- News
- Books
Featured Books
- design007 Magazine
Latest Issues
Current IssueAll About That Route
Most designers favor manual routing, but today's interactive autorouters may be changing designers' minds by allowing users more direct control. In this issue, our expert contributors discuss a variety of manual and autorouting strategies.
Creating the Ideal Data Package
Why is it so difficult to create the ideal data package? Many of these simple errors can be alleviated by paying attention to detail—and knowing what issues to look out for. So, this month, our experts weigh in on the best practices for creating the ideal design data package for your design.
Designing Through the Noise
Our experts discuss the constantly evolving world of RF design, including the many tradeoffs, material considerations, and design tips and techniques that designers and design engineers need to know to succeed in this high-frequency realm.
- Articles
- Columns
- Links
- Media kit
||| MENU - design007 Magazine
AltiumLive 2022 - Vince Mazur’s Supply Chain Advice: Always Have Alternatives
April 11, 2022 | Andy Shaughnessy, Design007 MagazineEstimated reading time: 6 minutes
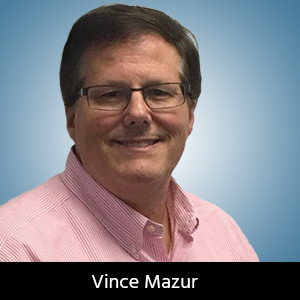
I had the chance to speak with Vince Mazur, a technical marketing engineer at Altium, about his AltiumLive presentation, “Avoiding Supply Chain Issues with Variants and Live Part Choices,” which is now available online. Vince discussed some of the high points of his talk, including the need for designers to pay closer attention to the supply chain than ever before, and to always have an alternative part or two as backup—just in case.
Andy Shaughnessy: How are you, Vince? Long time, no see.
Vince Mazur: Hi, Andy. I’m doing well.
Shaughnessy: Why don’t you start off by telling us about your AltiumLive presentation?
Mazur: I’ll quickly say that a variant is a variation of a design, not to be confused with the COVID variants that we keep hearing about these days. First, I reviewed electronic part supply chain fundamentals. For some of the audience, this might be new. Next, I talked about product change notices and product discontinuance notices. I then talked about some of the environmental compliance issues, the differences between, say, a manufacturer part number and a supplier part number—just some fundamentals that might fill in the gaps for designers.
Then, I transitioned into more of a pre-layout design type of strategy by discussing how design architecture impacts the ability to source components. I offered some tips that can insulate designs from sourcing issues from the start. I moved into a finer grain level of abstraction, if you will, and spoke about some of the things that you can do early, such as planning for critical blocks and components.
Again, if you know you’re going to have a challenge or you know you’re exposed, and you’ve only got one source for a part that’s absolutely key for your design, you’re just going to be in a bind. And, by the way, designers were exposed to these challenges 10 years ago. Nothing has changed in this area, except for today’s increased probability of downside risk. I outlined some of the ways that you can avoid these challenges.
I also discussed tactics and tips on addressing today’s part sourcing challenges in designs that are either ready to go to manufacturing, or are already in manufacturing. I demonstrated how the Altium tools’ capabilities assist in overcoming these headaches.
Shaughnessy: Basically, designers have to get their supply chain issues straight early in the process, so that they’re not surprised at the last minute.
Mazur: Absolutely! There are so many different quotes along these lines. “Failure to plan is planning to fail,” comes to mind. If you know you’re going into the mountains in the depths of winter, you have to have some preparation. If you know that you’re going into a tough supply chain environment, and that supply chains are being impacted not just because of the current dilemma, but because of issues that started several years ago, designers will need to plan. We’ve got more people doing electronics design than ever in the history of engineering. They all need parts. And, I can say, as somebody who is very familiar with the small electronics OEM that my wife runs, we have been bumped on some of the parts unbelievably.
What I’ve found is that when you order parts, you don’t pick a number like you do at the meat counter. When that number comes up, you’re not guaranteed. They’re bumping us likely because there are bigger accounts that need those parts, you’ve got to be really careful how you design right now. And literally there is an opportunity for companies that do it right to gain a competitive advantage, in that they’re able to deliver their product in volume where their competition, who may even have a slightly better feature set, cannot.
It's always been a challenge, but it really is now. And, for instance, I did a webinar the other day, and one of the attendees said, “We’ve had to spin our board five different times to compensate for component issues.” And you know what that is? That’s a bunch of time. It’s a bunch of validation. That’s tough. And at Altium we’re trying to address some of the critical aspects relating to the supply chain. And, the key is just like everything else, plan ahead. It’s better to have it and not need it, than to need it and not have it. And it’s that way with a lot of things.
