-
- News
- Books
Featured Books
- pcb007 Magazine
Latest Issues
Current IssueSales: From Pitch to PO
From the first cold call to finally receiving that first purchase order, the July PCB007 Magazine breaks down some critical parts of the sales stack. To up your sales game, read on!
The Hole Truth: Via Integrity in an HDI World
From the drilled hole to registration across multiple sequential lamination cycles, to the quality of your copper plating, via reliability in an HDI world is becoming an ever-greater challenge. This month we look at “The Hole Truth,” from creating the “perfect” via to how you can assure via quality and reliability, the first time, every time.
In Pursuit of Perfection: Defect Reduction
For bare PCB board fabrication, defect reduction is a critical aspect of a company's bottom line profitability. In this issue, we examine how imaging, etching, and plating processes can provide information and insight into reducing defects and increasing yields.
- Articles
- Columns
- Links
- Media kit
||| MENU - pcb007 Magazine
Estimated reading time: 5 minutes
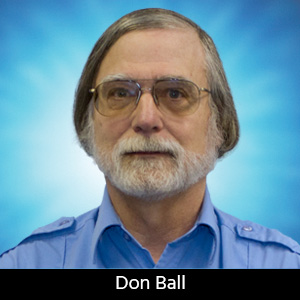
The Chemical Connection: Basics of Cupric Chloride Etchant
Cupric chloride (CuCl2) is an etchant that has capabilities that make it a great application in PCB manufacturing. Although it is not the most used etchant in the industry, it proves to be beneficial by being simple to maintain. Maintaining CuCl2 is relatively forgiving in comparison to alkaline etchant because there are only a handful of parameters you need to monitor. If CuCl2 seems like it would be an appealing etchant to use for your PCB etch process, here are some basic parameters that are key to understanding how to maintain it.
Specific Gravity
Specific gravity (SG) is a main factor that must be watched and controlled to maintain a consistent etch quality. I’ve mentioned in previous columns that as you etch more panels, the metal content of your etchant increases. This increase in metal content makes your etching solution have a higher SG, and SG and etch rate tend to have an inverse relationship; thus, the higher your specific gravity gets, the slower your etch rate will be. The maximum etch rate for cupric comes in between the range of 28 to 36 °Bé (SG: 1.2393 to 1.3303)1. Thankfully, the normal CuCl2 etching solution you will receive comes in the range of 32 to 36 °Bé. Although specific gravity is one of the key factors, unlike alkaline etchant, there are no critical risks to falling out of this range. If the SG gets too high, you can simply add more water to your etching solution; if it is too low, just simply add more cupric crystals or etch more panels.
Temperature
Temperature is also a parameter that should be controlled for consistent etch quality. The higher the temperature, the faster your reaction rate will be. The temperature of the etcher bath tends to have little effect on etch factor and only improves etch rate; thus, cupric etchers are typically run at the highest possible temperature. The standard temperature to etch at is 130°F. Controlling temperature is also simple because it is done through the etching equipment by monitoring the temperature with probes that will activate or deactivate the machine’s heating and cooling systems as needed.
Oxidation-reduction Potential
Oxidation-reduction potential (ORP) is a major factor to monitor with CuCl2. ORP can be understood as a measurement of how ready your etchant is to etch metal. It does this by measuring the ratio of Cu+2 ions (from CuCl2) and Cu+1 ions (from CuCl—the spent form of the etchant). As you etch, the Cu+2 ions will decrease and the Cu+1 ions will increase, and thus the ORP value will drop. A low ORP is a sign that you need to add reagents to perform regeneration so that the Cu+1 ions will be converted back to Cu+2. There are three main ways that you can perform this regeneration; if you wish to know more, please see my November 2022 column, “Cupric Chloride Regeneration Options.”
ORP is measured via an ORP probe that provides a value in the units of millivolts. If you are curious where the millivolts value comes from, the equation is shown in Figure 3.
Figure 3: Nernst equation for ORP in CuCl2 etchant. Eo is the standard potential of your electrode, R is the gas law constant, T is temperature (in Kelvin), n is number of electrons transferred per molecule.
If you are a person who does not like math, no worries; what you mostly need to understand is that the ideal ORP range for CuCl2 is 540 to 560 mV. It is best to avoid overshooting ORP past the value of 600 mV because typically there are not enough Cu+1 ions in a solution to absorb all the chlorine used in regeneration. This can lead to a chance of chlorine gas forming and being released into the atmosphere, which can be dangerous—so it is best to avoid high ORP values. If you are too low on ORP, you need to add more regenerating components so the regeneration reaction can replenish the Cu+2 ions. If your ORP is too high, you can remedy this by simply running panels. However, if the ORP is too high and causes an unpredictably high etch rate, it is best to find some way to introduce copper into your etch bath to bring the ORP back down. Bringing the ORP down can mean running a piece of scrap copper through the machine or dissolving copper powder into the solution. If you are finishing a shift and you notice the ORP is running low, you can leave the etchant to rest during a break or overnight because as it sits, it will react with the oxygen and increase the ORP again.
Free Hydrochloric Acid Content
Another critical factor to monitor in your CuCl2 is free hydrochloric acid (HCl) content. For CuCl2 to etch efficiently, there needs to be a detectable amount of excess acid. This is because CuCl2 is relatively insoluble in water on its own, and it needs to be in a highly acidic solution to prevent the CuCl2 solids from precipitating out of the solution. The HCl also helps remove the copper oxide layer that is present on copper panels. CuCl2 is not efficient at removing this, but with HCl present, that layer gets removed, allowing for easier access to the copper surface. Without HCl, the etch rate of CuCl2 is cut in half.
Typically, the higher the HCl levels, the faster the etch rate. Although higher HCl content increases etch rate, it comes with the drawback of increasing undercut. Since there are some drawbacks to higher HCl contents, it is recommended to keep the free acid in a range of 1 to 2 N HCl. One major consideration with free acid content is the difficulty of keeping a close eye on this parameter. This is because there are a lot of technicalities in trying to measure it. The only established, reliable method of doing this is through routine titrations.
Conclusion
Once you know the basics of maintaining CuCl2, and both the spray pressures and total etch time you need to meet your PCB specifications, running your etching process should be fairly easy. To summarize the parameters discussed in this column, see Table 1 for the recommended parameter ranges for cupric etchant.
References
1. “Process Guidelines for Cupric Chloride Etching,” Chemcut.net.
This column originally appeared in the December 2022 issue of PCB007 Magazine.
More Columns from The Chemical Connection
The Chemical Connection: Through-glass Vias in Glass SubstratesThe Chemical Connection: Reducing Defects in Circuit Board Production
The Chemical Connection: Common Misconceptions in Wet Processing
The Chemical Connection: Surface Finishes for PCBs
The Chemical Connection: Earthquakes, Astronauts, and Aquatics—A Lighter Look at the Past
The Chemical Connection: Better Fabs Attract a Better Workforce
The Chemical Connection: Can Changing Spray Nozzles Improve My Etch Quality?
The Chemical Connection: Getting the Best from Your Cupric Chloride Etchant