-
- News
- Books
Featured Books
- smt007 Magazine
Latest Issues
Current IssueSupply Chain Strategies
A successful brand is built on strong customer relationships—anchored by a well-orchestrated supply chain at its core. This month, we look at how managing your supply chain directly influences customer perception.
What's Your Sweet Spot?
Are you in a niche that’s growing or shrinking? Is it time to reassess and refocus? We spotlight companies thriving by redefining or reinforcing their niche. What are their insights?
Moving Forward With Confidence
In this issue, we focus on sales and quoting, workforce training, new IPC leadership in the U.S. and Canada, the effects of tariffs, CFX standards, and much more—all designed to provide perspective as you move through the cloud bank of today's shifting economic market.
- Articles
- Columns
- Links
- Media kit
||| MENU - smt007 Magazine
Estimated reading time: 6 minutes
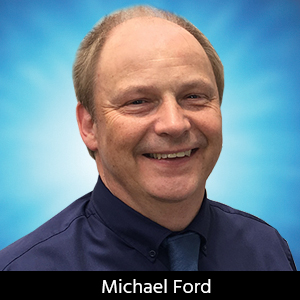
Smart Factory Insights: An Unblinkered View
For many, blindly going where no one has gone before is just a normal day in the factory. As new products are introduced, manufacturing is expected to provide perfect products based primarily on assumptions and reverse engineering. Without accurate and complete product data, there can be no engineering automation, which results in a complete waste of energy. This should no longer be acceptable in the industry. A lack of adequate contextualizing of product information creates unnecessary cost and risk in manufacturing operations, thereby limiting competitiveness. What’s behind the industry’s reluctance to change on this matter?
The key reason relates to security. Releasing full design data to manufacturing exposes valuable intellectual property (IP), which could make its way to competitors. The current paradigm wherein we trade performance for security needs to be destroyed if we, as an industry, will ever succeed in our business goals. Recently, performance and security considerations have become more urgent and significant, such that we will soon reach a crucial tipping point. On one side, there is a clear expectation for assembly manufacturing to be as efficient as possible. Operational exceptions, compromises, and defect rates that were once acceptable are no longer viable in a successful assembly operation; these include general wastes of time, resources, and investment, including delayed deliveries and poor quality. Any activity that invokes waste of any kind is unacceptable. Perfection is paramount.
Digital manufacturing technology has now come of age, making automated processing an integral component of manufacturing engineering software. These new processes are meant to eliminate the needless, repetitive, and error-prone conventional methods that have long guided the industry’s decision-making. Product design data has been fully digitized, comprising 3D-CAD data, bills of materials (BOMs), and PCB layouts and specifications for electronics assembly. From a layperson’s perspective, product data simply needs to be converted into instructions needed for the entire assembly operation to take place. Instructions are needed for automated processes, such as those assigned to machines and robots, as well as for human assembly operators; all this is derived from product data. With product design tools and ERP systems already computerized, why is so much work still done manually?
Back in the days of high volumes and limited product mix, manually compiling data worked fine. Today, there are many more product variants, even customized product variants that require tailoring assembly at key operations. For example, each core chassis in a mobile phone has many thousands of active variants. At the other extreme, variability is open-ended, such as the height of a bespoke piece of furniture, or the dimensions of a window blind. Humans can handle all this variation, but it takes time; a lack of automation coupled with an exponential increase in degree of variation makes mistakes inevitable. In addition, people with essential skills are now leaving the manufacturing industry, and there’s little motivation for new people to take on these stressful and repetitive roles for so little reward.
Removing low-level and repetitive critical actions from manufacturing engineering is essential. With digital product data, manufacturing engineering tools now have the opportunity to elevate engineering's contributions. Although digital product design information has been available for some time, few operations have set up the data flows necessary to handle it. Very few tools on the market have the built-in capability to use such data as their core driver, yet digital manufacturing engineering tools offer innumerable benefits, including the ability to quickly expose any exceptions or specialist requirements inherent in a design via the enhanced visibility provided by digital design data. New digital best practices make it possible to automate processes associated with an individual product, including assigning product configurations, selecting materials, and creating work instructions. Automating these processes helps limit operational mistakes, defects, and delays.
This effect of automation on the operation is not restricted to new products. Digital manufacturing engineering allows risk-free, on-the-fly production allocation; these processes now take seconds as opposed to days. Engineering is now in the driver’s seat, replacing the individual who, until now, has blindly pushed the car along the road. Contextualizing designs with data collected from the shop floor enables immediate decision-making, which improves operational effectiveness overall; low-level decisions are now made automatically. And because every data point is precisely considered in the context of the design, variant, material, process, timing, etc., overall value increases. This all sounds great, doesn’t it?
However, most companies are not using digital design data to automate their manufacturing engineering processes. Company profitability and survivability are being compromised in lieu of IP security. Protecting IP is not new. The latest products from competitors are being physically torn down and their features, functions, and technologies analyzed in labs run by all the major product design teams. A competitor’s design data can now be reverse engineered in minutes. The risk of cloned, compromised, and even counterfeit products has become a major concern for the industry.
While these concerns are legitimate, everything comes down to trust between the company owning the product IP and the companies involved in the manufacturing. Such companies are generally diligent about providing contracts and agreements that protect the IP of their customers. It is extremely difficult, however, to ensure that every person with access to that data will refrain from leaking it to the many individuals and companies offering significant incentives to do so. Dealing with sensitive data requires mechanisms that ensure minimum risk and access to a minimum number of people. Engineering automation eliminates the need for a person to have access to the design data itself; instead, they need only have access to the various abstracts created from it. Technologies available today can ensure that holistic design data never leaves the security of its owner’s servers. Authenticated engineering solutions allow secure, selective access on demand, with no need to store core design data locally. Trust is earned through long-term relationships, but as trusted people are always leaving companies, trust can’t always be a part of the equation.
Most companies are now digitally transforming their operations in ways that they consider “safe” for their business. But these changes need to be made as part of an overarching strategy, not as a piecemeal, step-by-step process meant to preserve the balance between performance and security. Sharing design data that is then processed manually offers few benefits, especially because the increased risk of IP leakage is high. In contrast, modern digital manufacturing engineering tools prevent people from manipulating raw design data. Automating low-level jobs means that engineers can work at an abstracted layer from the data. Any design data needed by machines or in work instructions is thereby isolated from the main design IP, which has very little value when it can’t be painstakingly reverse engineered.
With appropriate IT security practices in place, automating manufacturing engineering creates an environment in which products can be reliably made with reduced exceptions and defects. These systems are also very safe from threats to IP leakage, since they can designate or prevent access to core design data as necessary. Trustworthy companies who want their digital transformation projects to remain competitive need to consider updating the entirety of their data flow and automation practices so as not to get caught in this “blind leading the blind” trap of modern information technology.
This column originally appeared in the January 2023 issue of SMT007 Magazine.
More Columns from Smart Factory Insights
Smart Factory Insights: Making Rework a Smart Business OpportunitySmart Factory Insights: The Sustainability Gold Rush
Smart Factory Insights: Today’s Manufacturing Jobs Require a New Skill Set
Smart Factory Insights: Compose Yourself, Mr. Ford
Smart Factory Insights: The Smart Business Case for Local PCB Manufacturing
Smart Factory Insights: Manufacturing Digital Twin—Spanners in the Works
Smart Factory Insights: Machines, People, and AI
Smart Factory Insights: Is Sustainability in Manufacturing a Benefit or Burden?