It’s unfortunate, but even people who get advanced warning of hurricanes sometimes run out of water. And the other thing that I think is happening is that, as designers, we were usually not the ones who traditionally had to worry about sourcing parts. We just designed. Today, you must be aware of the supply chain. And again, to borrow a phrase from Homeland Security relating to another significant activity, “if you see something, say something.” And if you’re at the beginning of a design process and you’re an engineer, you’re a technician, or you’re a board designer, if you see a problem with that bill of materials, you need to tell somebody as early as possible.
So that’s the theme of my AltiumLive presentation. Fortunately, Altium provides a lot of high value capability. One of the keys is to have an early warning system that lets you know you have a component issue. And the nice thing about Altium is supply chain intelligence is intrinsic to the application—It’s built in. You go into the properties panel. You see an indication if that part that you’ve selected has an issue. When you go into your bill of materials, you’ll see any component red flags. If you’re selecting a component from your library and there’s a current stock issue, you’re going to see it.
Shaughnessy: What are some of the lead times you’re seeing now? Is it still 50 weeks for a lot of these parts?
Mazur: Yes. I ordered SPI EEPROM chips in May of 2021, and they made it sound like they would ship them later that same month. Then it moved to July. Then it moved to December. I think it’s out until 2023 now. Fortunately, if you offer 512K of storage in your product, you can always offer 256K and still ship your product, with a derated specification. This was the backup plan, but as it turned out, we were able to find a substitute for the 512K part.
Shaughnessy: What do you hope the attendees take away from your presentation?
Mazur: Well, I hope that they realize that today’s supply chain and the way they design impacts the sourcing of parts, and that in some cases, when their goal is to get a product to market, it’s not necessarily time to come up with the most eloquent design. Eloquent designs are great. Very efficient designs are great, but they’re not great if you can’t manufacture them in volume. As designers, we need to strike a practical balance.
Sometimes you may be better off taking a block of circuitry, implemented with a single-sourced, purchased chip, and consider designing that block as discrete circuitry, because that would give you the ability to substitute out easily. That’s one of the nice things about transistor design, as an example.
So just to summarize, the answer to your question is that I hope I was able to broaden their awareness to realize the impact that design and part choices have on their ability to get their products manufactured. Another aspect is if you’re choosing popular parts, that’s like choosing a popular theme park. It’s not always fun to go to—It’s packed. And so sometimes you’ve got to think outside the box, design with volume in mind and have alternatives. Have several destinations rather than a focus on one.
Shaughnessy: That’s a good way to look at it. Thanks for your time, Vince.
Mazur: Thank you, Andy.
Watch Vince Mazur's presentation Avoiding Supply Chain Issues with Variants & Live BOM Part Choices below.
Suggested Items
DownStream Acquisition Fits Siemens’ ‘Left-Shift’ Model
06/26/2025 | Andy Shaughnessy, I-Connect007I recently spoke to DownStream Technologies founder Joe Clark about the company’s acquisition by Siemens. We were later joined by A.J. Incorvaia, Siemens’ senior VP of electronic board systems. Joe discussed how he, Rick Almeida, and Ken Tepper launched the company in the months after 9/11 and how the acquisition came about. A.J. provides some background on the acquisition and explains why the companies’ tools are complementary.
Elementary Mr. Watson: Retro Routers vs. Modern Boards—The Silent Struggle on Your Screen
06/26/2025 | John Watson -- Column: Elementary, Mr. WatsonThere's a story about a young woman preparing a holiday ham. Before putting it in the pan, she cuts off the ends. When asked why, she shrugs and says, "That's how my mom always did it." She asks her mother, who gives the same answer. Eventually, the question reaches Grandma, who laughs and says, "Oh, I only cut the ends off because my pan was too small." This story is a powerful analogy for how many PCB designers approach routing today.
Connect the Dots: The Future of PCB Design and Manufacturing
07/02/2025 | Matt Stevenson -- Column: Connect the DotsFor some time, I have been discussing the increasing complexity of PCBs and how designers can address the constantly evolving design requirements associated with them. My book, "The Printed Circuit Designer’s Guide to… Designing for Reality," details best practices for creating manufacturable boards in a modern production environment.
Siemens Turbocharges Semiconductor and PCB Design Portfolio with Generative and Agentic AI
06/24/2025 | SiemensAt the 2025 Design Automation Conference, Siemens Digital Industries Software today unveiled its AI-enhanced toolset for the EDA design flow.
Cadence AI Autorouter May Transform the Landscape
06/19/2025 | Andy Shaughnessy, Design007 MagazinePatrick Davis, product management director with Cadence Design Systems, discusses advancements in autorouting technology, including AI. He emphasizes a holistic approach that enhances placement and power distribution before routing. He points out that younger engineers seem more likely to embrace autorouting, while the veteran designers are still wary of giving up too much control. Will AI help autorouters finally gain industry-wide acceptance?