-
- News
- Books
Featured Books
- design007 Magazine
Latest Issues
Current IssueAll About That Route
Most designers favor manual routing, but today's interactive autorouters may be changing designers' minds by allowing users more direct control. In this issue, our expert contributors discuss a variety of manual and autorouting strategies.
Creating the Ideal Data Package
Why is it so difficult to create the ideal data package? Many of these simple errors can be alleviated by paying attention to detail—and knowing what issues to look out for. So, this month, our experts weigh in on the best practices for creating the ideal design data package for your design.
Designing Through the Noise
Our experts discuss the constantly evolving world of RF design, including the many tradeoffs, material considerations, and design tips and techniques that designers and design engineers need to know to succeed in this high-frequency realm.
- Articles
- Columns
- Links
- Media kit
||| MENU - design007 Magazine
Pulsonix Collision Avoidance to Bring Mechanical Capabilities Into ECAD
May 19, 2022 | I-Connect007 Editorial TeamEstimated reading time: 12 minutes
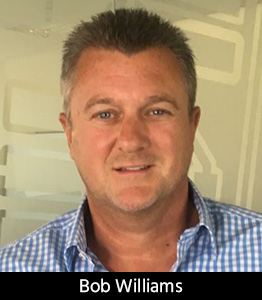
The I-Connect Editorial Team recently spoke with Bob Williams, managing director of Pulsonix. He discussed some of the new features in the upcoming version of the Pulsonix PCB design tool, Version 12, including collision avoidance and other 3D options that allow certain MCAD functions within the ECAD environment.
Andy Shaughnessy: Why don’t you give us the basics on this collision avoidance in the new Pulsonix tool? It sounds pretty cool. A lot of us have collision avoidance in our cars.
Bob Williams: Sure. We’ve written another extension to our 3D interface. Within our 3D co-design interface in Pulsonix you can add STEP models to your board, you can also include enclosures or cases onto your board, and then you can pass that configuration into the 3D environment that is included with Pulsonix. In this newest version of Pulsonix, you can put reference markers onto the board for use in the 3D editor. You can have multiple boards and by using the reference markers, you can actually transpose the board or boards once inside the 3D environment. You can run inter-board clashes and inter-component clashes and clashes within the enclosures between the multiple boards in their ‘built’ orientations. This MCAD simulation enables the build status of the boards to be defined and checked up front. It’s a huge step in bringing the design process forward.
Shaughnessy: Was this something that the customers had asked you for?
Williams: Oh, yes, absolutely. It’s like the next step on from the visualization and clash detection within the actual enclosure itself. Users want to put multiple boards together; mother-daughter boards or multiple boards within the actual case itself, and definitively see if they clash before they pass the structure into the mechanical environment.
Nolan Johnson Bob, for readers who might not be that informed on the jargon in this context, what is a clash?
Williams: It would be a physical item clashing with another item. Let’s say you have two large clusters; obviously, you can’t put them directly on top of each other because they will violate each other’s real estate, if you like. So, it’s the actual physical environment that they occupy.
Also, it’s a bit like if you cut Manhattan in half and then folded one half onto the other. It wouldn’t fit because you’ve got the tall buildings clashing with other tall buildings. But if you were smart enough to move it around, the buildings wouldn’t actually clash, and they would fit very nicely within each other. That’s basically what we are trying to do. We’re just trying to free up physical space so they can drop inside each other. Imagine two large capacitors on two different boards and then bringing the boards together. The capacitors would need to avoid each other, or not “clash.”
Johnson: All right. So that’s really what you’re trying to accomplish—finding the topology in which they can fit together without trying to occupy the same space.
Williams: Yes, that’s right. And once you’re in our 3D environment, when you see clashes, you can physically move the components. This makes the changes dynamically in the PCB itself; components are moved in real time. You can move and line up components, and this is before you’ve sent it to the mechanical environment. Getting correct component positioning and solving clashing issues earlier in the design process provides enormous time savings.
Johnson: Well, it almost sounds to me like this would be a great thing to be doing at component placement. Don’t invest in putting down the traces until you’ve got all your clashes worked out.
Williams: Exactly that, and it also means because you’re doing it in the PCB environment, you’re potentially not using another person who has mechanical experience so you’re not taking up mechanical CAD time. You’re doing all this within our own 3D environment. It’s all built into the Pulsonix toolset free of charge as part of the standard product.
Johnson: Regarding clashes, you’re talking about taking a mechanical look at what you’re doing in PCB design. That includes enclosures and other boards.
Williams: Yes, very much so. This is an important facet to modern PCB design.
Johnson: That’s bringing in some interesting data. You’ve got to make sure that you’ve got some work going on in the other parts in order to make sure that you can do this.
Williams: That’s right, the most important point to recognize is that in Pulsonix it is a very easy set up as well. Once you’ve got your regular components and footprints (decals) defined in the library, then you can then take a STEP model from the internet and position it on the footprint. That’s all you need to do. The definition and placement of enclosures is even easier and is done with the aid of a visual positioning tool. When the user passes this structure into 3D it is simply one command, and then it then can be visualized.
