-
- News
- Books
Featured Books
- smt007 Magazine
Latest Issues
Current IssueWhat's Your Sweet Spot?
Are you in a niche that’s growing or shrinking? Is it time to reassess and refocus? We spotlight companies thriving by redefining or reinforcing their niche. What are their insights?
Moving Forward With Confidence
In this issue, we focus on sales and quoting, workforce training, new IPC leadership in the U.S. and Canada, the effects of tariffs, CFX standards, and much more—all designed to provide perspective as you move through the cloud bank of today's shifting economic market.
Intelligent Test and Inspection
Are you ready to explore the cutting-edge advancements shaping the electronics manufacturing industry? The May 2025 issue of SMT007 Magazine is packed with insights, innovations, and expert perspectives that you won’t want to miss.
- Articles
- Columns
- Links
- Media kit
||| MENU - smt007 Magazine
Estimated reading time: 6 minutes
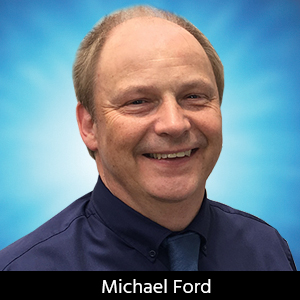
Smart Factory Insights: The Progress of Machine Intelligence
Adversity drives focus, realization, and innovation. This is especially true in manufacturing, which has felt the effects of recent challenges. For decades, manufacturing has been overly focused on short-term business objectives, with little regard for risk or adaptability. This oversight has persisted into automation projects and digital transformation initiatives. Innovators today realize there is no way back, that we must embrace the intelligence we all should have learned.
We’re now seeing the true fragility of our business world after a decade or two of relative calm. When nothing untoward happens for a while, risks get downplayed in favor of short-term results, and complacency takes hold. The enduring focus of automation within manufacturing has been predominantly stuck with Industry 3.0—that is, the automation of physical tasks once performed by humans. Recently however, automation of human thought (aligning with Industry 4.0) has become the origin of true digital transformation. Unfortunately, for many this started at a time of relative calm in the industry, focusing again on short-term profits rather than long-term resilience. But it’s not too late to change.
It’s a Human Resource Issue
The recent trilogy of challenges—COVID-19, political instability in several regions, and a restless climate—have led to known fundamental effects, including shortages, inflation, and human resource issues. It is taking a significant toll. Existing software automation has revealed its true limitations in many cases. Relatively simple automation of operations, optimized to meet short-term goals without real consideration of long-term challenges, has proven to be near-useless. It was left to good, old human intelligence to respond to recent extraordinary events, make quick decisions, and navigate through obstacles, as well as look for opportunities. Lack of investment in flexibility, the acceptance of dependencies on materials and products made in remote locations, as well as reliance on key people in the organization where only one person knows or can perform certain tasks, have led to extreme challenges for many.
In our continuously changing world, we seek to avoid things over which we have little or no control. Local sourcing of key materials, security of operations and data, and automation choices that provide flexibility with a vast range of simultaneous operational and business models, should top the “to do” list, as manufacturing embraces the world’s uncertain future.
The most unexpected and interesting challenge, however, is that during such volatility, we found we could not even rely on human intelligence. We are now experiencing economic patterns of inflation and potential recession, which seem familiar to those old enough to remember the 1980s. Legacy economic tools to deal with these issues, however, seem inappropriate as, unlike previous cases, employment levels are very high—exactly the opposite of previous scenarios. While companies were focused on business challenges, people were also making their own private changes, as they decided (or were forced) to seek a “better life,” moving from roles that were just acceptable to ones that stimulate them. This turbulence in the labor market can be regarded as good news from the digital transformation perspective.
So, Let the Machines Do the Talking
The technology behind automation of physical work continues to evolve considerably. There are more choices of hardware automation solutions than ever before. The priority between flexibility and optimization, however, is now under serious review. Rather than having a person or an automation dedicated to a specific role, we have learned that such resources should be flexible, allowing them to be dynamic across a whole selection of prioritized tasks. Humans have the physical dexterity to be flexible; automation is also making progress.
The real challenge, in both cases, is to provide the continuous step-by-step guidance as to how to perform and complete each task. Humans are then not dependent on niche, rarely used training, nor on specialist knowledge. People receive information in the form of electronic work instructions, and deliver to automation through IIoT-based commands and data exchanges. This innovation brings the need for a holistic view of operations, sourced from the domain of MES, which already provides the central control and management of operations. Standards-based “plug and play” interoperability across the shopfloor, for example with IPC-CFX, is proving its worth, and differentiation from older data exchange mechanisms, as it provides any machine or solution a secure protocol and fully defined unambiguous language.
An extension of this MES intelligence is to automate the decision-making processes that drive operational events. Human intelligence is no longer motivated, or interested in, searching for data and using it to make mindless routine decisions. Retaining sustainable human intelligence will be for those who derive job satisfaction from making complex decisions in an easy and timely way, based on the availability of immediate, accurate, and contextualized knowledge. The intelligence within MES is based on internal complex data models, created from many years of experience, where data is contextualized across many factors. This enables software to take routine decisions and action them, such as the best timing and selection of a material replenishment. This enhances the human contribution in manufacturing to work at a higher level of responsibility and provides for more job satisfaction.
Here is where we see the benefits. As an inherent part of digital transformation, software-based automation that is intelligent and flexible helps resolve both day-to-day business operations, and supports challenging exceptions. It starts with the respect for human intelligence, a change that we have begun to take seriously, and is potentially the most fundamental challenge of anything we’ve faced so far. It may come as a bit of a surprise, though the signs have been there for a while. People want to be more evolved, to get their hands dirty through their chosen hobbies, rather than daily obligations. As humans have left manufacturing operations for whatever reasons, it took out their wealth of skills, knowledge, and intelligence, which perhaps was often taken for granted. It has been especially noticeable during the pandemic when many business-critical exceptions needed to be dealt with. Intelligent software built into automation and machines, and especially modern MES solutions, will fill the gaps. The key requirement is a rich and mature internal data model:
- Representing knowledge about every aspect of the manufacturing operation
- Making and executing routine decisions, with significant flexibility
- Providing key intel to humans with which their intelligence results in real business differentiation
Conclusion
As we move forward, we need to revisit our business practices. Operational risk and dependencies in the supply chain as well as inefficiencies in terms of environmental impact and energy use are sure to be top of mind. We must revisit our strategies behind digital transformation, not just to help automate and optimize existing, fixed operations, but to provide flexibility, to relieve humans from the distractions of data gathering and trivial decision-making, and to create a sustainable and resilient environment.
In between challenges, we will be tempted to revert and focus too intently on short-term goals. Such a strategy helps business for only a short term, while cannibalizing future potential. Let’s seize the benefits that this silver lining has presented and be prepared for any future challenges when they come. By doing so, we increase the quality of life for our human teams that are essential to meet sustainable business objectives.
This column originally appeared in the September 2022 issue of SMT007 Magazine.
More Columns from Smart Factory Insights
Smart Factory Insights: Making Rework a Smart Business OpportunitySmart Factory Insights: The Sustainability Gold Rush
Smart Factory Insights: Today’s Manufacturing Jobs Require a New Skill Set
Smart Factory Insights: Compose Yourself, Mr. Ford
Smart Factory Insights: The Smart Business Case for Local PCB Manufacturing
Smart Factory Insights: Manufacturing Digital Twin—Spanners in the Works
Smart Factory Insights: Machines, People, and AI
Smart Factory Insights: Is Sustainability in Manufacturing a Benefit or Burden?