-
- News
- Books
Featured Books
- design007 Magazine
Latest Issues
Current IssueProper Floor Planning
Floor planning decisions can make or break performance, manufacturability, and timelines. This month’s contributors weigh in with their best practices for proper floor planning and specific strategies to get it right.
Showing Some Constraint
A strong design constraint strategy carefully balances a wide range of electrical and manufacturing trade-offs. This month, we explore the key requirements, common challenges, and best practices behind building an effective constraint strategy.
All About That Route
Most designers favor manual routing, but today's interactive autorouters may be changing designers' minds by allowing users more direct control. In this issue, our expert contributors discuss a variety of manual and autorouting strategies.
- Articles
- Columns
- Links
- Media kit
||| MENU - design007 Magazine
Estimated reading time: 3 minutes
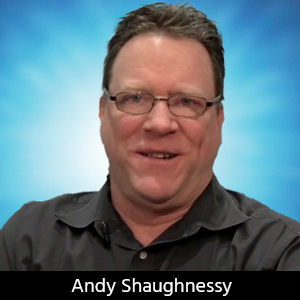
The Shaughnessy Report: Upskilling Staff Is Your Best Option
For the past few years, industry analysts have been talking about the need for fabricators to “upskill” their employees to be ready for the technologies of tomorrow. The Smart factory and Industry 4.0—not to mention the ramping-up of AI—are just a few reasons that your staff really needs continuing education throughout their careers.
But upskilling is more than a fancy-sounding idea. In today’s labor market, fabrication management may not have any other alternatives than to make the best of the employees they have right now. That, and pray that none of the subject matter experts retire in the meantime.
(If I owned a board shop right now, I’d set up putt-putt golf in one corner of the shop floor to satiate the 63-year-old staffers who are looking forward to spending life on the links. And make every day Hawaiian Shirt Day. But I digress.)
It’s certainly a good time to be adding tools to your toolbox of skills. As the Smart factory and Industry 4.0 lead the drive to replace more humans with technology, the need for humans who are trained to manage AI-optimized systems will increase exponentially. Much of the software used to fabricate and assemble PCBs contains AI or machine learning—it just operates in the background, learning as it works.
But what’s the best way to upskill your employees? Several managers we spoke with said they don’t have time to take staff off the shop floor for training sessions. Your best bet is to incentivize employees to continue their education and training on their own time. But how do you make that happen?
For fab managers, upskilling is almost your only good option. We’re still feeling the effects of the brain drain of the past few years; many who were close to retirement pulled the pin during the pandemic. As 10,000 Americans turn 65 each day over the next 15 years, this is becoming our reality. More shop managers are finding themselves with a lack of subject matter experts in-house, and a tight labor market isn’t helping them fill the gaps.
So, some managers have adopted the mantra, "If you can't find them, grow them." They’re sending their current staff to be upskilled, whether at conferences, trade shows, or industry training centers. With three or four open positions for every job-seeking engineer, training your current workforce to be the best they can be is just good business.
In this issue, our contributors discuss the skill sets they see lacking in the fab community, and some strategies for training and educating employees to fill these gaps. We cover the challenging topic of the skills gaps and upskilling. We will bring insight into some of the common gap areas and methods to fill in those gaps.
We started by talking with IPC’s David Hernandez, who outlines some of the organization’s educational plans, including a curriculum approach that can be tailored to a company’s needs. We also asked three Sunstone Circuits managers to share their thoughts on upskilling for tomorrow’s fabricators. For his monthly column, IPC President and CEO John Mitchell shares valuable insight into the workforce challenges, and columnist Todd Kolmodin shares tips on how to best optimize your training time.
Our new columnist Hannah Nelson explains how students can be better prepared for an internship in this industry, and Editor Nolan Johnson discusses some of the lessons he learned from Analyzing Performance Problems, a book authored by Robert Mager and Peter Pipe in 1970. Barry Matties brings us interviews with two representatives from the FIRST robotics programs in Oregon and Washington, who share their enthusiasm for the program and the need to attract more students into STEM careers. We also have columns by our regular contributors Christopher Bonsell, Steve Williams, and Happy Holden.
There’s never been more opportunity than there is today for your employees to become valuable than there is today. But you’ll have to support them by giving them time to continue their education, and they’ll have to step outside of their comfort zone to learn about new processes and technologies.
Don’t forget: You’re in this together with your employees, but they have more options than you do. While that may feel like a sobering reality, it’s about perspective. Taking the opportunity to upskill means everybody wins.
This column originally appeared in the April 2022 issue of PCB007 Magazine.
More Columns from The Shaughnessy Report
The Shaughnessy Report: A Plan for Floor PlanningThe Shaughnessy Report: Showing Some Constraint
The Shaughnessy Report: Planning Your Best Route
The Shaughnessy Report: Solving the Data Package Puzzle
The Shaughnessy Report: Always With the Negative Waves
The Shaughnessy Report: Breaking Down the Language Barrier
The Shaughnessy Report: Back to the Future
The Shaughnessy Report: The Designer of Tomorrow