-
- News
- Books
Featured Books
- pcb007 Magazine
Latest Issues
Current IssueInventing the Future with SEL
Two years after launching its state-of-the-art PCB facility, SEL shares lessons in vision, execution, and innovation, plus insights from industry icons and technology leaders shaping the future of PCB fabrication.
Sales: From Pitch to PO
From the first cold call to finally receiving that first purchase order, the July PCB007 Magazine breaks down some critical parts of the sales stack. To up your sales game, read on!
The Hole Truth: Via Integrity in an HDI World
From the drilled hole to registration across multiple sequential lamination cycles, to the quality of your copper plating, via reliability in an HDI world is becoming an ever-greater challenge. This month we look at “The Hole Truth,” from creating the “perfect” via to how you can assure via quality and reliability, the first time, every time.
- Articles
- Columns
- Links
- Media kit
||| MENU - pcb007 Magazine
iNEMI Call for Participation: Hybrid PCBs for Next Generation Applications
December 1, 2022 | iNEMIEstimated reading time: 1 minute
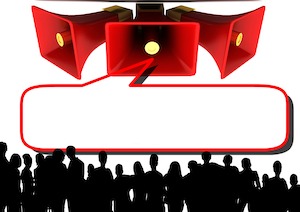
An increasing range of high-speed applications require low loss dielectric laminate materials within a printed circuit board (PCB) stack-up to achieve the required electrical performance. However, these materials are more expensive than standard loss materials. One solution to minimize cost is to selectively use lower loss material on only the layers that require higher performance and use cheaper material on layers that do not require high performance. This “hybrid” combination of laminate materials can provide the required electrical performance at minimum cost, but the combination of dissimilar dielectric materials has associated challenges for PCB fabrication that can negatively impact reliability if manufacturing processes are not optimized and/or the materials are in some way incompatible.
According to an iNEMI survey, determining material compatibility and minimizing warpage are among the greatest challenges in hybrid PCB manufacturing. iNEMI’s Hybrid PCBs for Next Generation Applications project, led by Sarah Czaplewski (IBM) and Steven Ethridge (Dell), will evaluate how placement of dielectric materials with dissimilar properties within a hybrid stack-up impacts PCB thermomechanical performance. The team will study the impact of the following parameters on via hole reliability and PCB warpage:
- Material placement within a symmetrical hybrid stack-up with materials having different properties such as CTE and/or gel point
- Various ratios of dissimilar dielectric materials in a symmetrical hybrid stack-up (i.e., 25% material A & 75% material B; 50% material A & 50% material B, etc.)
- Resin asymmetry in the stack-up
The results of this project will increase understanding of how hybrid stack-up designs influence PCB thermomechanical performance. OEMs and PCB manufacturers may use this information to improve stack-up designs to be more robust and reliable as well as reduce the number of design and test iterations, thereby saving cost and development time. Laminate manufacturers may use this information to help tailor resin systems for use in hybrid constructions to better support customer needs.
Registration
This webinar is open to industry; advance registration is required.
Wednesday, December 7, 2022
12:00-1:00 p.m. EST (US)
9:00-10:00 a.m. PST (US)
6:00-7:00 p.m. CET (Europe)
Testimonial
"In a year when every marketing dollar mattered, I chose to keep I-Connect007 in our 2025 plan. Their commitment to high-quality, insightful content aligns with Koh Young’s values and helps readers navigate a changing industry. "
Brent Fischthal - Koh YoungSuggested Items
Happy’s Tech Talk #41: Sustainability and Circularity for Electronics Manufacturing
08/13/2025 | Happy Holden -- Column: Happy’s Tech TalkI attended INEMI’s June 12 online seminar, “Sustainable Electronics Tech Topic Series: PCBs and Sustainability.” Dr. Maarten Cauwe of imec spoke on “Life Cycle Inventory (LCI) Models for Assessing and Improving the Environmental Impact of PCB Assemblies,” and Jack Herring of Jiva Materials Ltd. spoke on “Transforming Electronics with Recyclable PCB Technology.” This column will review information and provide analysis from both presentations.
EMC-Taiwan Announces Further Investment in North America
08/11/2025 | Elite Material Co. LtdElite Material Company (EMC)-Taiwan announced that it has made a commitment to invest $80 million dollars in the Arlon EMD factory in Rancho Cucamonga, CA it acquired at the end of 2020.
EMC Taiwan Receives IPC-4101 Qualified Products Listing Certification
08/08/2025 | Global Electronics AssociationIPC’s Validation Services Program has awarded an IPC-4101 Qualified Products Listing (QPL) to Elite Materials Co. (EMC), an electronics base material manufacturing company headquartered in Taoyuan City, Taiwan.
DuPont Reports Second Quarter 2025 Results
08/06/2025 | PRNewswireNet sales increased 3% led by organic sales growth of 2% which consisted of a 4% increase in volume partially offset by a 2% decrease in price. Currency was a 1% benefit.
Insulectro Promotes Mitchell Benson to Product Manager for Laminates
07/29/2025 | InsulectroInsulectro, the largest distributor of materials used in the manufacturing of printed circuit boards and printed electronics, announces the promotion of Mitchell Benson to Product Manager for its rigid laminate portfolio.