-
- News
- Books
Featured Books
- smt007 Magazine
Latest Issues
Current IssueWhat's Your Sweet Spot?
Are you in a niche that’s growing or shrinking? Is it time to reassess and refocus? We spotlight companies thriving by redefining or reinforcing their niche. What are their insights?
Moving Forward With Confidence
In this issue, we focus on sales and quoting, workforce training, new IPC leadership in the U.S. and Canada, the effects of tariffs, CFX standards, and much more—all designed to provide perspective as you move through the cloud bank of today's shifting economic market.
Intelligent Test and Inspection
Are you ready to explore the cutting-edge advancements shaping the electronics manufacturing industry? The May 2025 issue of SMT007 Magazine is packed with insights, innovations, and expert perspectives that you won’t want to miss.
- Articles
- Columns
- Links
- Media kit
||| MENU - smt007 Magazine
Estimated reading time: 4 minutes
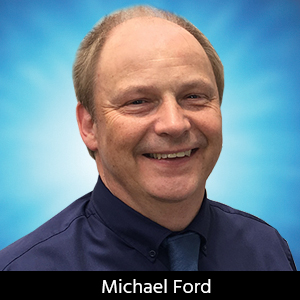
Smart Factory Insights: AIs Without Context Are Dumb
We often discuss the emergence of artificial intelligence in terms of how it will save us, or if movies are to be believed, how it might terminate us. The countless annoyances AIs inject into our daily lives can make us wonder: Do they already have a plan? We need to adequately consider context vs. privacy when deciding how to integrate AI technology into our lives, especially within our factories.
Picture this: After a quick search on the internet, I bought a pair of golfing gloves. Big mistake. Advertising AIs across the globe immediately inundated me with hundreds of golf-related recommendations. Golf gloves, clubs, balls, socks, markers, books, weekend getaways—all a complete waste of not only data storage and energy, but also my time. I have no interest in golf whatsoever; the gloves were a present for a friend. The lesson here is that AIs often fail to work effectively because they lack adequate context. Marketing divisions pay good money to push billions of targeted ads each day, justifying the cost for that one-in-a-million hit. But all of us, along with the environment, are the ones who are really paying the price.
In my case, the privacy restrictions I set on my data prevented AIs from accessing certain facts about my purchase—which I'm very happy about. Advertising companies who own these AIs will argue that more data leads to better value from their services, but is that worth the potential loss of our privacy?
This conundrum is a massive issue facing almost all digital transformation, Smart manufacturing, and Industry 4.0 projects. The situation is not so bad within a factory running, for example, a Smart MES solution. Data related to design, manufacturing capabilities and configurations, operations, measurements etc., are all collected and stored in either a secure manufacturing environment or private cloud storage space. An MES can produce a variety of values by contextualizing the collected data, providing visibility, control, assurance, and optimization of manufacturing execution through material flows, operator assignments, and both machine and operator work instructions.
Well, at least that used to be the case. This open sharing vs. privacy issue can now be seen in Smart manufacturing, where external parties might request—even demand—access to private manufacturing information. Data relating to customer assurance, proof of product and material provenance, predictive maintenance, energy profiling, quality analytics—everything is fair game. Honoring these requests means potentially exposing sensitive intellectual property details. Further, intelligence—whether artificial or human—can use this newly shared information for other purposes. How do we determine what data to share, who to share it with, and what purposes it can be used for? Once we decide these parameters, how do we enforce them?
The good news is that new digital technology standards, called Distributed IDs (DIDs) and Verifiable Credentials (VCs), have been developed by the World-Wide Web Consortium (W3C) to bring a simple resolution to this conundrum. These technologies use the blockchain to allow provable facts to be shared between authorized parties without the disclosure of the original private information. IPC has already begun work on new standards to determine how these technologies may be utilized within or around the IPC Digital Twin, traceability, cybersecurity, component-level assurance, Connected Factory Exchange (CFX), and IPC-2581 design data standards.
What might this look like in practice? A VC, for example, could help determine whether a product can carry a “Made in the USA” designation. This is by no means a simple question, as a certain percentage of assembly and material sourcing locations need to be considered before making the determination. All that data is recorded, with bits and pieces retained by the many manufacturing, assembly, and distribution companies involved in the supply network. The VC is a trusted algorithm that both calculates the proof of a claim and provides this claim as a small digital identity. Together with the proven identity (DID) of the source, this identity is stored openly (but securely) using blockchain technology so that companies can avoid sharing protected information while preventing any data tampering. Throughout the supply network, MES solutions associate materials with products at the point of assembly and thereby create a hierarchy and inheritance of proofs based on consumed materials. For the completed product, the VA is a record that can be accessed by authorized parties to decisively answer the “Made in the USA” question without the need to divulge private data about materials or products.
This is a simple example, one of many now being considered as a solution for the industry, that enables Smart manufacturing and supply network data to provide that crucial contextual element to external parties without compromising privacy.
This is one of the many subjects that will be introduced and discussed at IPC APEX EXPO 2023 in a Professional Development Course named, “Application of IPC Smart and Secure Digital Transformation Standards,” scheduled from 8 to 11 a.m. Sunday, Jan. 22. The course will discuss how the new IPC Factory of the Future standards can work together to provide an interoperable, secure environment for the full lifecycle of Smart manufacturing. This is a unique opportunity to understand the context of the use and adoption of each IPC standard as they relate to each other in the creation of new digital best practices, which will be relevant to any holistic OEM, EMS, or solution-provider business.
Many key industry experts related to the development and driving adoption of each of these standards, have teamed up to present this course. While 8 a.m. may seem early, there's no better time than early morning—as many birds can attest—to expand your horizons. Please consider joining us to learn more about these exciting new developments in the industry.
This column originally appeared in the December 2022 issue of SMT007 Magazine.
More Columns from Smart Factory Insights
Smart Factory Insights: Making Rework a Smart Business OpportunitySmart Factory Insights: The Sustainability Gold Rush
Smart Factory Insights: Today’s Manufacturing Jobs Require a New Skill Set
Smart Factory Insights: Compose Yourself, Mr. Ford
Smart Factory Insights: The Smart Business Case for Local PCB Manufacturing
Smart Factory Insights: Manufacturing Digital Twin—Spanners in the Works
Smart Factory Insights: Machines, People, and AI
Smart Factory Insights: Is Sustainability in Manufacturing a Benefit or Burden?