-
- News
- Books
Featured Books
- design007 Magazine
Latest Issues
Current IssueProper Floor Planning
Floor planning decisions can make or break performance, manufacturability, and timelines. This month’s contributors weigh in with their best practices for proper floor planning and specific strategies to get it right.
Showing Some Constraint
A strong design constraint strategy carefully balances a wide range of electrical and manufacturing trade-offs. This month, we explore the key requirements, common challenges, and best practices behind building an effective constraint strategy.
All About That Route
Most designers favor manual routing, but today's interactive autorouters may be changing designers' minds by allowing users more direct control. In this issue, our expert contributors discuss a variety of manual and autorouting strategies.
- Articles
- Columns
- Links
- Media kit
||| MENU - design007 Magazine
Estimated reading time: 4 minutes
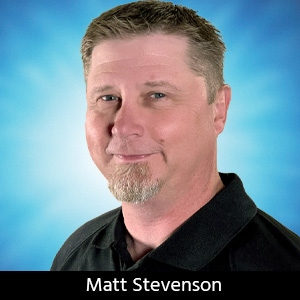
Connect the Dots: Managing Solder for Fewer Heat Sink Failures
Heat sink failures can be difficult to detect, especially when the failure rates are low. But even if the volume of failures is low, those costs quickly run into thousands of dollars. One of the primary causes of heat sink failure is inconsistent soldering of thermal pads. Given the cost of reliability problems, finding a path to improvement is crucial.
Uncontrollable, Unpredictable Solder
The standard, manufacturer-recommended approach for heat sinking is to place large copper pads on both sides of the board under the chip. These pads are then connected with vias to conduct heat, and full solder paste coverage is used to get the best thermal contact. Unfortunately, this approach can cause problems.
The issue is that solder is unpredictable once melted, which puts every board at risk of a poor heat sink connection. This problem is so pervasive that you might be tempted to accept it as the unavoidable cost of doing business. However, there are ways to solve this challenge. There are two main mechanisms that cause these failures: solder wicking through vias and solder movement under large pads.
Solder Wicking Through Vias
If the landing pad is covered in tiny holes, molten solder can run through them to the back of the board. This results in less solder connecting the pad, with the remaining solder distributed unevenly. The wicking will vary from board to board, causing unpredictable consistency and poor reliability.
Common vias are not precision components, and the amount of copper plated onto them varies. Some may be wider than intended and others may be plated partially or fully shut. Identically designed boards that went through the same manufacturing process may now have significantly different thermal responses.
Solder Movement Under Large Pads
It is important to consider the unpredictability of solder movement during reflow. If the board is warped or there is not enough solder under the slug, capillary action can pull the solder to one side of the chip. Attempt to correct this by applying more solder, and the chip might float right off the signal pins. Excess solder can overflow the pad, sending solder balls out to short or bridge other areas of the board.
The varying amount of solder pulled through the vias only exacerbates the problem and hinders attempts to correct for it by adjusting the amount of paste used.
Finding the Solution
A proper solution requires fixing two different problems, but both are related to solder. First, solder must be prevented from wicking through vias and ending up on the wrong layers of a PCB. Second, solder must be prevented from moving past its area of application.
The solution can be approached with two different methods:
- First, apply solder mask over the landing pad and open circular “islands” for paste application. If the solder will not behave in a large area, break that area up into an array of smaller areas. Since solder mask restricts the paste to its area of application, this reduces the amount of solder connecting the chip to the board, increasing the consistency. The circular solder paste apertures release the solder more reliably than those with sharp corners, which helps prevent loose solder balls.
- Second, surround the “islands” with small (~12 mil or smaller) vias that are tented and covered with solder mask. Removing the vias from the immediate area being soldered and tenting them prevents any stray solder from wicking down to the other side of the board while still providing good thermal transfer to the pads underneath. Add these vias as close as possible to the islands. The solder mask tenting will block any solder that wicks onto an exposed via due to manufacturing tolerances.
When implementing this solution, keep in mind a few key rules:
- Make sure the pad under the chip is a solid copper plane, so it will spread out the heat.
- To give maximum coverage to the heat slug, use a hexagonal packing pattern for the solder islands.
- The solder mask tents should be the same size as the resist mask opening on these islands. This ensures that adequate solder is present to bond to the chip.
- Thermal spokes will reduce thermal conductivity, so don’t use them on any layer of the vias.
- Vias should be solder mask tented, not plugged or filled. The epoxy in solder mask plugged vias may not cure fully and will tend to expand and erupt if subject to enough heat.
Implementing the Design
The most efficient way to implement this is to make it part of your package definition—making it uniformly applied to all similar parts. Unfortunately, many CAD packages do not support the direct addition of vias and copper planes to package designs. One workaround is to create square SMD pads to act as the top and bottom copper sinks, as well as small plated through-hole pads to act as the vias. These can then be configured as unconnected pins in your component definition. You may also have to create custom paste and solder masks for these pins.
If you are running into failures that may be caused by solder problems with thermal pads, try out this solution for your next project. We think you will be happy with the results. The benefits speak for themselves: fewer failures, a more consistent product, and happier customers.
This column originally appeared in the November 2022 issue of Design007 Magazine.
Download The Printed Circuit Designer’s Guide to... Designing for Reality by Matt Stevenson.
More Columns from Connect the Dots
Connect the Dots: How to Avoid Five Common Causes of Board FailureConnect the Dots: Sequential Lamination in HDI PCB Manufacturing
Connect the Dots: The Future of PCB Design and Manufacturing
Connect the Dots: Proactive Controlled Impedance
Connect the Dots: Involving Manufacturers Earlier Prevents Downstream Issues
Connect the Dots: Stop Killing Your Yield—The Hidden Cost of Design Oversights
Connect the Dots: Designing for Reality—Routing, Final Fab, and QC
Connect the Dots: Designing for Reality—Surface Finish