Shaughnessy: You’re bringing a good chunk of MCAD into the ECAD environment, basically.
Williams: Yes. Some of the most important parts, because obviously, you’re freeing up your expensive MCAD system (and person), and you’re likely a person who has the knowledge to make the critical placement of components within this structure. The way we see it, a lot of users will have either ECAD or MCAD experience, so you can do quite a lot the work up front with very little MCAD experience and just visibility on the PCB design in-hand. Most the time, the PCB designer will know where components must be placed with respect to each other and how they interact. They understand the PCB design tool, and we’ve made it very easy for them to get a mechanical perspective on the boards.
Johnson: All right. This is going to require 3D data for the packages—not just footprints for placement and symbols for the schematic, but now you really are looking for the 3D package model.
Williams: Yes, and they’re really easy to find on the internet through different resources. Most of the manufacturers make the STEP models available. They now provide a footprint symbol for a part as well as the STEP model for 3D design. It’s like another entity toward their offering. The content creators such as PCB libraries, SnapEDA, SamacSys, and Ultra Librarian all generally supply STEP models too.
Johnson: Are the suppliers, those content creators, becoming more important to the design process, and to you?
Williams: It depends upon who you talk to. They’re important for vendors like us who actually supply the design tool because it means we don’t have to specialize in creating content as well. They’re usually independent, not always, but they’re generally semi-independent of the vendor themselves. It’s quite an important facet for us because they have close connections to the component manufacturers and the component suppliers. It definitely makes life easier for everyone.
Johnson: It doesn’t seem like it’s very far away from dealing with mechanical clashes and mechanical models to starting to look at thermal analysis as well.
Williams: Yes. That’s certainly an issue for some users, but not everybody has that requirement. Generally speaking, it’s a very low percentage of users that actually need thermal analysis. Mostly, it’s either very high-speed boards, high-power boards, boards that are in a very confined area, or boards that are temperamental to heat changes and variations.
Johnson: It sounds like your 3D solution and new additions will be well received by users. What else does Version 12 have for Pulsonix?
Williams: The new additions to our 3D has been one of our key areas, but we’ve also rewritten the product to be 64-bit. We’re opening up the 64-bit environment for the extra memory address space that we can use. We can utilize this for large designs, it makes a big difference in some of the larger designs we’re seeing now, where you have, say, 24 layers, many thousands of components and connections, complex split power planes and more. We’ve also seen boards with 90,000 microvias!
Pulsonix is very efficient with its design size, but it starts pushing the boundaries of memory space allocation within your PC. So, 64-bit opens that up for us. Basically, that means it’s unlimited. Within the rewrite, we’ve also added additional multi-threading capabilities. Wherever possible, we’ve used multi-threading for other features within the product, this has. really created a huge speed-up. We’ve seen designs 60% faster on processing using multi-threading. We can utilize multicore technology where it’s available. I mean, not everything lends itself to multi-threading, but quite a few of the important processes do, like copper pouring for split planes, net optimization (to find shorter paths) and design rules checking (DRC).
Johnson: When you can use it, it helps out a lot.
Williams: Yes. For instance, it can optimize all the ground nets in one thread, and all the other nets in another thread. Because obviously, power and ground nets on a big board can be 20,000 connections, this speed increase makes a difference. We’re seeing significant speed-ups with this.
Johnson: How’s the user acceptance for the new features?
Williams: Really good. For our biggest customers, the 64-bit has made a big difference, along with the multi-threading technology. We’ve also added the dark UI; the dark mode interface. Users who are using the software professionally, constantly, and intensely really notice the difference because it causes less strain on the eyes and fatigue.
Johnson: The dark mode is my friend.
Williams: Some users hate dark mode on their application; not just Pulsonix but all apps. It seems that graduates coming in from university love it as they’re used to it, but I understand it’s not for everyone. It’s easily switchable in Pulsonix so users can choose. In terms of user comfort, it’s a huge feature for us and the benefit it gives users. The new SVG based icon set we created for the dark mode compliment this feature nicely too and is easily readable. While we were developing these, we recreated the alternative icon set for use in “light” mode.
Shaughnessy: I know you have some new ways of setting up rules for things like differential pairs. Tell us about that.
Williams: Yes, we have some additional features within differential pairs, which gives a better precision within the pair topology; this is the spacing when pairs change layers and tracks pair away from the via pattern. Generally speaking, the higher the speed of the design, the more precision you need around via pattern placement and the topology around where differential pairs are changing layers and how they appeared to interact track on track. We’ve done a lot of development work with that and really tightened up the precision.
The new rule sets also include rules for loop antenna, return paths, an anti-pad rule for planes, stub routing length, teardrop length and track mitering lengths used for high-speed design where behavior needs to be specifically defined and flag potential errors when the rule is violated. Additional rules define and flag issues for DFM like SMD to corner, SMD to plane, copper sliver, and sliver length. Once the rule has been defined, you’ve got to be able to detect them. So, we’ve done quite a lot of work within the detection algorithm as well. Our rule sets are powerful and included in the standard product. We’ve got a lot of rules built in that the user can set up if they want to, but we can also detect them in our DRC checking routines.
