-
- News
- Books
Featured Books
- pcb007 Magazine
Latest Issues
Current IssueInner Layer Precision & Yields
In this issue, we examine the critical nature of building precisions into your inner layers and assessing their pass/fail status as early as possible. Whether it’s using automation to cut down on handling issues, identifying defects earlier, or replacing an old line...
Engineering Economics
The real cost to manufacture a PCB encompasses everything that goes into making the product: the materials and other value-added supplies, machine and personnel costs, and most importantly, your quality. A hard look at real costs seems wholly appropriate.
Alternate Metallization Processes
Traditional electroless copper and electroless copper immersion gold have been primary PCB plating methods for decades. But alternative plating metals and processes have been introduced over the past few years as miniaturization and advanced packaging continue to develop.
- Articles
- Columns
Search Console
- Links
- Media kit
||| MENU - pcb007 Magazine
NASA Turns to AI to Design Mission Hardware
February 10, 2023 | NASAEstimated reading time: 3 minutes
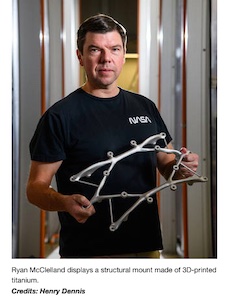
Spacecraft and mission hardware designed by an artificial intelligence may resemble bones left by some alien species, but they weigh less, tolerate higher structural loads, and require a fraction of the time parts designed by humans take to develop.
“They look somewhat alien and weird,” Research Engineer Ryan McClelland said, “but once you see them in function, it really makes sense.”
McClelland pioneered the design of specialized, one-off parts using commercially available AI software at NASA’s Goddard Space Flight Center in Greenbelt, Maryland, through a process he has dubbed evolved design.
To create these parts, a computer-assisted design (CAD) specialist starts with the mission’s requirements and draws in the surfaces where the part connects to the instrument or spacecraft – as well any bolts and fittings for electronics and other hardware. The designer might also need to block out a path so that the algorithm doesn’t block a laser beam or optical sensor. Finally, more complex builds might require spaces for technicians’ hands to maneuver for assembly and alignment.
Once all off-limits areas are defined, the AI connects the dots, McClelland said, producing complex structure designs in as little as an hour or two. “The algorithms do need a human eye,” he said. “Human intuition knows what looks right, but left to itself, the algorithm can sometimes make structures too thin."
These evolved parts save up to two-thirds of the weight compared to traditionally designed components, he said, and can be milled by commercial vendors. “You can perform the design, analysis and fabrication of a prototype part, and have it in hand in as little as one week,” McClelland said. “It can be radically fast compared with how we’re used to working.”
Parts are also analyzed using NASA-standard validation software and processes to identify potential points of failure, McClelland said. “We found it actually lowers risk. After these stress analyses, we find the parts designed by the algorithm don’t have the stress concentrations that you have with human designs. The stress factors are almost ten times lower than parts designed by an expert human designer.”
McClelland’s evolved components have been adopted by NASA missions in different stages of design and construction, including astrophysics balloon observatories, Earth-atmosphere scanners, planetary instruments, space weather monitors, space telescopes, and even the Mars Sample Return mission.
Goddard physicist Peter Nagler turned to evolved design to help develop the EXoplanet Climate Infrared TElescope (EXCITE) mission, a balloon-borne telescope designed to study hot Jupiter-type exoplanets orbiting other stars. Currently under construction and testing, EXCITE plans to use a near-infrared spectrograph to perform continuous observations of each planet's orbit about its host star.
“We have a couple of areas with very tricky design requirements,” Nagler said. “There were combinations of specific interfaces and exacting load specifications that were proving to be a challenge for our designers.”
McClelland designed a titanium scaffold for the back of the EXCITE telescope, where the IR receiver housed inside an aluminum cryogenic chamber connects to a carbon fiber plate supporting the primary mirror. “These materials have very different thermal expansion properties,” Nagler said. “We had to have an interface between them that won’t stress either material.”
A long-duration NASA Super-Pressure Balloon will loft the EXCITE mission’s SUV-sized payload, with an engineering test flight planned as early as fall of 2023.
Ideal Design Solution for NASA’s Custom Parts
AI-assisted design is a growing industry, with everything from equipment parts to entire car and motorcycle chassis being developed by computers.
The use case for NASA is particularly strong, McClelland said.
“If you’re a motorcycle or car company,” McClelland said, “there may be only one chassis design that you’re going to produce, and then you’ll manufacture a bunch of them. Here at NASA, we make thousands of bespoke parts every year.”
3D printing with resins and metals will unlock the future of AI-assisted design, he said, enabling larger components such as structural trusses, complex systems that move or unfold, or advanced precision optics. “These techniques could enable NASA and commercial partners to build larger components in orbit that would not otherwise fit in a standard launch vehicle, they could even facilitate construction on the Moon or Mars using materials found in those locations.”
Merging AI, 3D printing or additive manufacturing, and in-situ resource utilization will advance In-space Servicing, Assembly, and Manufacturing (ISAM) capabilities. ISAM is a key priority for U.S. space infrastructure development as defined by the White House Office of Science and Technology Policy’s ISAM National Strategy and ISAM Implementation Plan.
This work is supported by the Center Innovation Fund in NASA's Space Technology Mission Directorate as well as Goddard’s Internal Research and Development (IRAD) program.
Suggested Items
Spotlight on PEDC: Filbert Arzola
12/19/2024 | Andy Shaughnessy, Design007 MagazineIPC and FED have teamed up to create a new PCB design conference in Vienna, Austria. The Pan-European Electronics Design Conference (PEDC) takes place Jan. 29-30 at the NH Danube City hotel in Vienna. Raytheon’s Filbert Arzola is presenting “Engineering and Adapting Model-based PCB Design in Step with Sustainability and Digital Twins” at PEDC. I asked Filbert to discuss what attendees can expect from his class.
Avnet Insights: Engineers Outline Opportunity for AI
12/19/2024 | AvnetFor the fourth consecutive year, Avnet, Inc. (Nasdaq: AVT) will release its Avnet Insights survey, which has been keeping a pulse on how engineers are responding to the market since 2021. This year’s survey examines technology’s new frontier: Artificial Intelligence, and the promise – and challenges – it presents for product design.
IPC/WHMA Launches Groundbreaking Online Course on Wire Harness Design
12/18/2024 | IPCIPC/WHMA is excited to announce the launch of its new online instructor-led training course, "Introduction to Wire Harness Design I," available now through the IPC EDGE Learning Management System.
The Companion Guide to 'Designing for Reality' by Matt Stevenson Now Available
12/19/2024 | I-Connect007I-Connect007 is excited to announce the release of "The Companion Guide to...Designing for Reality," written by Matt Stevenson of ASC Sunstone Circuits. This essential resource builds on the foundational insights presented in "The Printed Circuit Designer’s Guide to... Designing for Reality" and delivers advanced strategies for scaling PCB production.
Global PCB Connections: Following DFM Rules Leads to Better Boards
12/18/2024 | Jerome Larez -- Column: Global PCB ConnectionsAs a PCB field applications engineer, ensuring smooth communication between PCB designers and fabricators is one of my frequent challenges. A critical part of that dialogue is design for manufacturing (DFM). Many designers, even experienced ones, often misunderstand or overlook important DFM considerations. They may confuse design rules with manufacturing minimums, leading to technically feasible designs that are difficult or costly to produce. In this column, I will clarify some common DFM guidelines and help designers understand the difference between “design rules” and “minimums” while sharing best practices that will simplify the production process and ensure the highest quality PCB.