-
- News
- Books
Featured Books
- design007 Magazine
Latest Issues
Current IssueProper Floor Planning
Floor planning decisions can make or break performance, manufacturability, and timelines. This month’s contributors weigh in with their best practices for proper floor planning and specific strategies to get it right.
Showing Some Constraint
A strong design constraint strategy carefully balances a wide range of electrical and manufacturing trade-offs. This month, we explore the key requirements, common challenges, and best practices behind building an effective constraint strategy.
All About That Route
Most designers favor manual routing, but today's interactive autorouters may be changing designers' minds by allowing users more direct control. In this issue, our expert contributors discuss a variety of manual and autorouting strategies.
- Articles
- Columns
- Links
- Media kit
||| MENU - design007 Magazine
Estimated reading time: 4 minutes
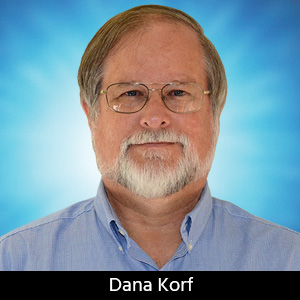
Dana on Data: DFM Issue Reduction—Company-specific PCB Acceptance Specifications
PCB data packages commonly generate fabricator DFM feedback questions that require resolution. Resolving these issues delays the manufacturing cycle time until the issues are resolved. There are many methods and techniques to reduce the DFM issues, such as working with the fabricator to review proposed stackup materials and impedance structures early in the design cycle. Another common method is to generate a company specific acceptance specification that provides requirements that are not covered in referenced IPC specifications and include negotiated DFM issue resolutions.
There are two generic sections in this document:
-
Referenced IPC specification modifications
-
Global approved deviation approvals
Let’s use the commonly referenced IPC-6012 “Qualification and Performance Specification for Rigid Printed Boards” specification as an example on where OEMs will modify the requirements to conform to their application.
IPC Specification Modifications
These company requirements will add, delete, or modify information contained in specific sections. Here are a few examples:
Section 1.2.1 Supporting Documentation [Additional requirements]
a) If Gerber data is provided, it is for reference only and may not be used for fabrication of the PCB. Only IPC-2581 design data shall be used for PCB fabrication.
b) All supplied documentation and data are company confidential, remain the property of [The Company], and shall be returned to [The Company], or their agent, upon request.
Section 1.3.1.1 Requirement Deviations [Modification]
Requested deviations or modifications to the provided documentation or design data shall be approved in writing by an authorized representative prior to the initiation of PCB fabrication, unless otherwise specified herein.
Section 3.2.11 Hole Fill Insulation Material [Modification]
Electrical insulation material used for hole-fill for metal core boards shall be determined by the fabricator and approved in writing prior to use.
Section 3.2.12 Heatsink Planes, External [Modification]
Deviations to these requirements shall be approved in writing before fabrication starts.
Section 3.3.5.4 Marking Types and Location [Additional requirements]
a) Markings shall be either etched or as legend ink.
b) Markings shall be placed on the solder side or layer n side, where n is greatest numbered layer at locations indicated on the fabrication drawing, or IPC-2581 files as applicable.
c) Markings shall include, but not be limited to the following:
-
Manufacturer’s UL Recognized Component Marking
-
UL Flammability Rating
-
UL 796 Direct Support Rating as indicated in the design documentation
-
Date Code and Lot Code are mandatory
-
Date Code shall be YYWW format
-
The Date Code year (YY) shall use the calendar year
-
Lot Code shall be traceable to the supplier fabrication records
Section 3.7 Solder Mask Requirements [Additional requirements]
a) The solder mask color and gloss shall be specified in the documentation.
b) Liquid Photoimageable (LPI) solder mask shall be used as the default.
c) Solder mask over bare copper (SMOBC) shall be used unless otherwise specified.
Global Approved Deviation Approvals
These items are previously documented data DFM issues that have been raised by one or more fabricators. There are many commonly asked DFM issues. These may be termed “Globally Approved Edits” as they apply to all design packages. The advantage of this list is that future design packages and new suppliers won’t have to ask these questions because you have already provided the answers. This solves the complaint, “Quit asking the same question over and over again.” Here are a few examples:
“The following modifications, as required, to the provided design data do not require pre-approval by [The Company]. The following edits, other than scaling, shall be documented in the DFM report when sent to the technical contact for approval of other items.”
a) Scaling: Incorporate scaling factors to compensate for material shrinkage/expansion in the PCB fabrication process.
b) Solder Mask: Solder mask apertures specified in the data, directly adjacent to exposed conductive features, shall be modified to maintain proper clearance to the exposed conductors.
c) Legend Marking: Legend shall be trimmed or moved from a solder resist opening to avoid printing on exposed conductors.
d) Non-Functional Pads Removal: Non-functional pads on internal signal layers may be removed except for PTH’s greater than 2.5mm [0.098"].
e) Impedance Traces: Dielectric thickness may be modified to meet impedance requirements.
f) Anti-pad Size: May be modified to meet annular ring requirement.
g) Pad Size: May be modified to meet annular ring requirement.
h) PCB Corners: Modify to add a radius to not damage shipping packaging.
i) Date Code Format: Shall be selected by fabricator.
j) Tear Drops: May be added to pad to trace connections as required.
k) Duplicate Holes: Remove all occurrences. If the holes are different sizes, the smaller size shall be deleted.
l) Drill Data: Modify to align to pads for through hole mounted components.
m) Copper Thieving: To improve metal distribution and uniformity across an internal signal or outer layer, copper thieving features may be added to layers, provided the specified impedance and safety isolation requirements are unaffected.
-
The minimum spacing between a thieving, or dummy pad, feature and any conductor shall be 0.100 inches (100 mils) for both internal and external layers
-
The supplier shall provide a graphic representation with size and spacing of thieving that has been added for written approval
The above global deviation examples should be reviewed to ensure that the design performance requirements are met. High speed digital design signal integrity loss and noise budgets are becoming more sensitive to trace and via editing and thus may not allow all approved global edits.
The goal of transferring the design data for manufacturing should be to eliminate DFM issues that may affect the production cycle time, quality or PCB reliability.
Dana Korf is the principal consultant at Korf Consultancy LLC.
More Columns from Dana on Data
Dana on Data: Best Practices in Interpreting Drawing Notes—‘Use Latest Revision’Dana on Data: The Missing AI-NPI Link
Dana on Data: Merging 2D Electrical, 3D Mechanical Worlds
Dana on Data: Resurrecting IPC Class 1
Dana on Data: The Evolution of Fabrication Drawing
Dana on Data: The Insane PCB DFM Process
Dana on Data: eCAD PCB Design Deficiencies
Dana on Data: Nuke the Netlist