Shaughnessy: Yes. This does a lot for its price point.
Williams: I mean, Pulsonix is certainly good on price point, and it has a very high feature set for the money, plus we’ve a very large set of input filters. We can import virtually any other system in one way or another, and accurately. We based our import filters around quality and accuracy so that users have maximum confidence in the imported design data (and libraries) having the integrity of their original design. This is very important and has been proven in the field.
You know, I would say most of the import filters have about 99% accuracy. There are very small items that don’t look exactly as they were because of the way that the other tool defines it, such as text. But once you’re down to analysis of text, you don’t really care. Everything else is good and the integrity is there.
Shaughnessy: The last time that we spoke with you, you talked about expanding into North America. How is that going?
Williams: We’re certainly getting more recognition in the United States and it’s starting to turn into sales, but obviously one of the biggest problems is not attending shows and having feet on the street because of COVID, but generally speaking, COVID has hardly affected us. When we first started into the COVID pandemic and country lockdowns, we didn’t know whether it was going to make a difference, but it’s almost not affected us at all.
The only thing that has affected us was in running face-to-face demos in some regions, especially in the UK where the country is a lot smaller. In the UK, I would visit customers, whereas in the U.S., you are used to Zoom and Teams, but that’s a new culture for us in the UK and Europe. We’re getting there now, though.
Shaughnessy: You know, COVID is an equal opportunity stressor.
Williams: Yes, and because we’re global, in some countries it’s really affected us. For instance, I was supposed to visit the Philippines and do some training and set up a large university there, but it was canned because of their strict lockdown. We actually did the sale, but not the training. In Europe, one country is closed for business and another country opens up. It’s been going around in circles but seems to have settled down a bit now.
Shaughnessy: Where are most of your users right now? Is it still Europe primarily?
Williams: Yes, definitely Europe. Germany is a big market for us, with the UK, Italy, France, and the Netherlands being the main European countries for us too. We’ve seen some movement in Portugal, and primarily big names as well, which is good.
We’ve listed the core features that we’ve added for version 12, and we’ve added around 50 features as well. Obviously, the main effort was in 64-bit, multi-threading, and 3D. Those were the key items for us. We’re pretty happy with it.
Shaughnessy: So, what’s next?
Williams: The next release! Yes, we’ve got plenty of input from customers. We’ve got key customers who we work with, and because they’re so big, they help drive what we do, but they are representative of the market overall too, which is pretty healthy. But yes, we’ve got some pretty key things that we’re looking at next. We’re not going to be idle, that’s for sure.
Shaughnessy: Thanks for speaking with us, Bob.
Williams: Thank you as well, Andy. I hope we can get together in person soon.
Suggested Items
The Evolution of Picosecond Laser Drilling
06/19/2025 | Marcy LaRont, PCB007 MagazineIs it hard to imagine a single laser pulse reduced not only from nanoseconds to picoseconds in its pulse duration, but even to femtoseconds? Well, buckle up because it seems we are there. In this interview, Dr. Stefan Rung, technical director of laser machines at Schmoll Maschinen GmbH, traces the technology trajectory of the laser drill from the CO2 laser to cutting-edge picosecond and hybrid laser drilling systems, highlighting the benefits and limitations of each method, and demonstrating how laser innovations are shaping the future of PCB fabrication.
Day 2: More Cutting-edge Insights at the EIPC Summer Conference
06/18/2025 | Pete Starkey, I-Connect007The European Institute for the PCB Community (EIPC) summer conference took place this year in Edinburgh, Scotland, June 3-4. This is the third of three articles on the conference. The other two cover Day 1’s sessions and the opening keynote speech. Below is a recap of the second day’s sessions.
Day 1: Cutting Edge Insights at the EIPC Summer Conference
06/17/2025 | Pete Starkey, I-Connect007The European Institute for the PCB Community (EIPC) Summer Conference took place this year in Edinburgh, Scotland, June 3-4. This is the second of three articles on the conference. The other two cover the keynote speeches and Day 2 of the technical conference. Below is a recap of the first day’s sessions.
Preventing Surface Prep Defects and Ensuring Reliability
06/10/2025 | Marcy LaRont, PCB007 MagazineIn printed circuit board (PCB) fabrication, surface preparation is a critical process that ensures strong adhesion, reliable plating, and long-term product performance. Without proper surface treatment, manufacturers may encounter defects such as delamination, poor solder mask adhesion, and plating failures. This article examines key surface preparation techniques, common defects resulting from improper processes, and real-world case studies that illustrate best practices.
RF PCB Design Tips and Tricks
05/08/2025 | Cherie Litson, EPTAC MIT CID/CID+There are many great books, videos, and information online about designing PCBs for RF circuits. A few of my favorite RF sources are Hans Rosenberg, Stephen Chavez, and Rick Hartley, but there are many more. These PCB design engineers have a very good perspective on what it takes to take an RF design from schematic concept to PCB layout.