-
- News
- Books
Featured Books
- design007 Magazine
Latest Issues
Current IssueShowing Some Constraint
A strong design constraint strategy carefully balances a wide range of electrical and manufacturing trade-offs. This month, we explore the key requirements, common challenges, and best practices behind building an effective constraint strategy.
All About That Route
Most designers favor manual routing, but today's interactive autorouters may be changing designers' minds by allowing users more direct control. In this issue, our expert contributors discuss a variety of manual and autorouting strategies.
Creating the Ideal Data Package
Why is it so difficult to create the ideal data package? Many of these simple errors can be alleviated by paying attention to detail—and knowing what issues to look out for. So, this month, our experts weigh in on the best practices for creating the ideal design data package for your design.
- Articles
- Columns
- Links
- Media kit
||| MENU - design007 Magazine
A Sneak Peak with Jim van den Hogen
December 29, 2022 | Andy Shaughnessy, Design007 MagazineEstimated reading time: 3 minutes
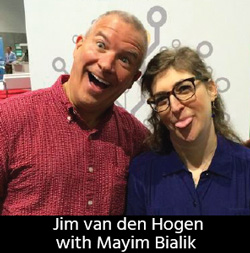
Jim van den Hogen has been teaching PCB designers and design engineers about fabrication processes for decades. Twenty years ago, I had the opportunity to see a class of his at PCB West; even back then, the room was jammed with designers eager to learn more about DFM techniques. Now Jim is bringing his teaching expertise to IPC APEX EXPO 2023 this January with a similar class directed at PCB designers. I asked Jim to give us a sneak peek into his curriculum and to share what he hopes attendees will take away from his class, as well as his thoughts on how to best bridge the gap between design and fabrication.
Andy Shaughnessy: Jim, tell us a little about your Professional Development class at IPC APEX EXPO 2023.
Jim van den Hogen: The class walks you through a basic multilayer fabrication process from front to back. It includes discussions on material, stackups, via metrics, aspect ratios, solder mask, surface finish, and various other fabrication-related topics. I have several sample sets that I’ll pass around for students to inspect. Each sample set has over 25 individual pieces, all of them taken at various steps of a multi-layer fabrication process, so students will be able to visualize the concepts we’ll be discussing in the class. We will also cover the typical requirements for a PCB fabrication drawing. The final portion of the class will cover array or manufacturing panel design, and ways to maximize cost savings when working with these processes.
Shaughnessy: Why should someone attend your class?
Van den Hogen: Students in my glass will gain a strong foundation in the basics of PCB fabrication and will get to go in-depth on the complexities of the process. You will learn how your design and specification thereof can affect the fabrication process and, in turn, how the delivered PCB can affect the assembly process.
Shaughnessy: It’s a fabrication class, but your target audience includes both PCB designers and design engineers. I know many designers who haven’t been in a board shop in decades, if at all; does that seem to be the case with your classes?
Van den Hogen: Yes, there are many designers and engineers that have never set foot in a board shop. It is difficult to understand the complexity of board fabrication without firsthand experience. While the PCB Fabrication Basics course presentation will get you close, a “behind the glass” board shop tour can tie it all together.
Shaughnessy: What is the most important piece of advice you give your attendees?
Van den Hogen: Engage with your suppliers up front. This becomes increasingly more important as your designs become more complex. Work with your supplier to define a fabrication stack-up that includes material selection, copper weights, plating thicknesses, and via/trace/space metrics. You will want to discuss what qualification specification(s) the finished product will need to meet. This may be an IPC specification (typically IPC-6012 and IPC-4101) or a corporate specification. This should be done as early in the design process as possible, preferably before you start placing parts in your design.
Shaughnessy: Is there anything else you’d like to add?
Van den Hogen: This class has been presented before and most of the attendee feedback comments mentioned how the sample sets that are passed out during class make it easier to grasp many of the topics presented. Also, while at the conference, you should plan on attending a standards development committee meeting. If you disagree with what is written or would like to help improve or update current specifications, that is where you’ll have your chance to make your voice heard.
Shaughnessy: Designers do like to share their opinions, so you may be in luck there. Thanks for talking with me, Jim.
Van den Hogen: Thank you, Andy.
Suggested Items
SHENMAO Strengthens Semiconductor Capabilities with Acquisition of PMTC
07/10/2025 | SHENMAOSHENMAO America, Inc. has announced the acquisition of Profound Material Technology Co., Ltd. (PMTC), a premier Taiwan-based manufacturer of high-performance solder balls for semiconductor packaging.
KYZEN to Highlight Understencil and PCB Cleaners at SMTA Querétaro Expo and Tech Forum
07/09/2025 | KYZEN'KYZEN, the global leader in innovative environmentally responsible cleaning chemistries, will exhibit at the SMTA Querétaro Expo & Tech Forum, scheduled to take place Thursday, July 24, at Centro de Congresos y Teatro Metropolitano de Querétaro.
Driving Innovation: Direct Imaging vs. Conventional Exposure
07/01/2025 | Simon Khesin -- Column: Driving InnovationMy first camera used Kodak film. I even experimented with developing photos in the bathroom, though I usually dropped the film off at a Kodak center and received the prints two weeks later, only to discover that some images were out of focus or poorly framed. Today, every smartphone contains a high-quality camera capable of producing stunning images instantly.
Hands-On Demos Now Available for Apollo Seiko’s EF and AF Selective Soldering Lines
06/30/2025 | Apollo SeikoApollo Seiko, a leading innovator in soldering technology, is excited to spotlight its expanded lineup of EF and AF Series Selective Soldering Systems, now available for live demonstrations in its newly dedicated demo room.
Indium Corporation Expert to Present on Automotive and Industrial Solder Bonding Solutions at Global Electronics Association Workshop
06/26/2025 | IndiumIndium Corporation Principal Engineer, Advanced Materials, Andy Mackie, Ph.D., MSc, will deliver a technical presentation on innovative solder bonding solutions for automotive and industrial applications at the Global Electronics A