-
- News
- Books
Featured Books
- smt007 Magazine
Latest Issues
Current IssueSupply Chain Strategies
A successful brand is built on strong customer relationships—anchored by a well-orchestrated supply chain at its core. This month, we look at how managing your supply chain directly influences customer perception.
What's Your Sweet Spot?
Are you in a niche that’s growing or shrinking? Is it time to reassess and refocus? We spotlight companies thriving by redefining or reinforcing their niche. What are their insights?
Moving Forward With Confidence
In this issue, we focus on sales and quoting, workforce training, new IPC leadership in the U.S. and Canada, the effects of tariffs, CFX standards, and much more—all designed to provide perspective as you move through the cloud bank of today's shifting economic market.
- Articles
- Columns
- Links
- Media kit
||| MENU - smt007 Magazine
Estimated reading time: 4 minutes
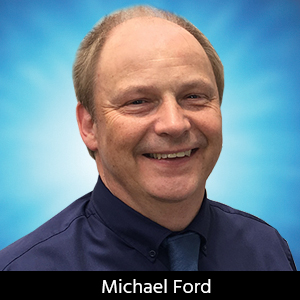
Smart Factory Insights: Fractional Materials and High-Mix Manufacturing
We used to discuss manufacturing paradigms in terms of high- or low-mix, coupled with high- or low-volume, with many shades of grey in between. Now, we have a new dimension, that of high-volatility, as key dependencies on labour, materials, and logistics contribute challenges to production, which in turn, is subject to the volatility of customer demand. More than ever, material management is either the key enabler for business success, or your nemesis in not being able to achieve the necessary recovery plan if not thought out properly.
One unique aspect of electronics manufacturing is that there are simply too many materials to individually manage. Obviously, we use carriers for those materials, whether collected on reels, in trays, bags, boxes, or other containers. These are used not only for discrete components, but also for materials measured using fractions of their initial content, such as volumes of liquids for dispensing, coating, cleaning, and solder paste, as well as lengths of wires and cables. For mass production, carriers are very convenient for simple logistics, but as you look deeper at other production paradigms, these carriers introduce a very complex logistical challenge.
Other than high-volume manufacturing, production often does not consume the entire quantity of materials within each carrier, leaving partly-used carriers of remaining materials, and which require specialist management. This very simple fact greatly contributed to productivity levels decreasing from 90% with high-volume production, to some extreme, high-mix cases of only 10%. Whatever benefits have come from mechanically automated production (the dream of the third industrial revolution) have become the proverbial nightmare.
As the market has slowly transitioned from high-volume to high-mix, manufacturing has become gradually accustomed to tweaking existing operations and practices. It creates continuous strain but never breaks. Today’s sudden increased volatility in the market takes us beyond that point. As many manufacturers face mounting questions daily of what can or should be built, the least concern should be how—but that is not the case. Consider the increased overhead on what has become routine decision-making in terms of material management:
- Which carriers of material are the most suitable carriers to use?
- What quantity/length/volume of material is remaining, and will it satisfy the needs of the work order without lost time of additional replenishment?
- How accurate is that assessment, bearing in mind the many opportunities for spoilage over the times that this material carrier has been used? There are cases, for example, where a reel of specialized chips was used once a week over a period of several months, each time using a very small number of pieces. Each time the material was set up, spoilage occurred, resulting in around 30% true spoilage rates. It is very challenging to find out that suddenly there are no remaining materials for the next few months of committed production, and nothing on order in the supply chain.
- How “old” are the materials, bearing in mind the many transportations and changing environments that they have been put through as part of their unused collective whilst in their carrier? Moving between environments with different humidity and temperatures causes issues with many types of material.
- Where are the carriers? Most often, partly-used carriers of materials remain in manufacturing between work orders. These are being managed, more often than not, by a team people who are working different shifts, moving things around, and using materials for other work orders. It is extremely difficult to keep track of specific partly-used material carriers, especially with most ERP and MES solutions not keeping track of such materials to this degree of granularity.
These used to be minor, infrequent issues, mainly occurring in between very long production runs, and therefore deemed insignificant. Today, these issues occur frequently, even daily. The management of these issues impacts our decision-making process in terms of deciding what products can be made, and affects the quality with which those products are made. Work that has been absorbed in outdated practices and procedures is human-augmented material management: those few people who could be relied on to find and make things happen. With the current levels of volatility, this coping mechanism is no longer a viable model.
This situation highlights the need and value of digital transformation. Having a modern MES that understands every idiosyncrasy of the complexities of material management provides the software-based automation that is required. Bear in mind that there are many other complexities involved, such as the management of moisture-sensitive devices and end-of-life materials, as well as multiple part-numbers, owners and statuses for identical materials belonging to different customers in, for example, the EMS environment. These things are currently being managed, and are dependent upon, in most cases, by an extremely undervalued human resource, or by artificially imposed, complex inefficient restrictions and practices that have invisibly accumulated over time.
Digital transformation may appear to be a big step to take at a time when other challenges are pushing the limits of what can be coped with, but this must be seen from the point of view as the compelling need to change, rather than something that is put off until things settle down. The market does not appear to be going back to what it was any time soon, and whenever that is, the recovery opportunity may well have passed by for those who continue to wait.
This column originally appeared in the May 2022 issue of SMT007 Magazine.
More Columns from Smart Factory Insights
Smart Factory Insights: Making Rework a Smart Business OpportunitySmart Factory Insights: The Sustainability Gold Rush
Smart Factory Insights: Today’s Manufacturing Jobs Require a New Skill Set
Smart Factory Insights: Compose Yourself, Mr. Ford
Smart Factory Insights: The Smart Business Case for Local PCB Manufacturing
Smart Factory Insights: Manufacturing Digital Twin—Spanners in the Works
Smart Factory Insights: Machines, People, and AI
Smart Factory Insights: Is Sustainability in Manufacturing a Benefit or Burden?