-
- News
- Books
Featured Books
- pcb007 Magazine
Latest Issues
Current IssueSales: From Pitch to PO
From the first cold call to finally receiving that first purchase order, the July PCB007 Magazine breaks down some critical parts of the sales stack. To up your sales game, read on!
The Hole Truth: Via Integrity in an HDI World
From the drilled hole to registration across multiple sequential lamination cycles, to the quality of your copper plating, via reliability in an HDI world is becoming an ever-greater challenge. This month we look at “The Hole Truth,” from creating the “perfect” via to how you can assure via quality and reliability, the first time, every time.
In Pursuit of Perfection: Defect Reduction
For bare PCB board fabrication, defect reduction is a critical aspect of a company's bottom line profitability. In this issue, we examine how imaging, etching, and plating processes can provide information and insight into reducing defects and increasing yields.
- Articles
- Columns
- Links
- Media kit
||| MENU - pcb007 Magazine
Estimated reading time: 5 minutes
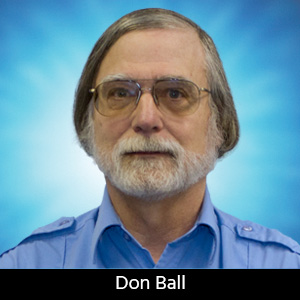
The Chemical Connection: Wet Process Start-up Considerations
Are you (or your company) considering starting your own PCB fabrication process? After the most recent IPC APEX EXPO, maybe you’ve made connections to help you with your start-up, but do you have a solid game plan? If you are new to managing a PCB shop, the first thing to know is that wet processing is essential in making PCBs. Wet processing steps, such as cleaning, developing, etching, and stripping, are among the many steps in the PCB fabrication process that require thorough planning. When you are just starting to get involved in this industry, keeping track of all this can feel overwhelming. If you fit in this category, it’s best to start with the basics and work your way up. Here are a few considerations and base essentials to aid you in starting up the wet processes for your new facility.
Scale of Production
Before you start planning out how you want your PCB shop to function, you will need to lay out your goals. For instance, it’s important to know the type of circuit boards you plan to make, as well as how many you want to make and how quickly you want to produce them. Knowing this information is vital because it will drastically shape your manufacturing process. Depending on your products, you may have to utilize different photoresists and wet processing chemicals (i.e., different cleaning, developing, etching, and stripping solutions).
In addition, you need to know the scale of your production so you can ensure that you get the suitable equipment for your level of manufacturing. For example, if you are planning to run a facility with a large output of panels per day, a multi-chambered etch machine may be something to consider (Figure 1). This is because the longer the etch chamber, the faster you can run the conveyor speed while maintaining the same processing time. This increased conveyor speed with a larger etch chamber means that more panels can be inside the etch chamber at the same time. Keep in mind that a larger machine also means that it will take up more floor space; the trade-off for increasing production is committing to a capital investment and sacrificing some space.
Utilities
When you are planning to start a PCB shop, you need to consider not only what equipment you’ll need, but also the basic utilities required and how those will be connected. The primary utilities/base necessities are electricity, water, and ventilation. Typically, utilities run 15–20% of equipment cost. Although these utilities are a necessity for any manufacturing facility, some situations may need additional considerations. For instance, when it comes to your electrical needs, not only do you have to ensure you get the power you need to run the equipment, but you need to consider where electrical cabinets should be located. If you are utilizing an alkaline etcher, you’ll need something to help regulate the airflow through the machine to ensure optimal etching.
Available Workspace
As I mentioned, the floor space requirements of your equipment should be a major consideration when planning your facility. When deciding on the equipment you need to meet production goals, you must find a balance between available floor space and how to meet your production needs. When working on the layout of your facility, keep in mind that you’ll need to reserve additional space to ensure that people can easily run and maintain your equipment. Poor manufacturing floor design can create inconvenient situations for operation and maintenance, which can negatively impact the longevity and efficiency of your equipment. Having an awareness of space is vital when planning your process because you need a layout that will get your equipment inside the facility and leave enough space for it to be operated efficiently.
Process Locations
When planning out your wet process, you may want to consider its location relative to other equipment. This is because corrosion is a given with etching equipment. Although the equipment safely contains the etching chemicals, the process tends to create a corrosive environment; anything metal in the area that lacks some form of corrosion resistance will experience corrosion over time. Etching equipment is often kept in its own room to account for this phenomenon. Therefore, if you have an expensive machine testing your printed circuit boards, you do not want it in the same room as your etching machine.
Waste Management
Producing PCBs generates many different forms of waste. For wet processing, contaminated rinse water and excess etchant are common waste streams. As you process a panel through one of the wet processes, it’s normal to rinse it before it goes to the downstream processes. These rinse waters become contaminated with wet processing chemicals and need to be treated before disposal. This is something that you can do in-house, but how you do it may depend on the wastewater regulations in your area. You may be required to precipitate any heavy metals out of the water to make it meet your discharge permit limits. In this case, the precipitated metal sludge is another waste steam that will need to be handled. Typically, this sludge is filtered off from the water, dried, drummed, and sent off to a waste treatment facility.
Excess etchant is another waste product you need to plan for. As you etch your PCBs and make chemistry adjustments, you will accumulate etchant in your etching machine over time. This excess etchant needs to be pumped out before the level gets too high in your etcher bath. Since the excess etchant usually doesn’t meet quality requirements for reuse, and because it is concentrated, it is common practice to pump the excess etchant into a barrel that will get shipped to a waste treatment facility.
Conclusion
If you are looking for a good place to start planning your PCB fabrication process, I hope the information I’ve provided here gives you a better idea of what to expect. Knowing about these matters and preparing for them ahead of time can make planning your wet process—and your job—much easier.
This column originally appeared in the February 2023 issue of PCB007 Magazine.
More Columns from The Chemical Connection
The Chemical Connection: Through-glass Vias in Glass SubstratesThe Chemical Connection: Reducing Defects in Circuit Board Production
The Chemical Connection: Common Misconceptions in Wet Processing
The Chemical Connection: Surface Finishes for PCBs
The Chemical Connection: Earthquakes, Astronauts, and Aquatics—A Lighter Look at the Past
The Chemical Connection: Better Fabs Attract a Better Workforce
The Chemical Connection: Can Changing Spray Nozzles Improve My Etch Quality?
The Chemical Connection: Getting the Best from Your Cupric Chloride Etchant